Kiara Machine Vision - Case Studies
FIBC Defect Identification
AI Powered defect identification, auto recutting of material for minimal wastage. Read more...
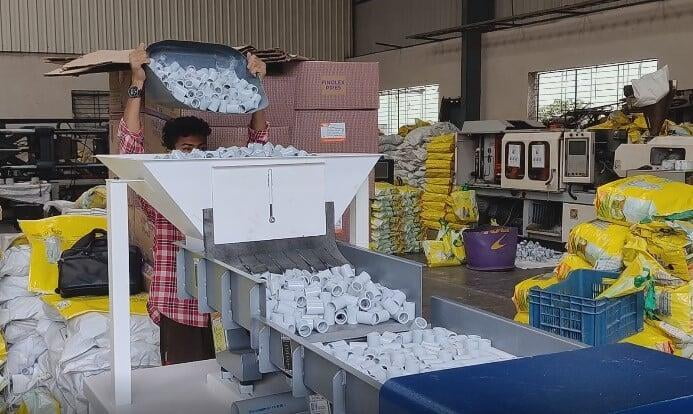
PVC Parts Counting
Automatic counting of variety of plastic parts with AI technology.
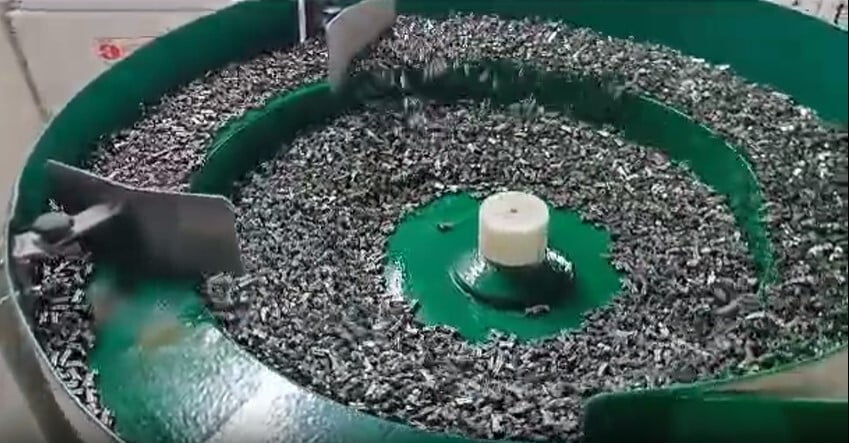
Bulk Metal Parts Counting
Counted Metal Parts using AI Vision
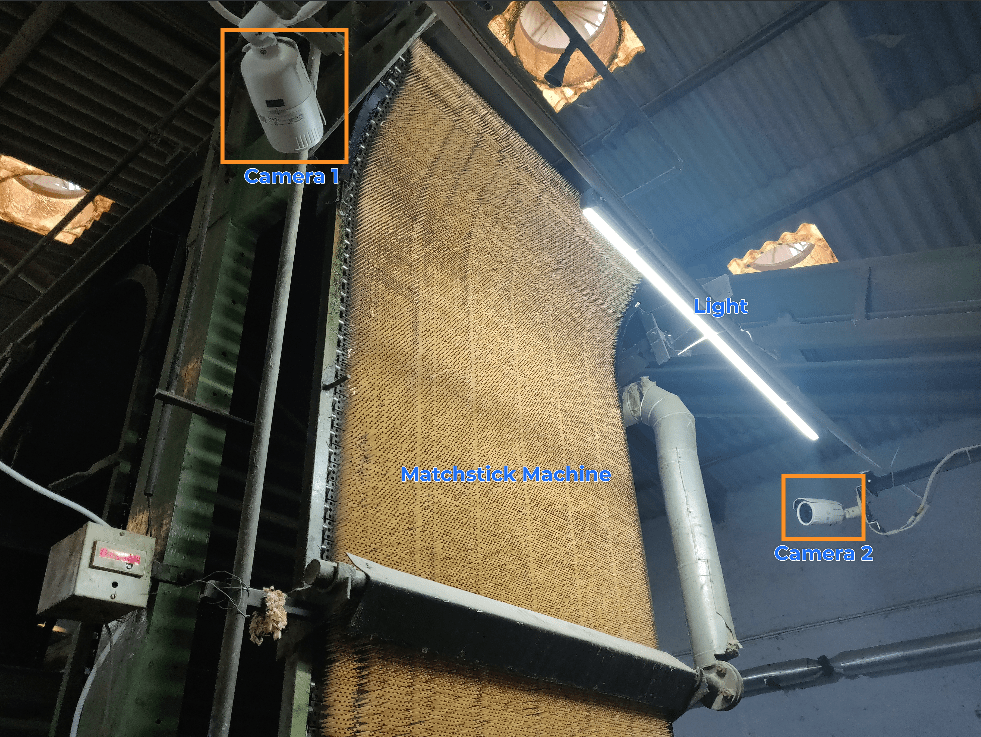
Headless Match Sticks Inspection
identifying defective matchsticks that do not have heads.
