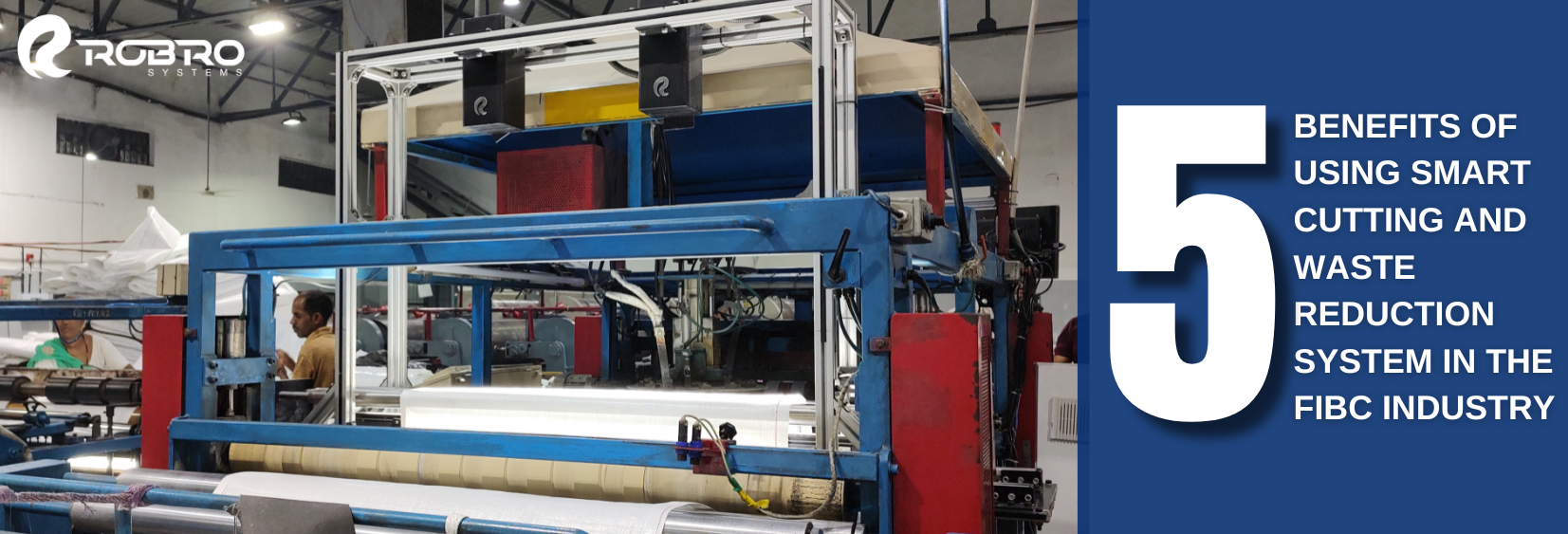
India’s Flexible Intermediate Bulk Container (FIBC) industry is considered to have the highest growth opportunities in the global FIBC market. This growth is driven by increased international trade and favorable initiatives by the Indian government to drive manufacturing in the nation. Industries in India that use FIBCs, like food products, agriculture, pharmaceuticals, chemicals, and fertilizers have seen considerable growth over this period, which has also driven the growth in FIBC sales. According to experts, the Indian FIBC industry is set to grow at a rate of 2x in the year 2022-23.
To capitalize on this growth in domestic sales and exports, stringent quality standards and optimal waste reduction are essential. During the cutting process in FIBC manufacturing, an error can result in entire cut sheets being discarded owing to a defective sheet. Typically, the FIBC industry has depended on skilled, experienced personnel keeping an eagle eye on materials and machines to ensure a defect-free process. As production ramps up, this becomes impractical, costly, and potentially hazardous, with so many people deployed on the production floor.
Hence, a machine vision-based, AI-enabled system like the Kiara Web Inspection System (KWIS) can detect these defects and perform cutting accurately, reducing wastage by as much as 50%.
