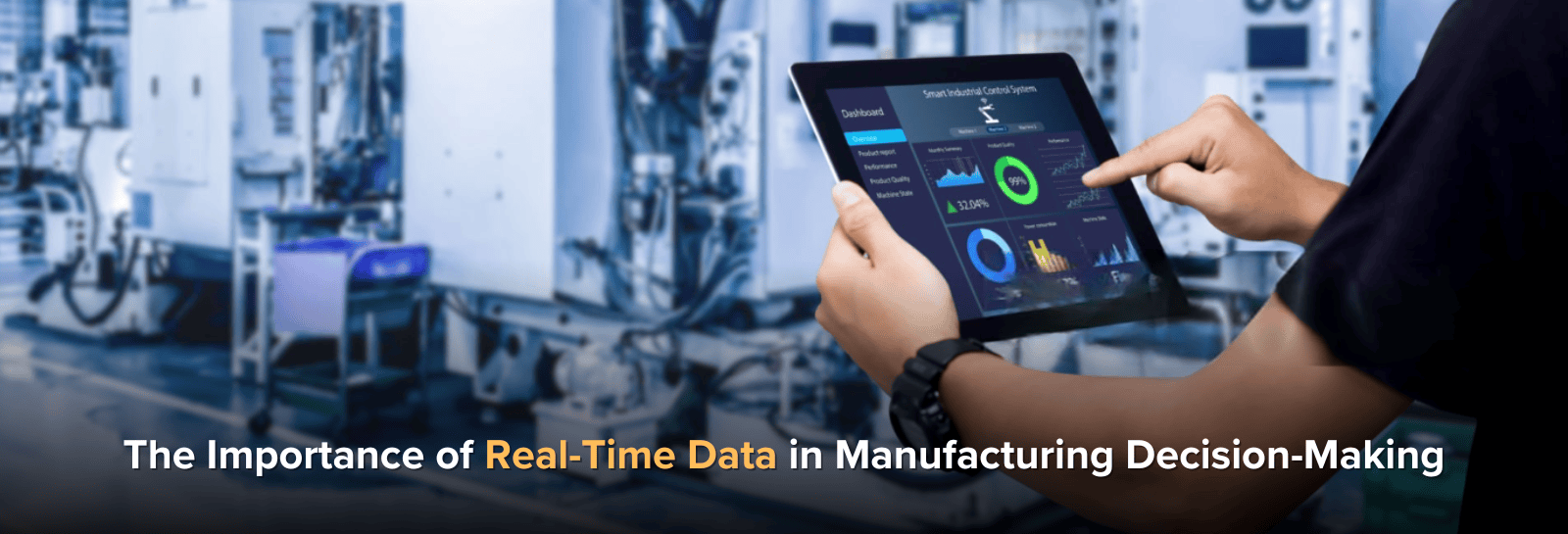
Manufacturing is evolving at an unprecedented pace, with increasing demand for higher efficiency, lower costs, and better quality control. Manufacturers need real-time data to make informed decisions as global supply chains become more complex and production lines more automated. Traditional decision-making in manufacturing was often reactive, relying on historical reports and manual inspections. However, in today's fast-moving industrial environment, waiting for periodic reports can lead to inefficiencies, defects, and costly downtimes.
Real-time data gives manufacturers instant insights into production processes, enabling proactive problem-solving, predictive maintenance, and optimized resource allocation. Technologies such as the Industrial Internet of Things (IIoT), AI-driven analytics, and cloud computing are transforming factories into innovative manufacturing ecosystems where decisions are made based on live data instead of outdated reports.
This blog explores the role of real-time data in manufacturing, its benefits, key applications, and how businesses can leverage it to enhance productivity and competitiveness.
Understanding Real-Time Data in Manufacturing
What is Real-Time Data?
Real-time data is instantaneous data collected from sensors, machines, and systems across the manufacturing floor. Unlike traditional data analyzed after production, real-time data enables immediate insights and instant decision-making.
For example, a machine monitoring system that detects abnormal vibrations can instantly alert maintenance teams, preventing unexpected breakdowns. Similarly, real-time defect detection can prevent defective products from moving further down the production line.
How is Real-Time Data Collected?
Manufacturers gather real-time data through various sources, including:
✔ IoT Sensors – Measure temperature, pressure, humidity, machine speed, and other parameters.
✔ AI-Powered Machine Vision – Detects defects and quality deviations.
✔ SCADA (Supervisory Control and Data Acquisition) Systems – Monitors and controls industrial processes.