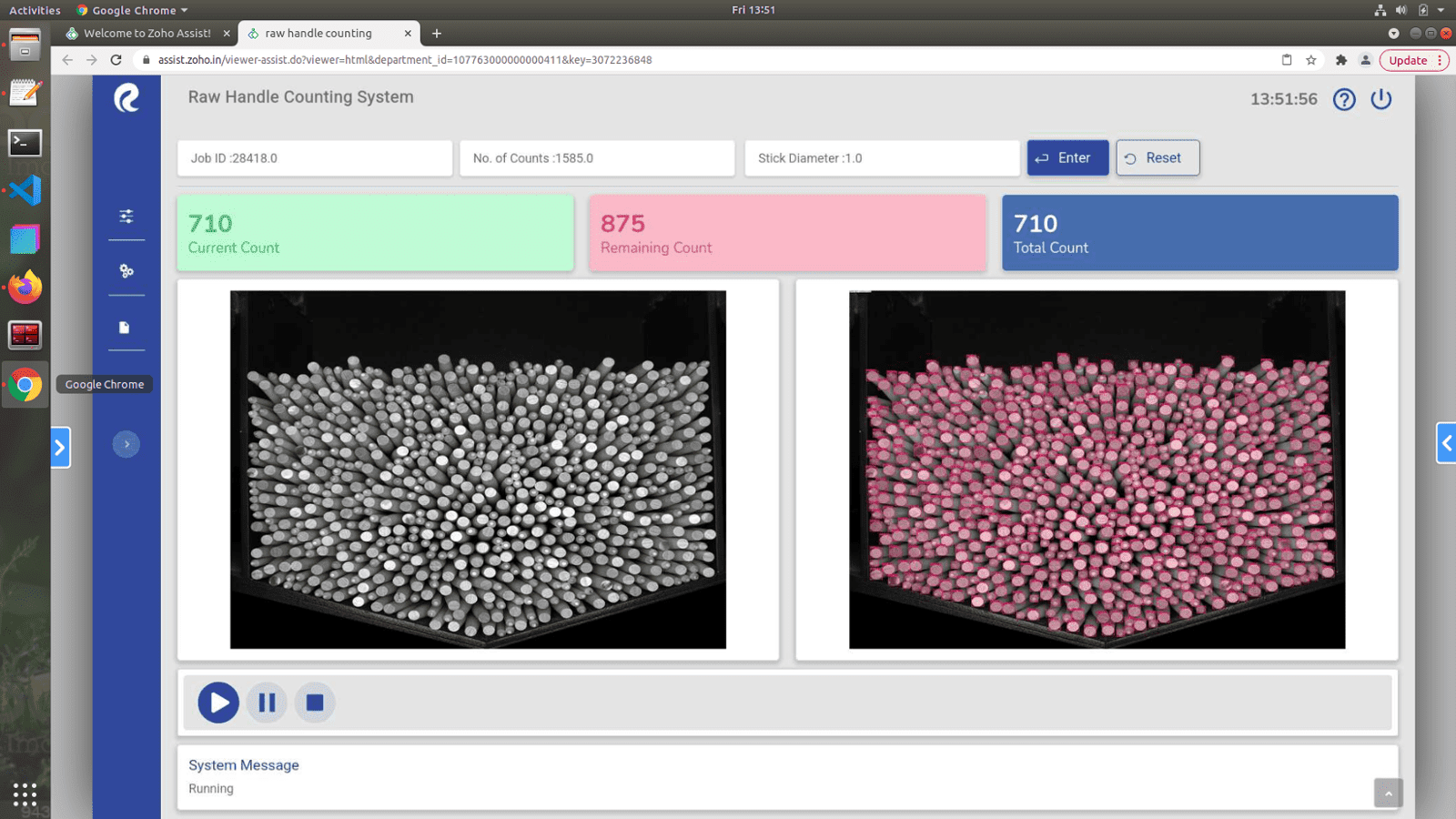
Handle Counting System
Bunch counting and packing of long elongated parts using AI technology.
