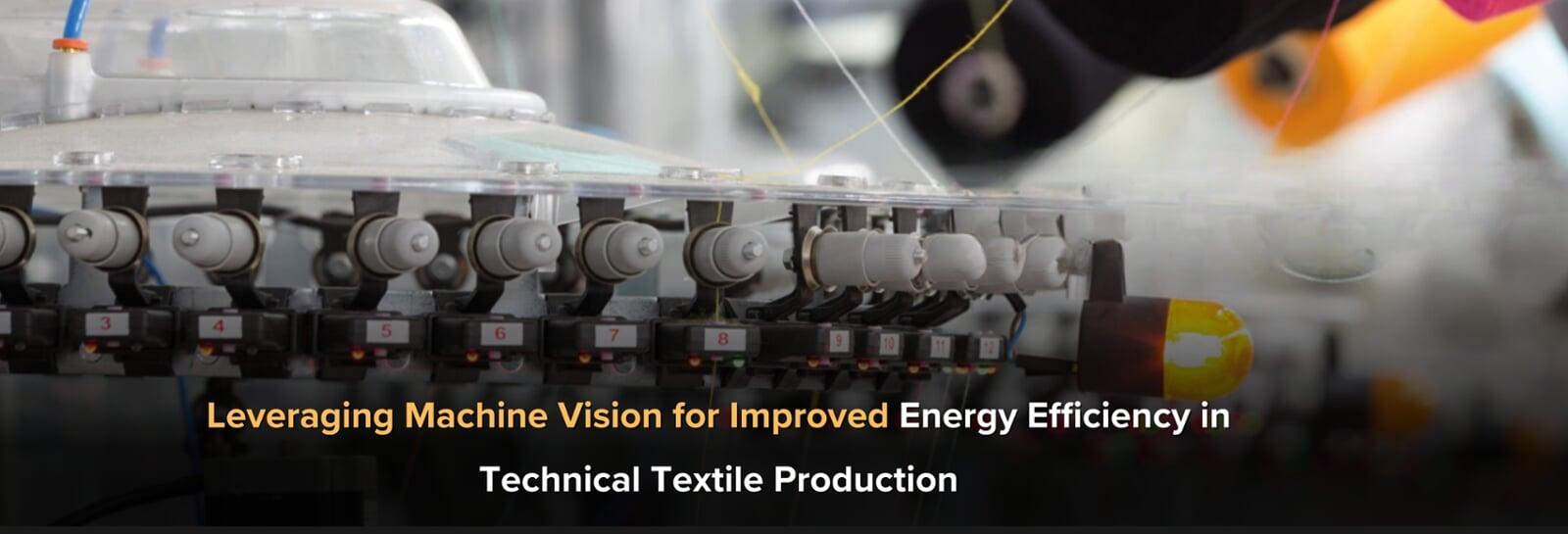
In the highly competitive world of technical textile production, manufacturers are under constant pressure to enhance operational efficiency, improve product quality, and reduce costs—particularly energy. As industries increasingly turn towards sustainability and energy optimization, one technology stands out for its ability to achieve these goals: machine vision. By integrating artificial intelligence (AI) and advanced image processing, machine vision systems are revolutionizing the way technical textile manufacturers monitor and manage their production processes, making them more energy-efficient and sustainable.
Machine vision systems, such as Robro Systems' Kiara Web Inspection System (KWIS), are at the forefront of this transformation. They allow textile manufacturers to optimize energy consumption, reduce waste, and improve quality control. This results in an enhanced bottom line, improved resource management, and a step towards greener, more sustainable manufacturing practices.
This blog explores how machine vision drives energy efficiency in technical textile production. It focuses on its applications in fabrics such as FIBC (Flexible Intermediate Bulk Containers), conveyor belt fabrics, tire cord fabrics, and shade nets. We will also delve into machine vision's benefits, challenges, and real-world applications, supported by industry insights and technical details, to show why this technology is indispensable for manufacturers today.
What is Machine Vision?
What is Machine Vision?
Machine vision refers to using cameras, sensors, and image processing software to enable a system to "see" and analyze visual data in real-time. It is used in manufacturing to inspect products, detect defects, and optimize processes. Machine vision relies on artificial intelligence (AI), deep learning, and machine learning algorithms to identify patterns, analyze images, and make decisions—similar to how the human eye processes visual information, but far more efficiently and accurately.
Machine vision is primarily used for fabric inspection in the technical textile industry. It ensures the highest product quality while minimizing defects and waste. By automating the inspection process, machine vision systems eliminate the need for manual inspection, which is often prone to human error and can be time-consuming. These systems offer high-speed, accurate defect detection and provide real-time data that manufacturers can use to optimize production and reduce energy consumption.
Machine vision is becoming more than just a quality control tool; it is a key driver of energy efficiency. By identifying issues early in the production cycle, manufacturers can prevent the energy waste associated with reprocessing or discarding defective materials. Additionally, machine vision helps streamline production workflows, minimizing machine downtime and optimizing resource allocation, contributing to significant energy savings.
