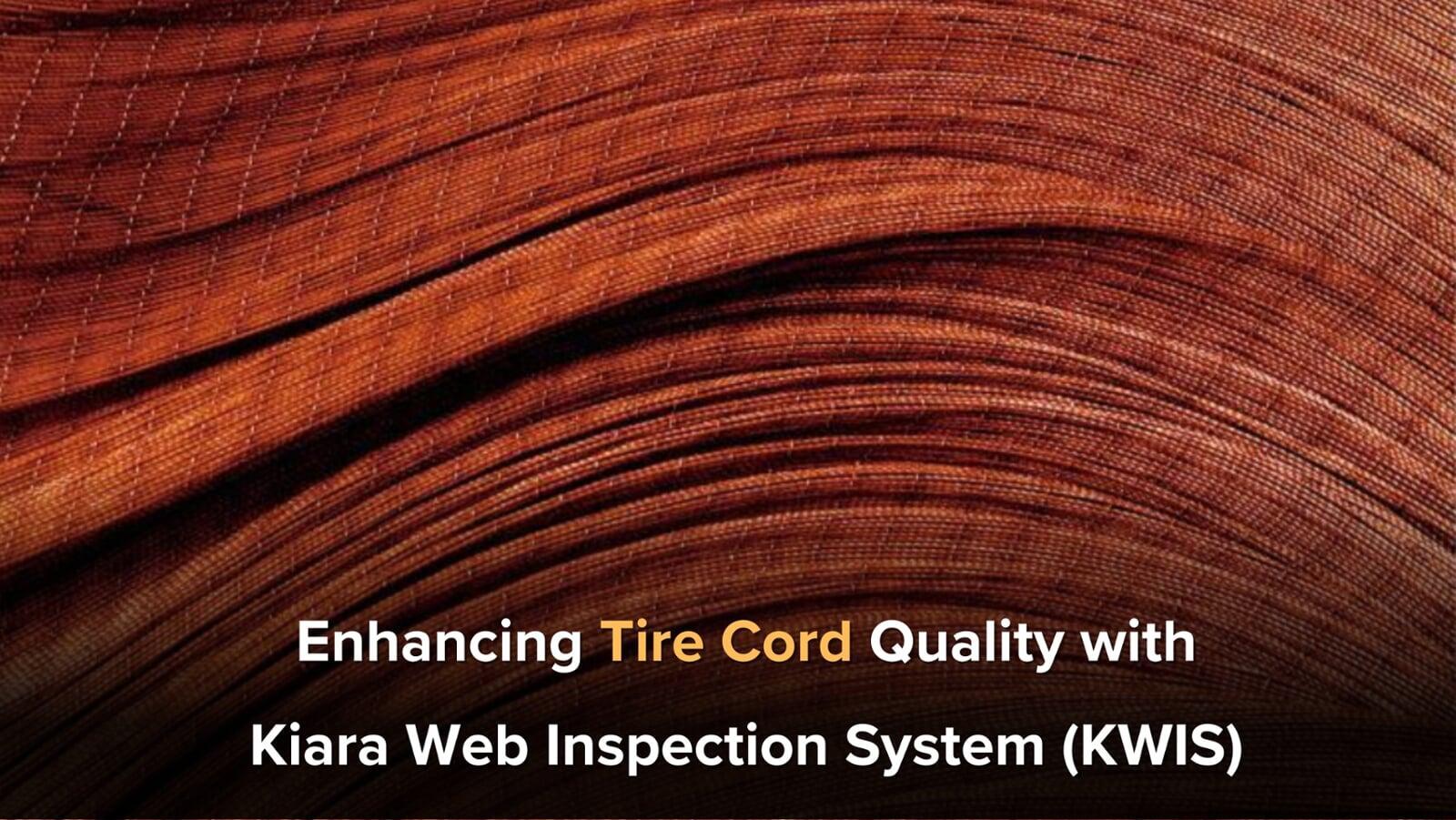
The Challenges in Tire Cord Manufacturing
High-End Synthetic Materials in Tire Cord Production- Tire cord manufacturing uses advanced synthetic materials like aramid, nylon, and polyester, requiring precise weaving to ensure uniformity and strength.