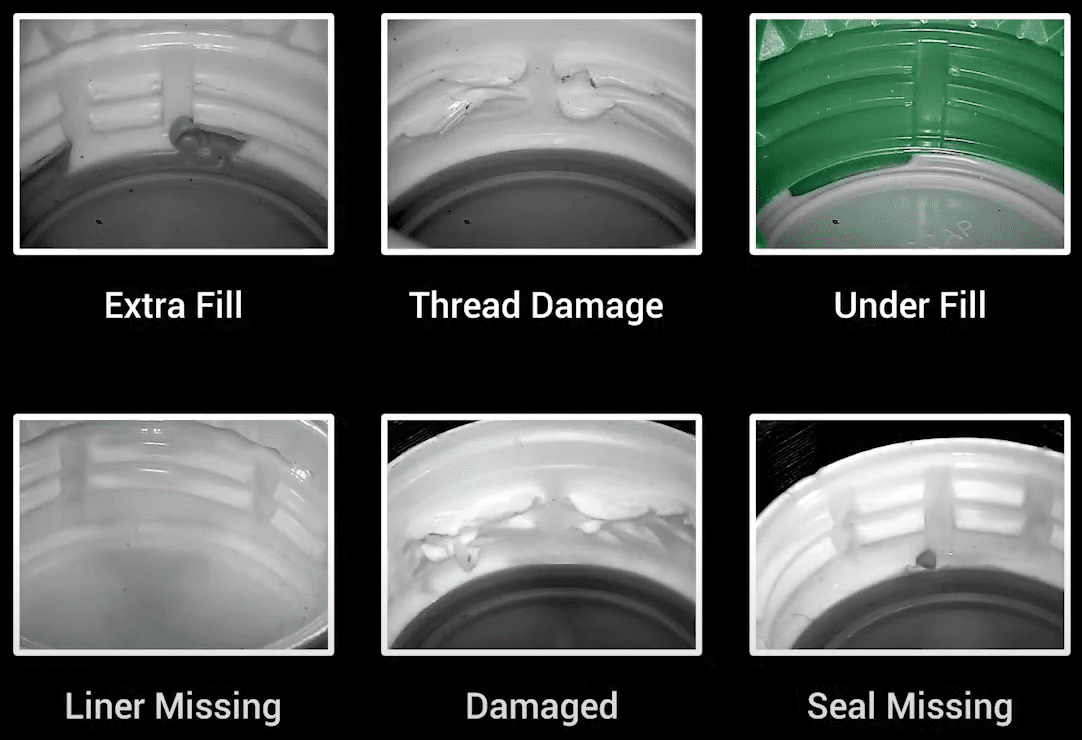
Sorting Defective Caps
Identifying defective caps and sorting the defect caps into respective category.
