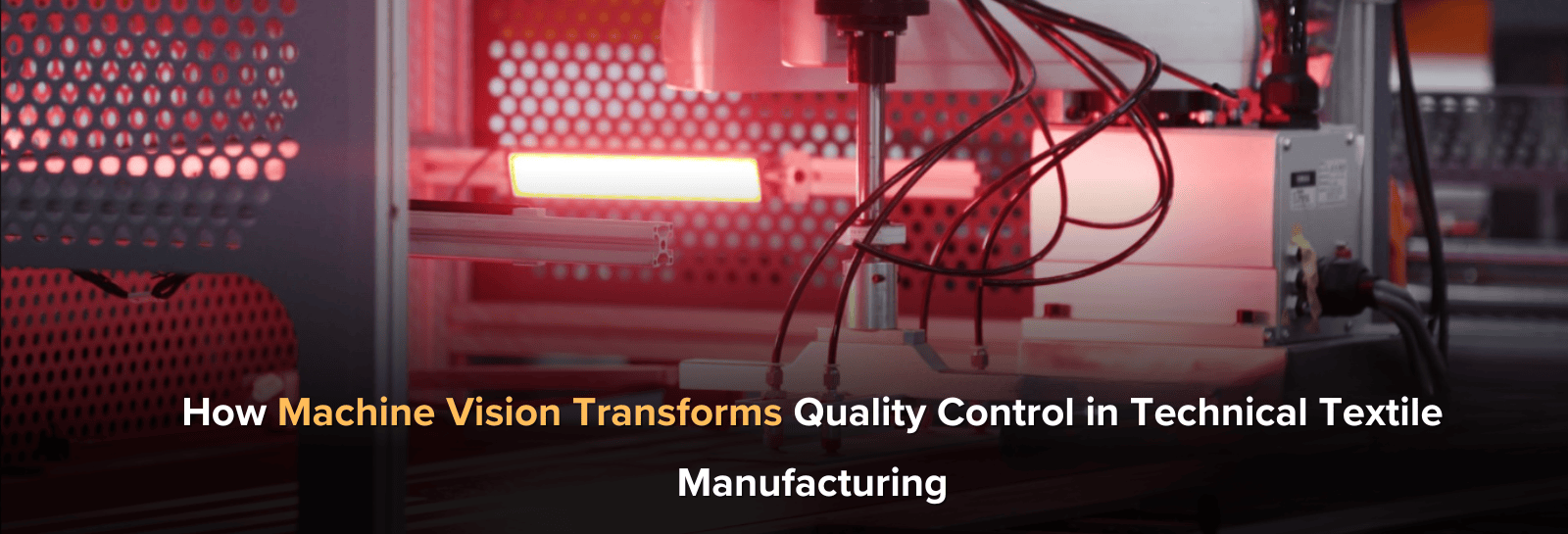
The Role of Quality Control in Technical Textile Manufacturing
Quality control in technical textile production ensures durability, functionality, and compliance with industry standards. Manufacturers must detect defects such as:
Weaving defects (e.g., broken or missing threads, inconsistent patterns) can weaken the structural integrity of textiles used in applications such as airbags, conveyor belts, and industrial filters.
Coating imperfections (e.g., uneven application, cracks, bubbles) that may impact water resistance, fire retardancy, or UV protection in specialized fabrics.
Color and shade variations can result in batch inconsistencies, particularly in applications where aesthetic uniformity is critical, such as automotive interiors and protective clothing.
Foreign contaminants (e.g., dirt, oil, fibers from different materials) can compromise the functionality of medical textiles, geotextiles, or food-grade fabrics.
Structural inconsistencies (e.g., varying thickness and incorrect density) can affect the mechanical properties of high-performance textiles, affecting their tear resistance, tensile strength, and thermal insulation.
Traditional quality control methods rely on human inspectors, who manually check fabric rolls under visual or UV light. This approach has limitations, including fatigue-induced errors, slow processing speeds, and difficulties detecting micro-defects. Machine vision overcomes these challenges by automating the inspection process with high-speed, high-precision imaging.
