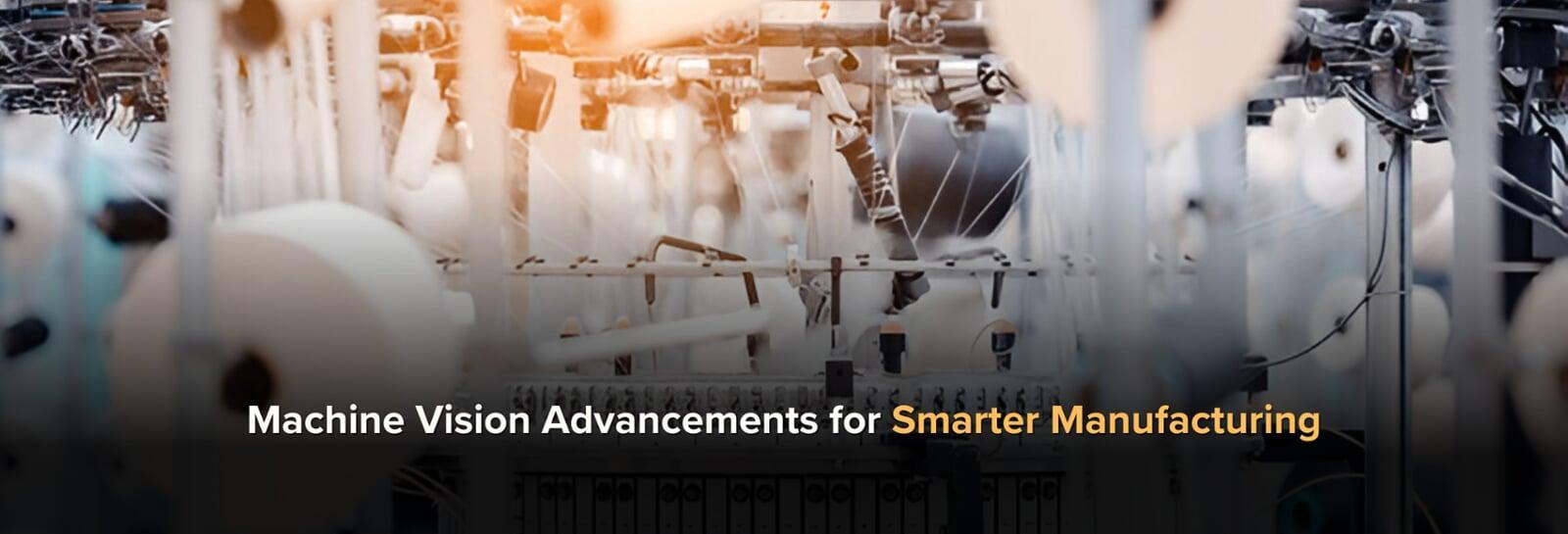
The manufacturing industry is undergoing a rapid transformation driven by technological advancements that improve efficiency, quality, and automation. Among these innovations, machine vision has emerged as a game-changer, revolutionizing production processes across various sectors. From inspecting high-precision technical textiles to optimizing defect detection in conveyor belt fabrics, machine vision ensures superior quality control and operational efficiency. With artificial intelligence (AI), deep learning, and edge computing powering modern inspection systems, machine vision sets new standards for accuracy and productivity.
What is Machine Vision?
How Machine Vision Works
Machine vision systems function through several key components:
High-Resolution Cameras: Capture detailed manufacturing process images at high speeds, ensuring no defect goes unnoticed.
Lighting Systems: Proper illumination is critical for highlighting surface defects and ensuring accurate image capture.
AI and Deep Learning Algorithms: Analyze images, detect defects, and classify fabric irregularities with self-learning capabilities that improve over time.
Real-Time Processing Units: These units instantly process vast amounts of visual data, allowing immediate corrective action.
Automated Alerts and Reports: Machine vision systems log defect data, generate reports, and notify operators, enabling quick responses to quality issues.
Integration with Manufacturing Execution Systems (MES): Machine vision can be linked with ERP and MES software to provide a holistic view of production quality.
By leveraging these technologies, manufacturers can detect and rectify defects early, enhancing product quality while minimizing waste and downtime.