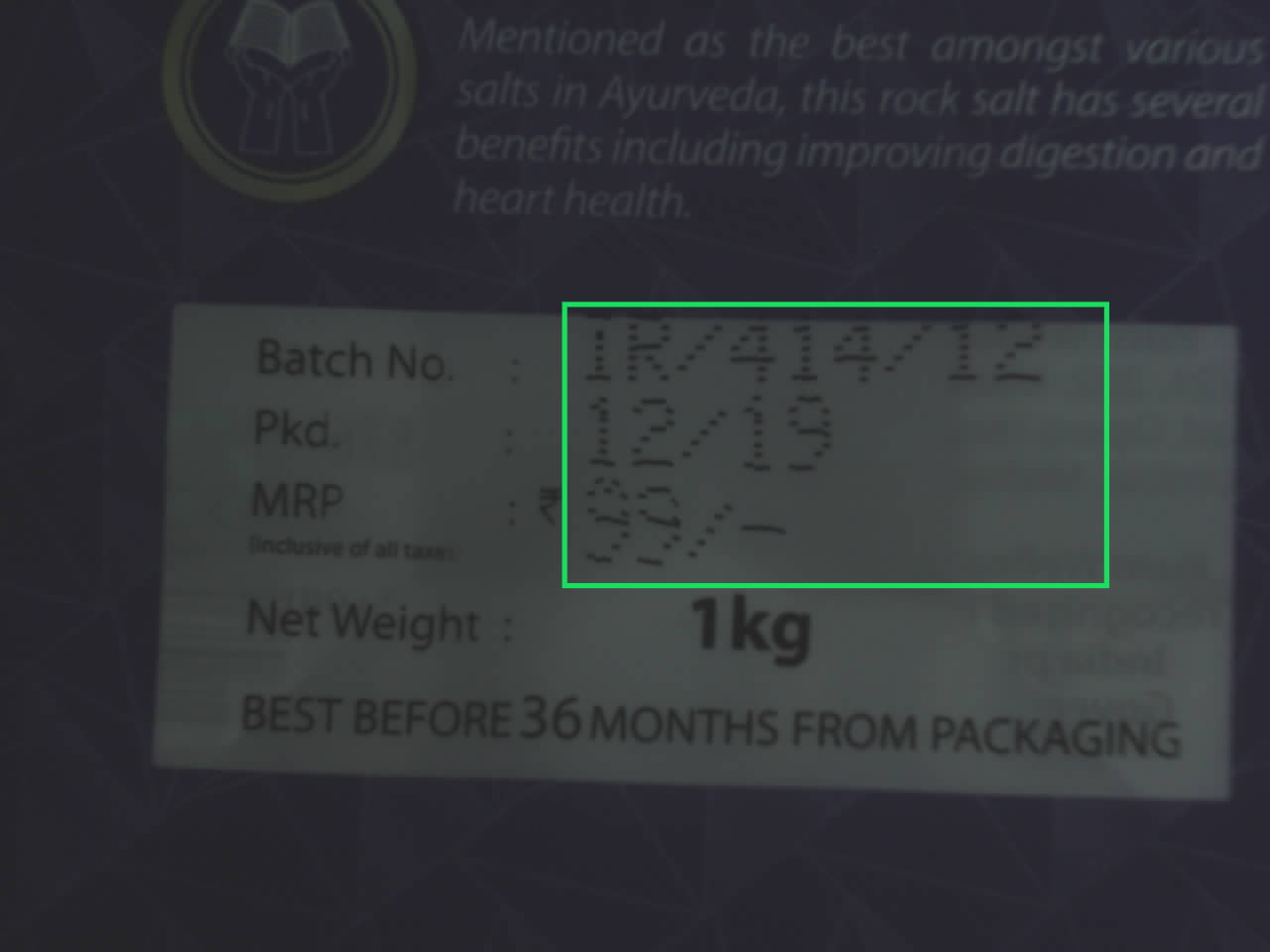
Expiry Date Print Inspection
Inspect Expiry date and batch details printed on tetrapack
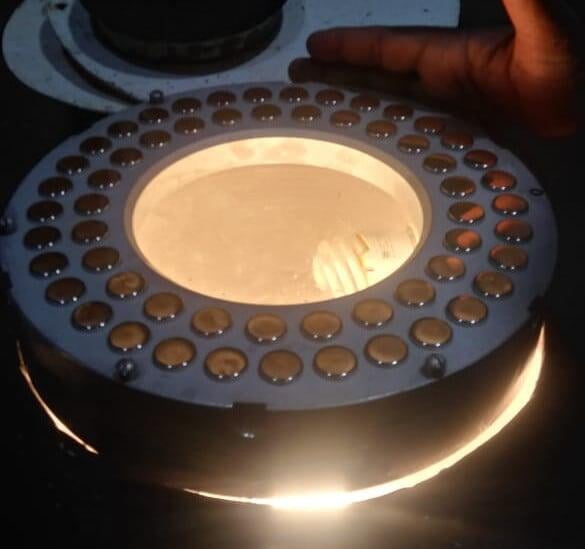
Hole Choke Identification