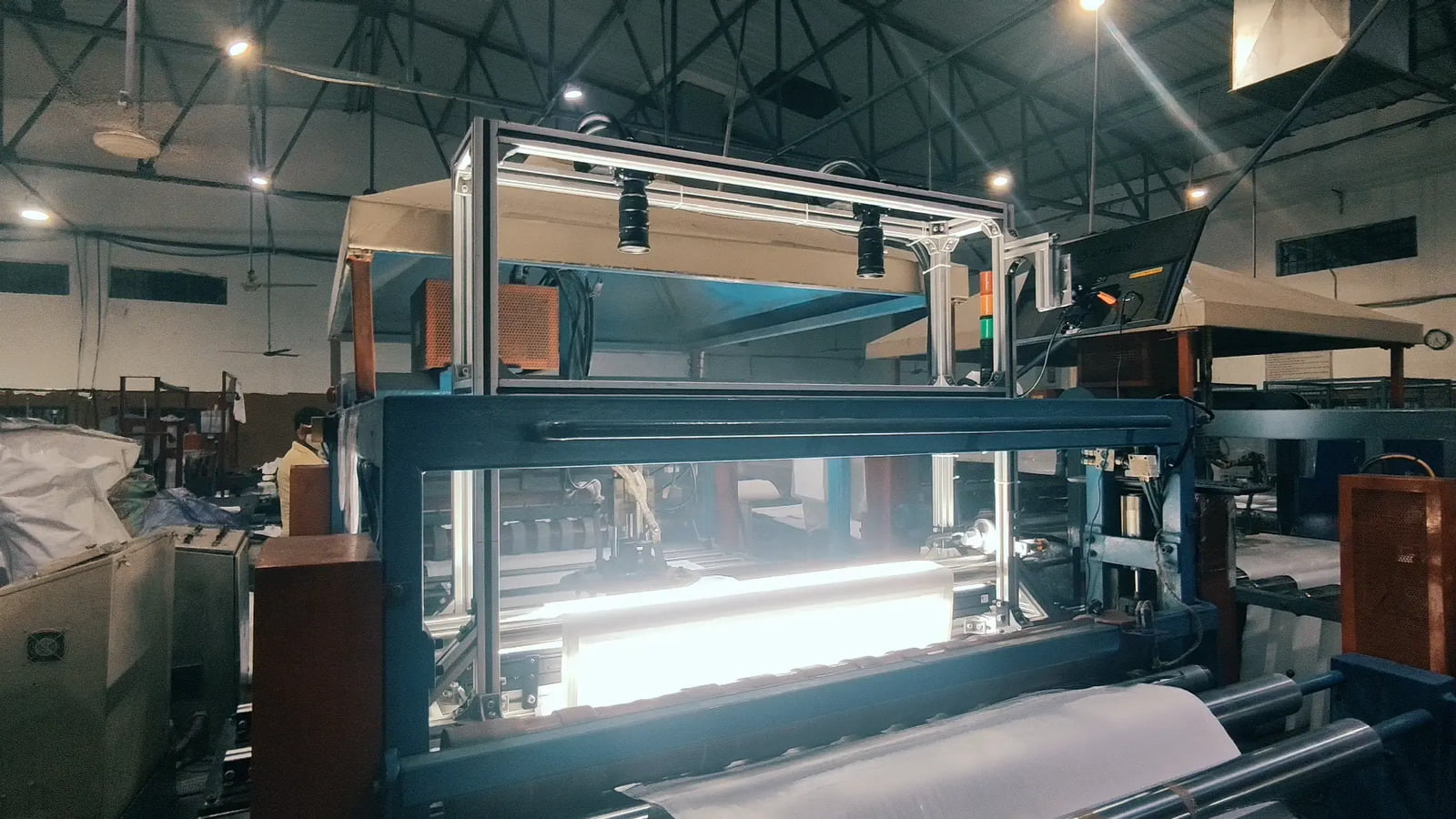
Installs onto your existing machinery
Machine learning for