Why Automate Defect Identification
Why Automate Defect Identification
Identification of Defects by Visions and Use Cases
High-resolution cameras take pictures of parts in motion on a production line. AI algorithms identify these defects in real time and take appropriate action
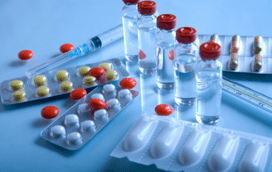
Pharmaceutical
Sort broken tablets, avoid empty blister packaging, ensure accurate counting in every pack, prevent label printing defects
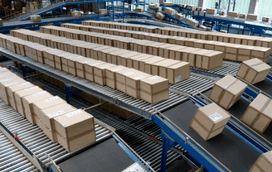
Printing and Packaging
Detect missing information on the outer packaging, printing defect identification like incorrect colour, label, or print, improper or missing batch code
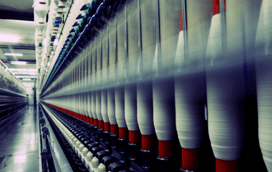
Textile
Line scan cameras are used to inspect sheets, webs, and cylindrical objects by capturing high-resolution fast-moving images; these can be useful for weaving defects and other textile inspections
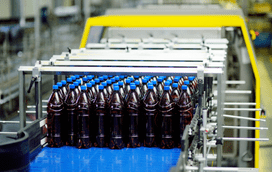
Food and Beverage
Identify broken or missing pieces, improper packaging and sealing, label printing defects, inaccurate or missing barcode, mislabelled outer packaging
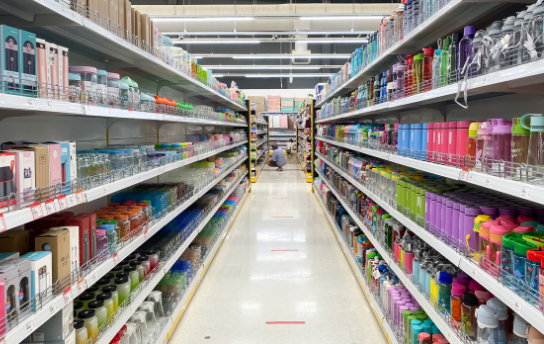
FMCG
Package seal inspection, date and lot code inspection, label quality inspection, barcode quality inspection, package seal and tamper-proof seal inspection
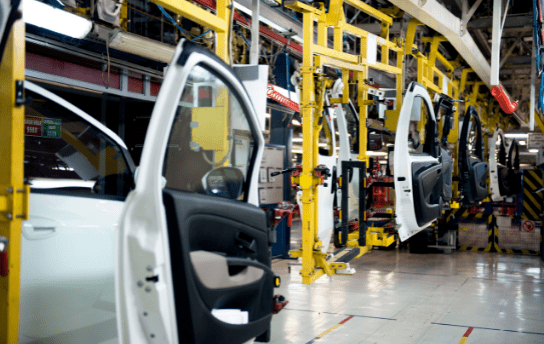
Metal and Automotive
Tire and wheel systems, power train systems, safety systems, electronic systems, small metal parts counting and inspection
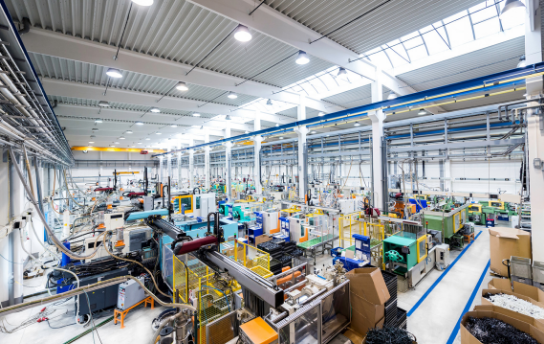
Wood and Plastic
Cap defects sorting, matchstick inspections, hole choke identification, over-sized knots, codes and markings, gouges and gaps, chips, lamination issues, stains, tear-outs and rips, voids, surface patterns and colors, profile shapes and dimensions
Benefits of Automated Defect Identification
Video-Based Case Study
Wooden sticks have replaced plastic sticks for teeth cleaning. Defects like missing holes, improper prints, cracks, and chip offs may occur during the manufacturing process. Manual inspection is inaccurate and slow and missed errors can result in rejections and losses. Robro Systems developed a vision system using line scan cameras and deep learning algorithms for automating the process, which is three times more reliable and five times quicker and delivers up to 99.5% accuracy ensuring each shipment is defect-free thereby enhancing customer satisfaction.
Have any questions?