Inspecting chokes of micropores in a spinneret.
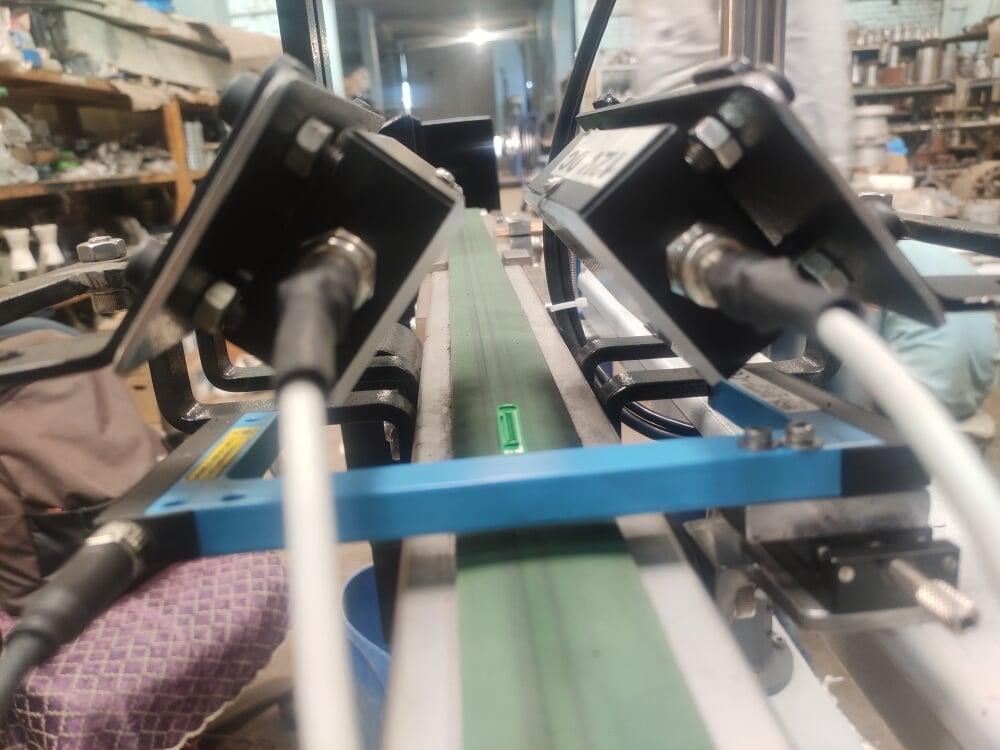
Plastic dripper defect Identification
High speed inspection and rejection of defective drippers.