ongoing defect recognition and prevention
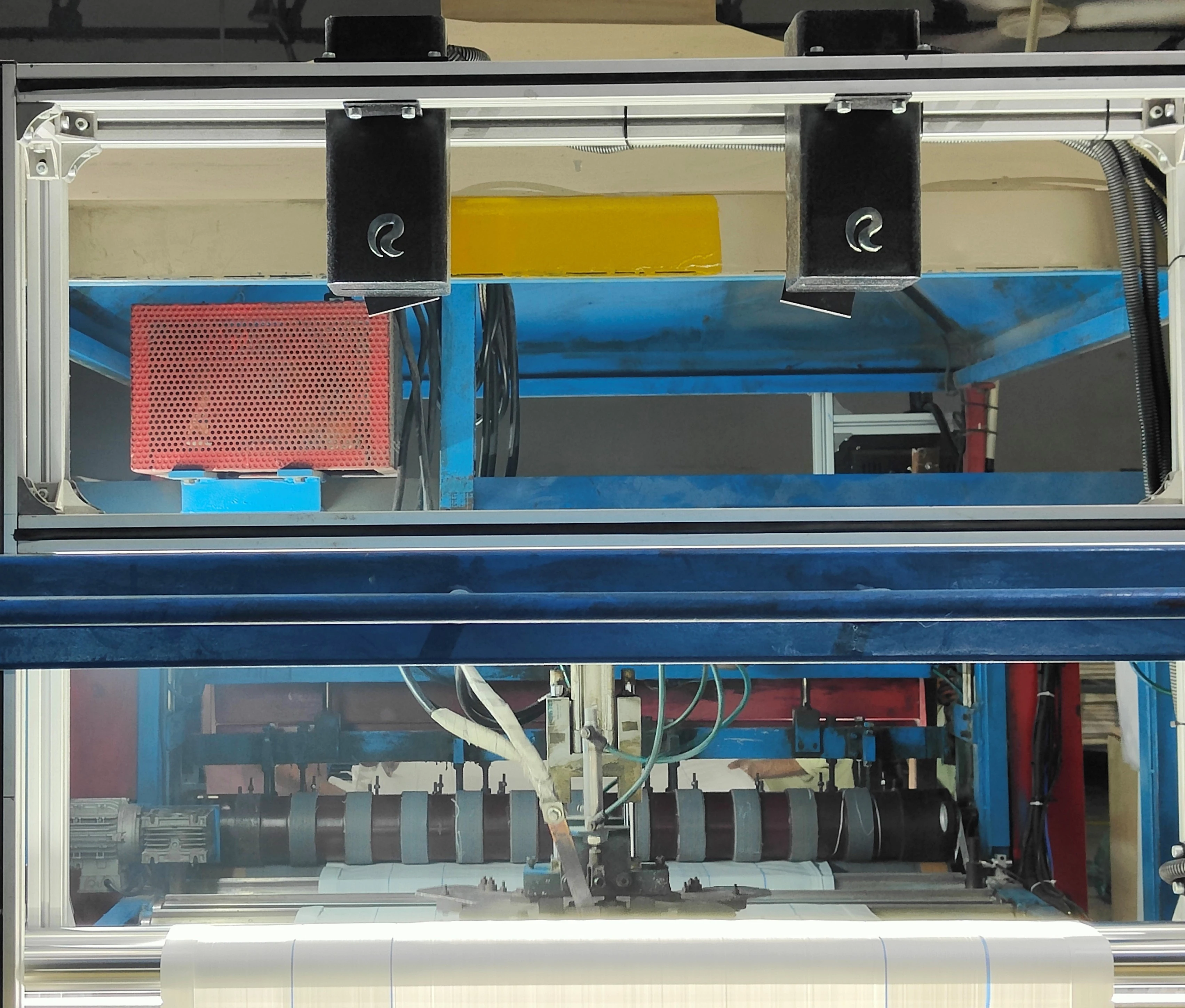
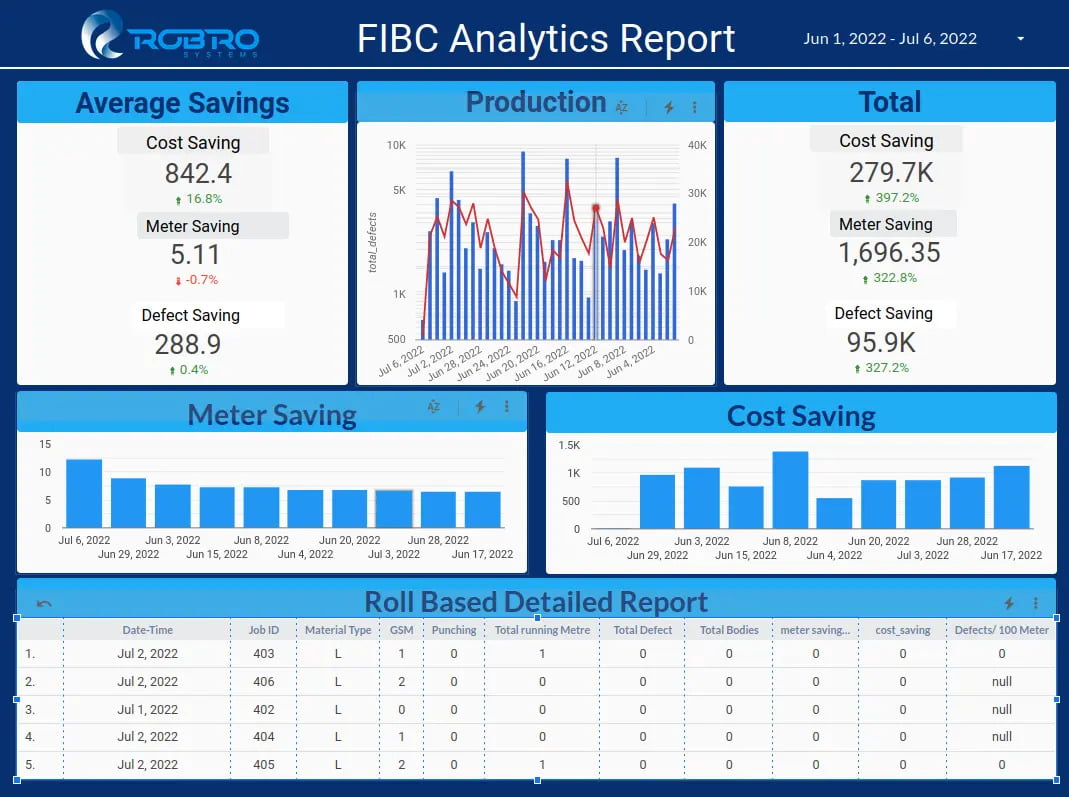