How Machine Vision Improves Energy Efficiency
How Machine Vision Improves Energy Efficiency
1) Optimized Production Line Operations
1) Optimized Production Line Operations
Machine vision enables manufacturers to streamline their production line operations by automating inspection and quality control. This reduces the need for frequent machine adjustments and operator interventions, which consume valuable energy.
For example, in technical textile production, where machines run at high speeds, identifying defects in real-time allows manufacturers to address issues immediately without stopping production. This helps maintain a steady production flow, reduces energy wastage caused by unnecessary stoppages, and ensures that the equipment always operates optimally.
Machine vision also helps maintain the precision of textile production processes, which often require high-speed, high-volume operations. Providing accurate, real-time data on fabric quality enables manufacturers to make adjustments that optimize machine settings, reducing energy consumption while maintaining the desired output.
2) Minimizing Waste and Reducing Energy Waste
2) Minimizing Waste and Reducing Energy Waste
Waste reduction is a key benefit of machine vision in textile production. When defects go undetected in manual inspections, fabric that is below standard has to be scrapped, resulting in energy-intensive reprocessing or disposal. Additionally, defective products that make it further down the production line often require additional energy to correct, leading to inefficient resource use.
Machine vision helps mitigate this problem by detecting defects early in manufacturing, often at the weaving or extrusion stage. This means only high-quality fabrics are passed on to the following stages of production, reducing the need for corrective actions that consume additional energy.
The KWIS system, for example, can identify even the most minor defects, such as holes, misweaves, or color inconsistencies, which would be difficult for the human eye to detect. By flagging these issues early, KWIS ensures manufacturers avoid wasting energy on defective materials. This increases overall production efficiency and reduces the energy costs associated with remanufacturing or disposal.
3) Predictive Maintenance and Downtime Reduction
3) Predictive Maintenance and Downtime Reduction
Machine vision systems play a crucial role in predictive maintenance, helping manufacturers reduce downtime and the energy costs associated with unplanned machine failures. Predictive maintenance relies on real-time monitoring of machine performance, and by analyzing data from machine vision systems, manufacturers can predict when a piece of equipment is likely to fail or require servicing.
For instance, in the manufacturing of technical textiles like recorded or conveyor belt fabrics, minor defects or issues in the machinery can lead to breakdowns that halt production. Machine vision systems can detect even minor performance issues—such as uneven fabric tension or misalignment—before they cause a complete system failure, preventing the energy waste associated with system restarts or repairs.
Furthermore, machine vision systems can help schedule maintenance more efficiently by identifying patterns in machine performance. This ensures that maintenance is only performed when necessary, helping maintain machine efficiency and reducing the likelihood of excessive energy consumption during periods of inefficiency or malfunction.
4) Improved Resource Allocation
4) Improved Resource Allocation
Machine vision systems are valuable for improving energy efficiency and helping optimize resource allocation. They can detect inefficiencies in material usage, labor allocation, and machine performance by continuously monitoring production lines.
For example, in the production of shade nets or FIBC bags, machine vision can analyze fabric quality in real-time and determine if adjustments to the production line are needed. If a batch of fabric is found to be defective, the system can automatically redirect production to ensure that only materials that meet quality standards continue down the line. This reduces the energy used to process low-quality materials and ensures that resources are directed toward the most efficient production process.
Machine vision systems can help manufacturers reduce waste, energy consumption, and costs by improving resource allocation while maintaining the highest quality standards.
Overcoming Challenges in Machine Vision Integration
Overcoming Challenges in Machine Vision Integration
While machine vision presents numerous opportunities to improve energy efficiency, manufacturers must address several challenges when integrating this technology into their production lines.
1) High Initial Investment
1) High Initial Investment
The upfront costs of implementing machine vision technology can be a significant challenge, especially for manufacturers with limited budgets. Machine vision systems require specialized cameras, sensors, and processing software, which can be costly. Additionally, integrating machine vision into existing production lines may require upgrading equipment and training personnel to handle the new technology.
While the initial investment can be high, the long-term benefits of machine vision systems—such as reduced energy consumption, lower operational costs, and increased productivity—more than justify the expenditure. Manufacturers can mitigate the cost barrier by adopting a phased implementation approach, gradually upgrading their systems to integrate machine vision without needing a significant, one-time investment.
2) Integration with Legacy Systems
2) Integration with Legacy Systems
Integrating machine vision technology with legacy equipment can be challenging. Many older machines are not designed to work with modern automation systems, and retrofitting them to accommodate machine vision can require significant modifications. The challenge is to ensure seamless compatibility between machine vision systems and existing machinery, which may require considerable planning and technical expertise.
Fortunately, machine vision technology has advanced so that many systems are designed to be easily integrated with legacy production lines. For example, Robro Systems’ KWIS can be implemented without extensive modifications to existing equipment, ensuring minimal disruption to ongoing production.
3) Data Complexity and Analysis
3) Data Complexity and Analysis
Machine vision systems generate large amounts of data that must be processed, analyzed, and interpreted in real-time. This data can be overwhelming for manufacturers who lack the infrastructure or expertise to manage it effectively. The complexity of the data may lead to difficulties deriving actionable insights, which could hinder the efficiency gains machine vision is designed to provide.