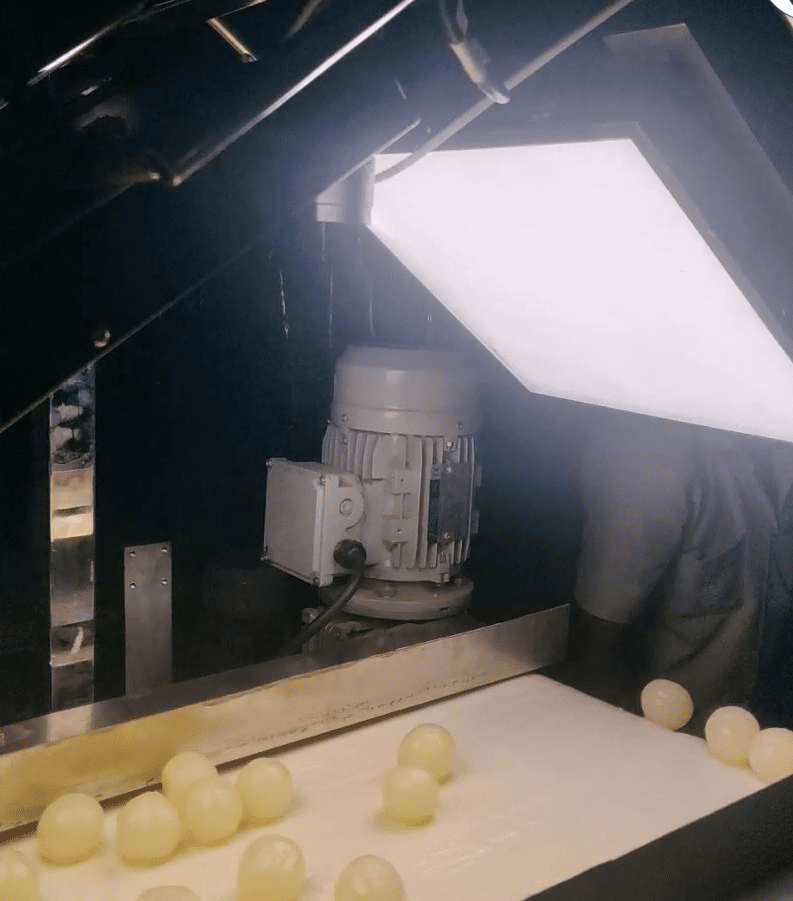
Sweets Counting on Conveyor
Counting sweets moving on a conveyor using AI technology.
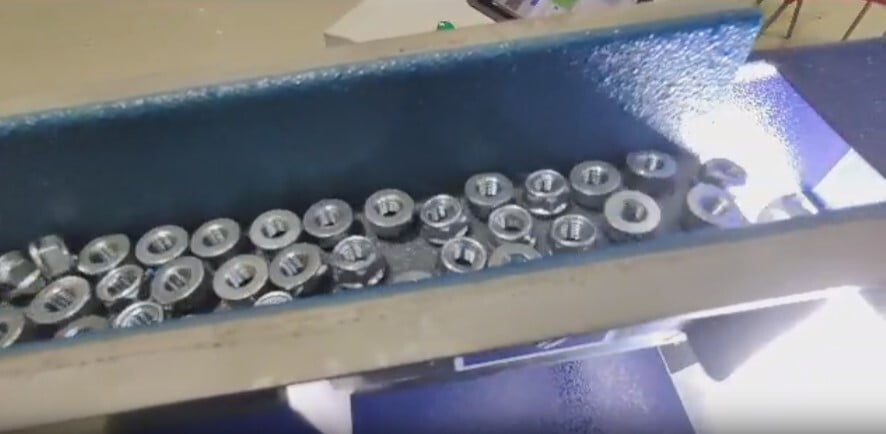
High Speed Fasteners Counting
Bulk and high speed fasteners counting and packing.
