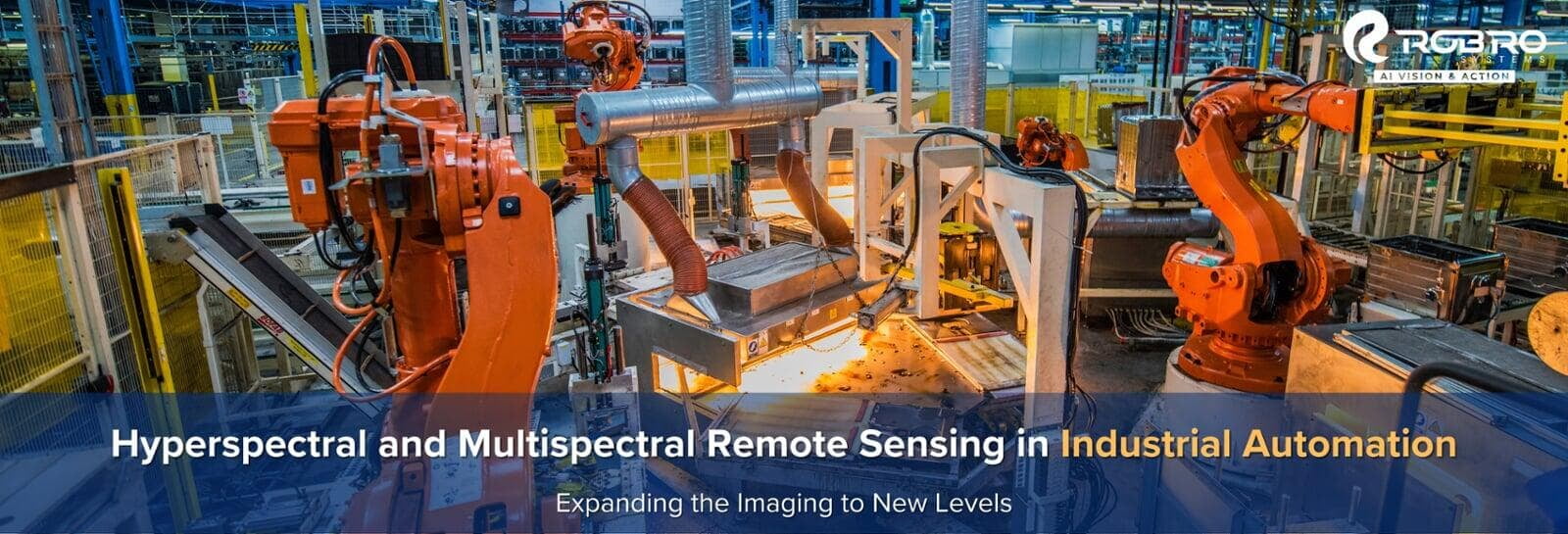
In the ever-evolving area of industrial automation, remote sensing technologies like hyper-spectral and multi-spectral imaging have proven to be smarter, innovative and transformative tools. When paired with AI and machine vision, these advanced imaging technologies enable manufacturers to up-stand their inspection processes, optimize production lines, and improve overall product quality.
In this we will help you understand the core differences between hyper-spectral and multi-spectral remote sensing and explore how these technologies are changing the industrial automation landscape.
Hyper-spectral vs. Multi-spectral Imaging: A Primer
Before getting into the industrial application, let's understand the difference between hyper-spectral and multi-spectral imaging.
- Hyper-spectral Imaging (HSI) captures a vast range of wavelengths across the electromagnetic spectrum, often in hundreds of narrow spectral bands. This granularity enables the system to detect minute differences in materials, making it highly suitable for applications requiring detailed analysis for factory automation.
- Multi-spectral Imaging (MSI) on the other hand, captures fewer bands (typically between three to ten) but over broader wavelengths. While it doesn’t provide the same depth of information as hyper-spectral imaging, MSI is advantageous in scenarios requiring faster, more generalized data collection across large areas.
In industrial automation, both technologies are pivotal. Their ability to inspect, monitor, and analyze materials with unprecedented accuracy is opening doors to smarter, more efficient manufacturing systems.
Key Differences | Multi-spectral Imaging | Hyper-spectral Imaging |
Number of Bands | 3-10 | 100-300+ |
Spectral Resolution | Lower | Higher |
Cost | Relatively low | Higher |
Processing Time | Faster | Slower |
Applications | General detection, agricultural surveys | Precision material analysis, quality control |
Applications in Industrial Automation
1. Hyper-spectral Imaging in Manufacturing
2. Multi-spectral Imaging for Process Optimization
Integration of Remote Sensing with AI and Machine Vision
The integration of hyper-spectral and multi-spectral imaging with AI-powered machine vision systems further enhances the value of these technologies in industrial automation. By utilizing AI algorithms, manufacturers can process the massive amounts of data generated by these imaging systems in real time, allowing for faster, more accurate decision-making.
Hyper-spectral Imaging with AI: Hyper-spectral cameras collect numerous amounts of data. Analyzing these data manually would be time-consuming, but AI algorithms can process the data in milliseconds, detecting patterns or abnormalities that would otherwise be missed. This capability is crucial in industries like pharmaceuticals, where ensuring the purity of a compound or the correct mixture of ingredients is essential.
Multi-spectral Imaging with AI: AI systems combined with multi-spectral imaging can monitor manufacturing processes in real time, identifying trends or issues that could lead to machine failure or product defects. For example, in the automotive industry, AI-driven multi-spectral systems can inspect car components for cracks, dents, or paint inconsistencies, ensuring that every part meets strict quality standards before assembly.
A 2023 report by Markets and Markets indicated that companies integrating AI with hyper-spectral imaging saw a 30% increase in defect detection accuracy and a 25% reduction in operational costs due to better predictive maintenance and fewer machine failures.
The Future of Hyper-spectral and Multi-spectral Remote Sensing in Industrial Automation
As industries continue to embrace Industry 4.0 and smart factory concepts, the role of remote sensing technologies will only expand. The future of hyperspectral and multispectral imaging is closely tied to advancements in AI, the Internet of Things (IoT), and machine vision, all of which are critical components of modern industrial automation.
1. Real-time Remote Sensing: One key development on the horizon is the ability to perform real-time 3D hyperspectral imaging. This could revolutionize quality control in industries like aerospace and defense, where the slightest material defect could have catastrophic consequences.
2. Predictive Maintenance: Hyperspectral and multispectral imaging systems are also being used for predictive maintenance in manufacturing. These systems can help manufacturers avoid costly breakdowns and reduce downtime by continuously monitoring equipment for signs of wear or damage.
According to a report by McKinsey & Company, companies using predictive maintenance technologies, including hyper-spectral and multi-spectral imaging, have experienced a 50% reduction in unplanned downtime and a 20% extension in the life cycle of critical assets.