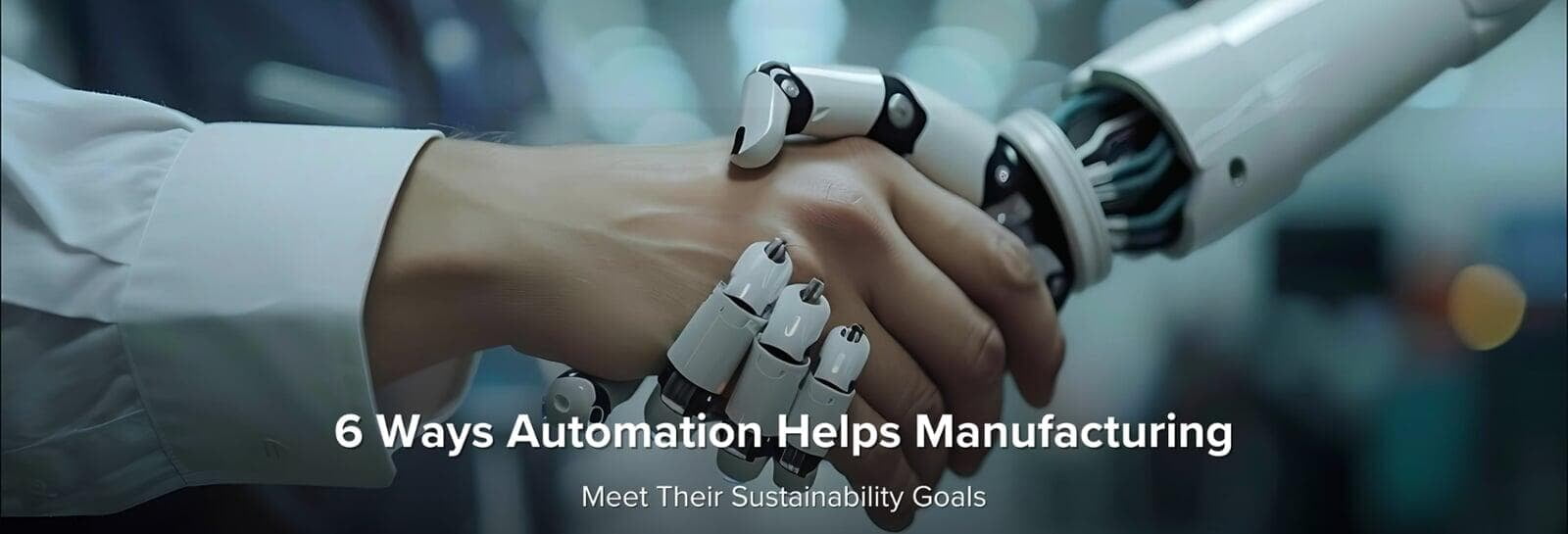
The modern manufacturing industry is undergoing a profound transformation, driven by the dual forces of technological advancement and the increasing demand for sustainability. As governments, consumers, and stakeholders push for environmentally responsible practices, manufacturers are being called to reduce their environmental impact and conserve energy. Automation has emerged as a critical tool in helping manufacturing companies meet their energy efficiency and sustainability goals. Through innovations like smart manufacturing, AI-driven process optimization, and industrial IoT (Internet of Things), automation is revolutionizing how manufacturers approach sustainability.
In this blog, we will explore how automation enables manufacturers to achieve their energy efficiency and sustainability targets, backed by real-time metrics and industry insights.
Reducing Energy Consumption with Process Automation
One of the most significant ways automation supports energy efficiency is by reducing the energy consumption of manufacturing processes. Manufacturers can significantly decrease their energy use by automating tasks that were previously performed manually or by semi-automated systems.
1) Smart HVAC Systems
2) Process Optimization
Enabling Predictive Maintenance to Minimize Waste
1) Predictive Maintenance with IoT Sensors
Waste Reduction and Material Efficiency
1) Robotic Automation for Precision
Energy-Efficient Lighting with Automation
Lighting is another area where automation helps reduce energy consumption in manufacturing. Traditional factory lighting systems often remain on even when areas are unoccupied or during daylight hours, leading to unnecessary energy use. Automated lighting systems with motion and daylight sensors can adjust the intensity or turn off lights based on occupancy and natural light availability.
1) Automated LED Lighting Systems
Water Conservation Through Automation
Water is critical in many manufacturing processes, especially in textiles, food and beverage, and chemicals. Automation technologies are helping manufacturers optimize water usage, recycle water more efficiently, and minimize water waste.
1) Automated Water Recycling Systems
Smart Energy Monitoring and Optimization
One of the most impactful ways automation drives energy efficiency is through smart energy monitoring systems. These systems continuously track energy usage across the facility, analyzing data to identify opportunities for reducing consumption. Automated systems can then make real-time adjustments, such as powering down machines during idle times or reducing heating in unoccupied areas.