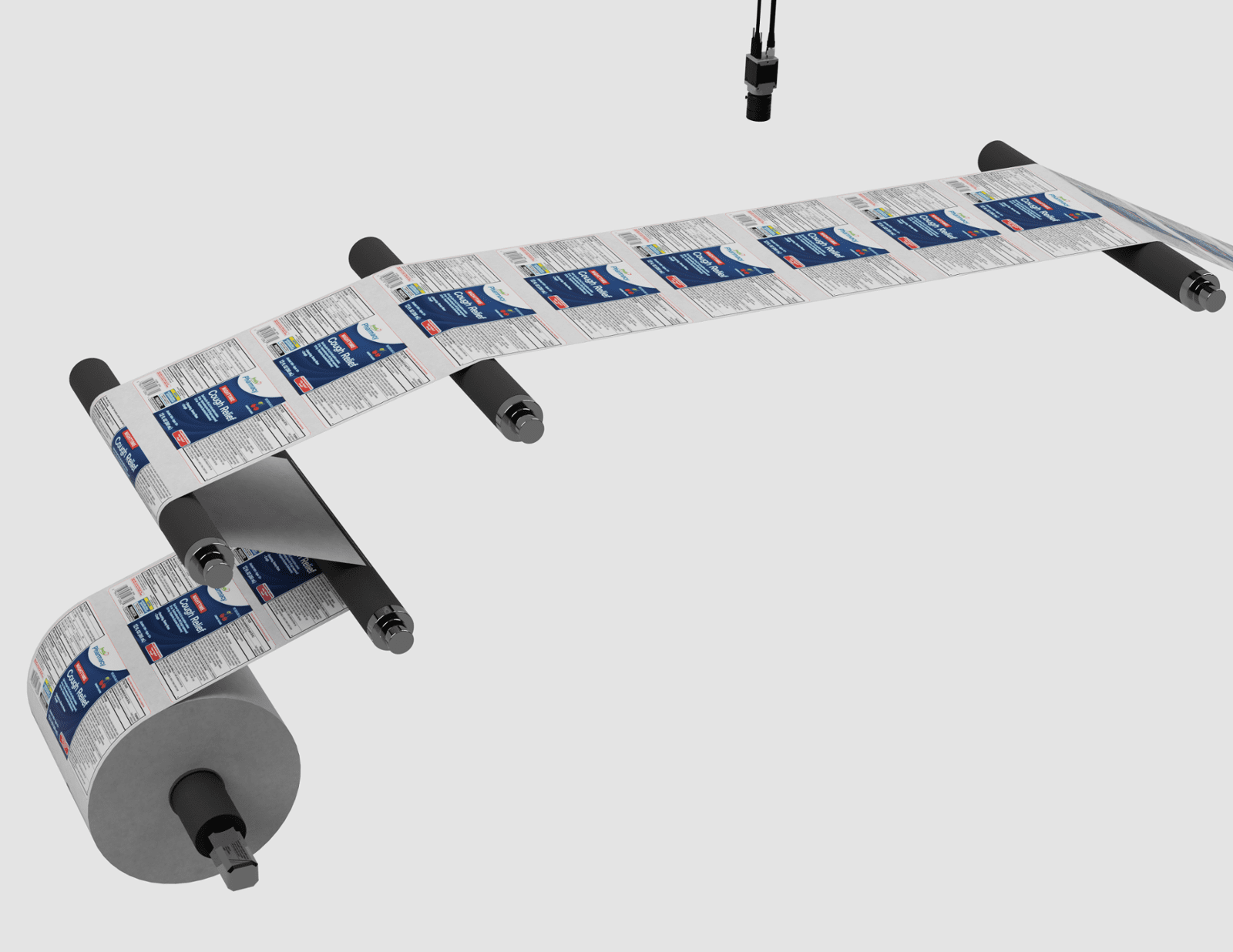
Label Surface Inspection
Inspection of label sheets to identify defects as small as 0.09mm.