✔ Enterprise Resource Planning (ERP) Systems – Tracks production schedules, inventory, and supply chain data.
✔ Cloud and Edge Computing – Processes data instantly for real-time analytics.
By integrating these technologies, manufacturers create a real-time feedback loop that continuously monitors, analyzes and optimizes production performance.
Why Real-Time Data Matters in Manufacturing Decision-Making
1) Faster Problem Detection and Resolution
Traditional manufacturing relied on periodic reports and manual inspections, meaning defects or inefficiencies were often detected after production. This led to:
Increased material waste from defective products.
High rework costs due to late defect detection.
Production delays affecting order fulfillment.
With real-time monitoring, manufacturers can detect and resolve problems as they occur. For example, suppose an AI-powered quality inspection system identifies a pattern of fabric defects in a textile factory. In that case, it can immediately alert operators, allowing them to adjust machine settings before producing more defective material.
2) Improved Production Efficiency and Throughput
Manufacturing lines operate at high speeds, making efficiency critical. Real-time data helps optimize production by:
✔ Identifying bottlenecks in production flow.
✔ Optimizing machine uptime and minimizing idle times.
✔ Adjusting workflows dynamically based on demand.
For example, real-time production dashboards allow factory managers to monitor machine utilization rates, detect underperforming equipment, and make data-driven adjustments. A 1% improvement in manufacturing efficiency through real-time data can result in millions of dollars in annual savings for large-scale factories.
3) Predictive Maintenance to Reduce Downtime
Equipment failure is one of the biggest challenges in manufacturing, leading to:
Unplanned downtime that disrupts production.
High repair costs due to emergency fixes.
Loss of revenue from delayed deliveries.
Real-time data from IoT-enabled sensors enables predictive maintenance, where machines predict their failures before they happen. Instead of waiting for a breakdown, manufacturers can perform scheduled maintenance only when necessary, reducing unnecessary servicing costs.
Example: A global steel manufacturer used predictive maintenance to reduce machine downtime by 40%, saving over $2 million yearly in repair costs.
4) Real-Time Quality Control for Zero-Defect Manufacturing
Quality control is crucial in pharmaceuticals, aerospace, textiles, and electronics industries, where even minor defects can lead to product recalls or safety hazards. Traditional quality checks often involve sampling and post-production testing, which can miss hidden defects.
AI-powered real-time defect detection ensures 100% quality inspection by:
✔ Identifying defects instantly through machine vision.
✔ Classifying defects based on severity.
✔ Automatically adjusting machine parameters to prevent further defects.
For example, real-time defect detection systems in textile manufacturing can identify weaving defects, color variations, or fabric inconsistencies at millisecond speeds, ensuring only flawless fabrics reach customers.
5) Data-Driven Inventory and Supply Chain Optimization
Inventory mismanagement leads to:
Excess stock increases storage costs.
Material shortages caused production delays.
Wasted raw materials due to overordering.
Real-time inventory tracking through IoT and ERP systems ensures optimal stock levels, preventing overstocking and shortages. When integrated with supply chain analytics, real-time data can:
✔ Predict raw material demand based on production trends.
✔ Automatically reorder supplies just-in-time (JIT).
✔ Identify supplier delays and adjust schedules accordingly.
Example: A leading consumer electronics company reduced inventory holding costs by 25% by switching to real-time supply chain monitoring, ensuring components arrived only when needed.
6) Enhanced Worker Safety and Compliance
Manufacturing environments involve hazardous conditions, such as high temperatures, toxic chemicals, and heavy machinery. Real-time data plays a vital role in ensuring worker safety by:
✔ Monitoring environmental conditions (e.g., air quality, temperature).
✔ Detecting safety violations using AI-powered cameras.
✔ Alerting workers and supervisors about potential hazards.
For example, wearable IoT devices can track worker vitals (heart rate, fatigue levels) and send alerts if a worker is at risk of exhaustion or exposure to hazardous conditions.
Technologies Powering Real-Time Data in Manufacturing
Conclusion
Real-time data revolutionizes manufacturing, enabling faster decision-making, reduced downtime, improved quality control, and optimized production efficiency. By leveraging technologies like IoT, AI, and cloud computing, manufacturers gain instant visibility into operations, allowing them to predict problems before they occur and optimize every aspect of production.
As manufacturing becomes increasingly data-driven, companies that embrace real-time analytics will gain a competitive advantage, ensuring higher efficiency, reduced costs, and superior product quality in the Industry 4.0 era.