Rich, informative defect reports, available on multiple devices
Versatile enough to catch all defects
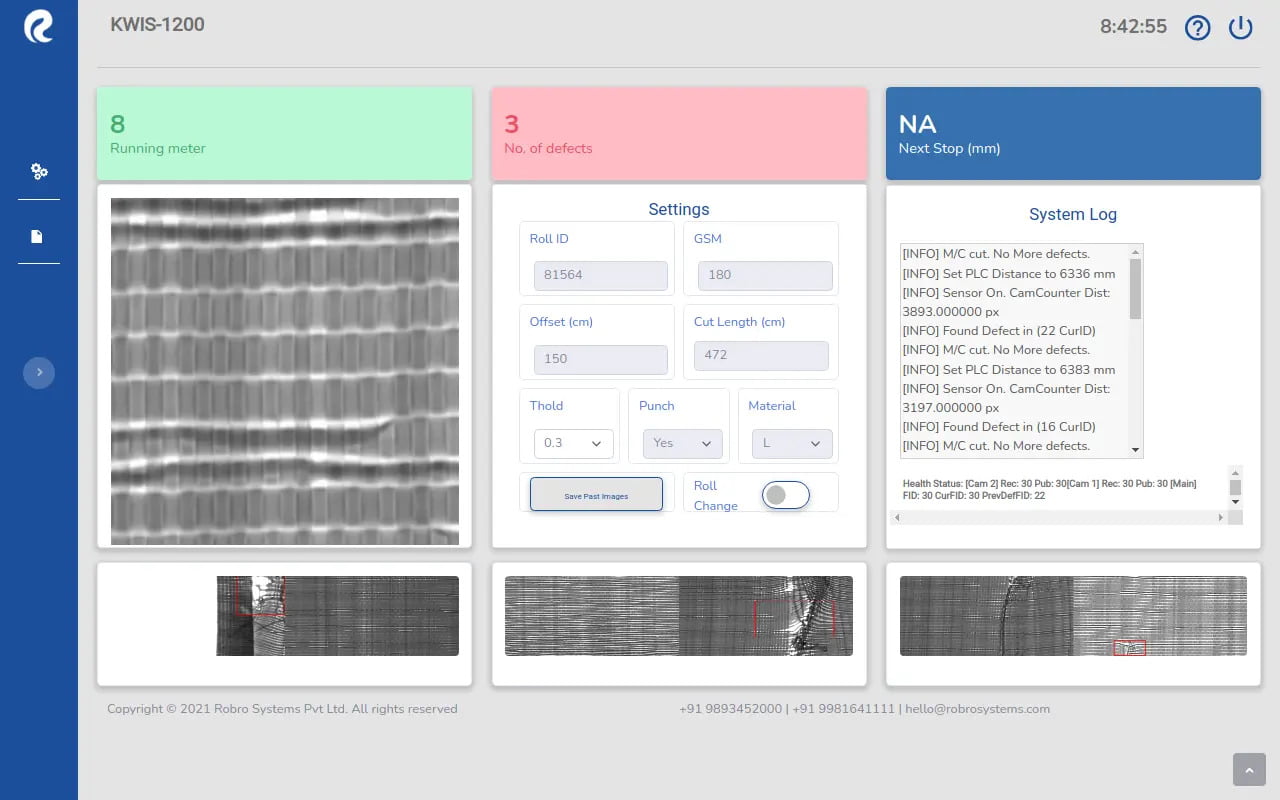
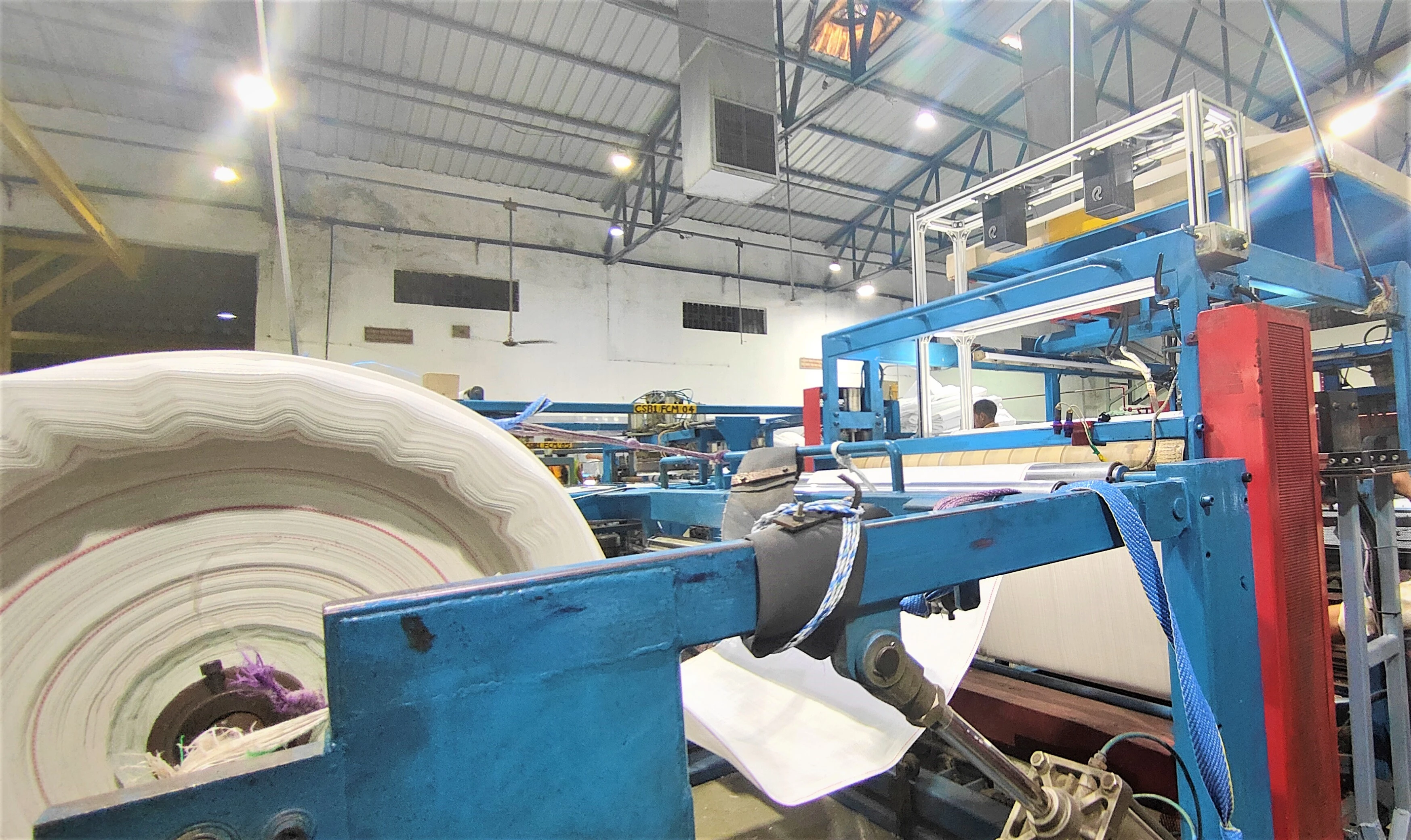