AI and machine learning advancements have helped address this issue by automating data analysis. Modern machine vision systems have sophisticated algorithms that can quickly and accurately process data and provide actionable insights, reducing manufacturers' burden of manually interpreting the data.
4) Training and Skill Gaps
4) Training and Skill Gaps
Implementing machine vision systems requires specialized knowledge, and manufacturers can face challenges due to a lack of skilled personnel. Operators need to be trained to understand how the system works, interpret the data it produces, and address any issues that arise during operation. Without proper training, the potential of machine vision technology may not be fully realized, and the system may not operate at its peak efficiency.
Fortunately, many machine vision vendors offer comprehensive training programs to ensure operators are fully equipped to use the system effectively. As machine vision technology continues to evolve, manufacturers must invest in ongoing training to keep up with new developments and maintain the highest levels of operational efficiency.
Benefits of Leveraging Machine Vision for Energy Efficiency
Benefits of Leveraging Machine Vision for Energy Efficiency
1) Significant Energy Savings- Machine vision systems contribute to energy savings by automating processes, minimizing downtime, reducing waste, and optimizing resource allocation. Manufacturers can reduce their overall energy consumption by addressing inefficiencies early in production and maintaining optimal machine performance, leading to long-term savings.
2) Lower Operational Costs- Automating key processes such as quality control, defect detection, and predictive maintenance helps reduce labor costs and the need for rework, which can be energy-intensive. Machine vision systems enable manufacturers to run their production lines with minimal human intervention, lowering operational costs and improving energy efficiency.
3) Sustainability and Regulatory Compliance- As sustainability becomes increasingly important for industries worldwide, machine vision helps manufacturers meet their environmental and regulatory goals. By reducing energy consumption, material waste, and carbon emissions, machine vision contributes to more sustainable production practices, helping manufacturers stay ahead of regulatory requirements and improve their environmental footprint.
4) Increased Productivity and Throughput- Machine vision systems enhance production efficiency by reducing downtime, increasing throughput, and ensuring consistent quality. By automating key tasks such as defect detection and quality control, manufacturers can achieve higher productivity levels while consuming less energy.
Technical Innovations Driving Energy Efficiency
Technical Innovations Driving Energy Efficiency
Machine vision technology continues to evolve, with innovations driving energy efficiency in technical textile production. Some key advancements include:
1) AI-Driven Defect Detection- AI-powered algorithms are improving the accuracy of defect detection in fabrics. These systems can identify even the smallest flaws, ensuring manufacturers only use the highest-quality materials and minimizing waste. AI also enables predictive maintenance, helping manufacturers avoid energy-consuming system failures.
2) Hyperspectral Imaging- Hyperspectral imaging technology allows manufacturers to analyze the composition of fabrics at a molecular level, helping them identify defects or inconsistencies that might not be visible to traditional machine vision systems. This technology reduces waste by ensuring that only the best materials continue down the production line.
3) Edge Computing- Edge computing allows machine vision systems to process data locally, reducing the need for cloud-based processing and minimizing the energy consumption associated with data transfer. This technology enables real-time analysis, allowing manufacturers to adjust production processes immediately and optimize energy use.
Real-World Applications in Technical Textiles
Real-World Applications in Technical Textiles
1) FIBC Inspection- Flexible Intermediate Bulk Containers (FIBC) are widely used in agriculture, construction, and chemicals. Machine vision inspects the fabric for defects such as holes, weak seams, or uneven weaving. KWIS, for instance, enables real-time defect detection, ensuring that only high-quality fabric is processed reducing waste and energy consumption.
2) Conveyor Belt Fabrics- Conveyor belt fabrics are crucial in mining, logistics, and manufacturing. Machine vision systems inspect the fabric for flaws that affect the belt’s strength and durability. By catching defects early, these systems ensure that only the best materials are processed, reducing the need for energy-intensive repairs and replacements.
3) Shade Nets- Shade nets protect crops from excessive sunlight. Machine vision systems inspect the netting for uneven weave or color discrepancies. Identifying these issues early helps reduce waste and energy consumption during production and ensures that only the highest-quality nets are produced.
Conclusion
Conclusion
Machine vision is revolutionizing the way technical textile manufacturers approach energy efficiency. By automating inspections, detecting defects early, reducing waste, and optimizing resource allocation, machine vision systems help manufacturers lower energy consumption, reduce costs, and improve product quality. With applications in industries ranging from FIBC and conveyor belts to shade nets and tire cord fabrics, machine vision drives significant changes in the technical textile sector.
At Robro Systems, we understand the challenges faced by technical textile manufacturers and offer cutting-edge solutions like the Kiara Web Inspection System (KWIS) to help optimize production processes, reduce energy consumption, and ensure superior fabric quality. Our AI-driven solutions are designed to integrate seamlessly into your production line, providing real-time defect detection and operational insights to improve energy efficiency.