How Machine Vision Works in Textile Inspection
1) High-Resolution Imaging
2) Advanced Image Processing
AI-powered software processes captured images, applying filters, edge detection, and pattern recognition techniques to identify inconsistencies. Deep learning models trained on large datasets of defect images improve the accuracy of defect classification over time. These models can differentiate between acceptable variations and actual defects, reducing false positives and increasing inspection reliability.
3) Real-Time Data Processing
4) Automation and Robotics Integration
Key Features of Machine Vision in Quality Control
1) 99.99% Defect Detection Accuracy
AI-driven machine vision systems achieve near-perfect accuracy by analyzing millions of pixels per second, surpassing human inspection capabilities. These systems continuously refine their defect detection models through self-learning algorithms, ensuring that even the most complex textile patterns and coatings are scrutinized precisely.
2) Non-Contact, High-Speed Inspection
Unlike manual inspection, machine vision operates at high speeds without physically touching the fabric, ensuring uninterrupted workflow and enhanced production efficiency. This is particularly beneficial for delicate or highly sensitive materials, such as conductive textiles and lightweight composite fabrics, where manual handling could cause damage or introduce contamination.
3) Adaptive Learning for Continuous Improvement
Deep learning algorithms continuously learn from new defect patterns, improving detection accuracy and reducing false positives. This means that even as textile designs and production methods evolve, machine vision systems remain adaptive and capable of precisely identifying emerging defect types.
4) Multi-spectral and Hyperspectral Imaging
Beyond visible light detection, hyperspectral imaging detects chemical compositions, contamination, and subtle variations in fabric coatings, which are essential for high-performance technical textiles. This capability is instrumental in medical and protective textiles, where factors such as antimicrobial coatings and fire retardancy treatments must be applied consistently.
5) Seamless Integration with Industry 4.0
Machine vision systems integrate with IoT-enabled manufacturing setups, allowing real-time monitoring, predictive maintenance, and automated decision-making. This inter-connectivity enables manufacturers to implement innovative production lines that self-optimize based on real-time quality data, significantly reducing waste and operational costs.
Benefits of Machine Vision in Technical Textile Manufacturing
1) Enhanced Product Quality— Machine vision helps manufacturers meet stringent quality standards by ensuring defect-free fabric. This reduces customer complaints and product recalls, which improves brand reputation and increases customer satisfaction, particularly in industries with mission-critical textile performance.
2) Increased Production Efficiency- Automated inspection enables manufacturers to achieve up to 300% faster production speeds, minimizing bottlenecks and optimizing throughput. Higher processing speeds allow large-scale textile operations to maintain high output levels without sacrificing quality control.
3) Reduced Material Waste and Costs—Machine vision prevents defective rolls from being processed further by identifying defects early in the production process, reducing raw material waste and rework costs. Automated defect categorization also allows for targeted corrective measures, minimizing unnecessary material scrapping.
4) Lower Energy Consumption—Machine vision-driven automation optimizes resource utilization, reducing energy consumption and contributing to sustainable manufacturing. Manufacturers can significantly reduce energy usage per output unit by eliminating redundant inspection steps and reducing reprocessing requirements.
5) Regulatory Compliance and Certification- Technical textiles used in aerospace, medical, and automotive applications must adhere to strict quality regulations. Machine vision ensures compliance with ISO, ASTM, and other industry-specific standards, providing documented quality assurance that facilitates smoother regulatory approvals and market access.
Conclusion
Machine vision revolutionizes quality control in technical textile manufacturing by offering unparalleled accuracy, speed, and efficiency. By leveraging AI, deep learning, hyperspectral imaging, and real-time analytics, machine vision systems ensure 99.99% defect detection accuracy, 300% faster production speeds, and significant cost savings. Integrating these systems with Industry 4.0 technologies enables real-time monitoring, predictive maintenance, and intelligent decision-making, driving a shift towards smart manufacturing.
As the demand for high-performance technical textiles grows, machine vision technologies will play an increasingly vital role in ensuring quality, efficiency, and sustainability. Future advancements in AI, augmented reality-assisted inspection, blockchain-based traceability, and quantum-enhanced image processing will further refine textile inspection capabilities. Manufacturers who invest in AI-powered machine vision will gain a competitive edge by producing superior-quality textiles with reduced costs and minimal environmental impact. In an industry where precision and reliability are paramount, machine vision is no longer a luxury but a necessity for future-ready textile manufacturing.