Limitations of Traditional Inspection Methods- Conventional inspection relies on human eyes and human expertise, which, while somewhat effective, is susceptible to human error and defects passing by in the inspection process.
Impact on Defect Detection and Manufacturing Costs- Inconsistent or manual defect detection leads to higher production of low-quality cords, increasing material waste and manufacturing expenses.
Rising Demand for High-Performance Tires- As the market demands better-performing tires, manufacturers must enhance quality control to meet strict industry standards and customer expectations.
Introducing the Kiara Web Inspection System (KWIS)
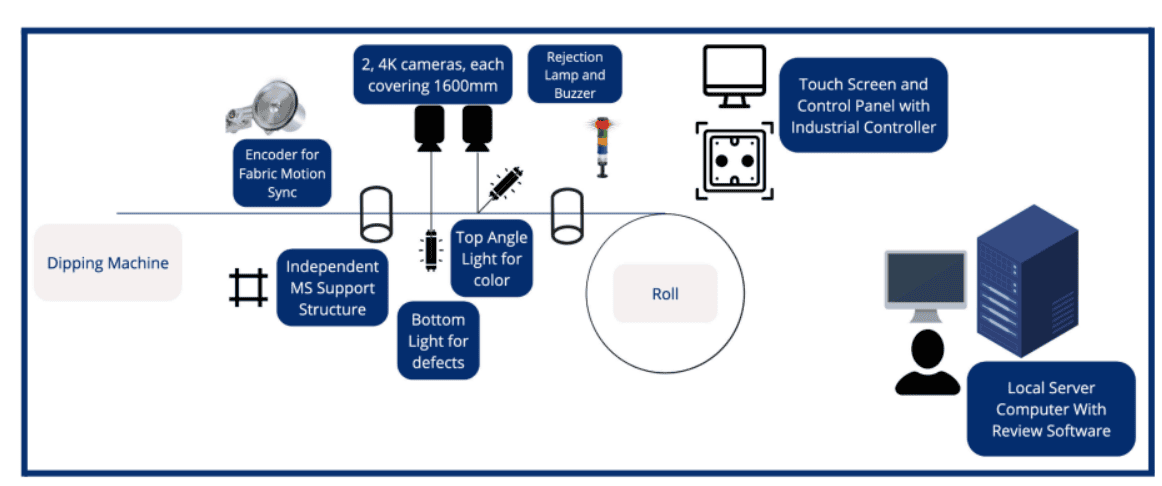
Real-Time Defect Detection and Classification
Comprehensive Defect Detection- KWIS identifies a wide range of defects, including broken weft, loose warp ends, tight warp ends, and higher weft density.
Advanced Detection of Transparent Stains- The system excels in detecting transparent stains, which are difficult to identify manually but can disrupt the dipping process and impact final product quality.
High-Resolution Imaging and AI Algorithms- KWIS utilizes high-resolution imaging and AI-driven algorithms to capture and classify defects with precision.
Data-Driven Quality Control- The system provides manufacturers with comprehensive quality data, enabling informed decision-making and process optimization.
Proactive Defect Prevention- KWIS helps production teams identify recurring issues early and implement corrective actions before defects escalate into major production setbacks.
Reducing Low-Quality Production and Optimizing Yield
By implementing KWIS, tire cord manufacturers have reported up to a 30% reduction in low-quality output. This improvement translates to significant cost savings, as fewer materials are wasted, and production efficiency is maximized. Automated inspection at both the weaving and finishing stages ensures that defective rolls are flagged early, reducing the chances of defective materials being processed further down the production line. The system also enables real-time tracking and reporting, allowing manufacturers to make data-driven decisions that enhance productivity and quality control efforts. The benefits of defect prevention extend beyond cost savings—they contribute to increased customer satisfaction by delivering consistently high-quality tire cords that meet or exceed industry standards.