Contact us to get your queries resolved
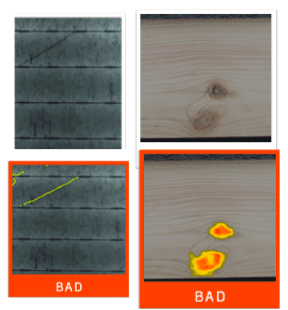
Identify defects by Vision
High-resolution cameras take pictures of parts in motion on a production line. AI algorithms identify these defects in real time and take appropriate action
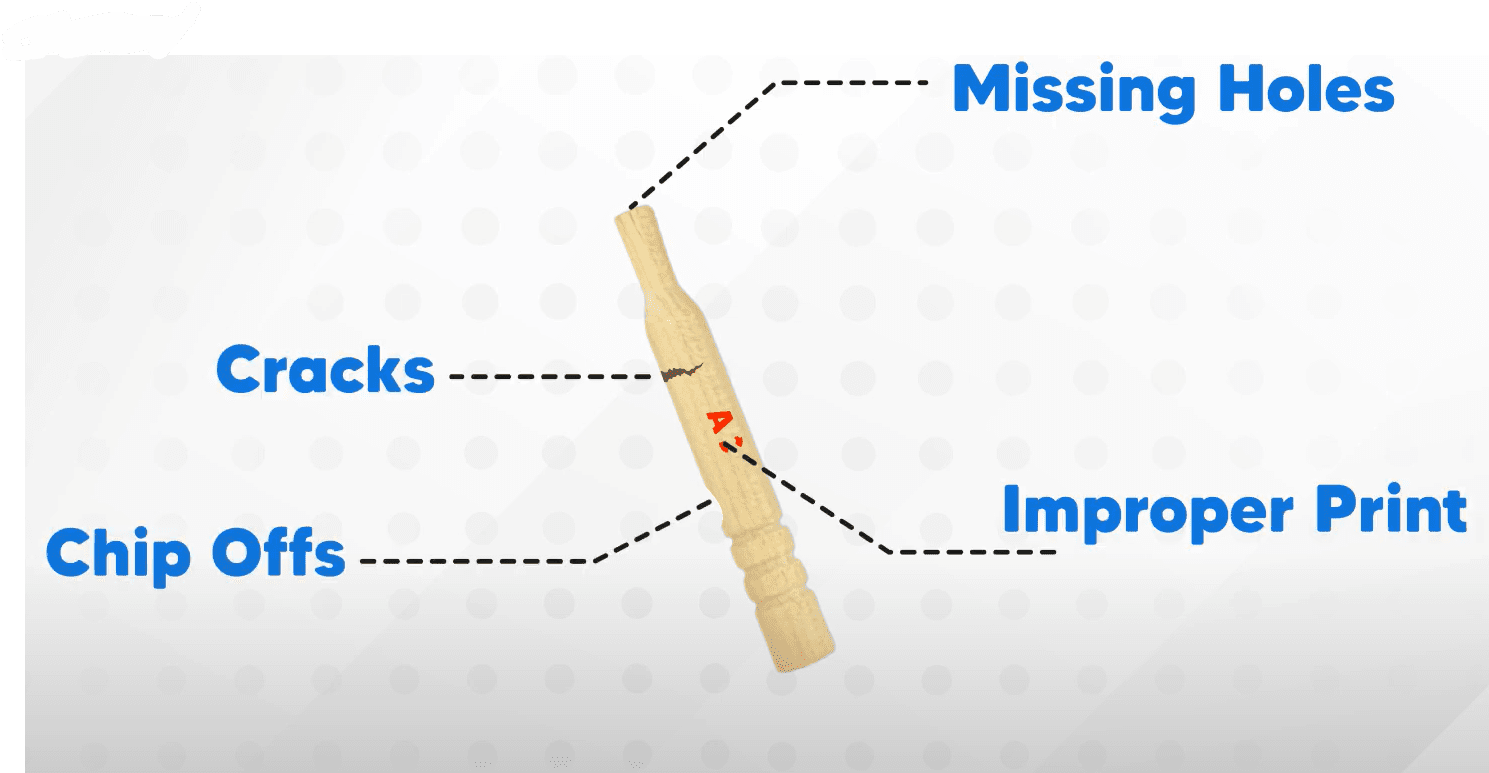
Automated Defect Identification can save you over
₹ 10,00,000 every year!
An estimated 23mn products were recalled in 2021. The cost of error is surmounting every day. Thanks to affordable inspection solutions these are avoidable. Vision Systems powered by our AI algorithms are trained to identify what is OK and what is Not-OK and take relevant action at high speeds while identifying the smallest of defects.
Automatically perform sorting based on types of defects identified by vision systems.
Automated defect identification through vision can identify defects that evade the human eye!
Digitalized defect data and insights into production data inch your factory closed to Industry 4.0.
When defects are identified early, re-work and wastage of products can be minimized.
Inspect at high speeds leading to efficient processing and increase in production rate.
Move on from human errors and attrisessions with AI assisted inspection to augment labor force.
Selected Case Study
For a wooden brush sticks manufacturer, automated defect identification helped reduce cost of labor, increase speed of inspection and helped our client's customer build tremendous faith in our client's ability to delivery quality product.