Reduce Your Wastage With Automated Inspection and Smart Cutting
About Kiara Web Inspection System for FIBC
About Kiara Web Inspection System for FIBC
What It Does
- Finds any defect in the fabric using high quality machine vision and artificial intelligence.
- For each defect, the system finds out the optimum cut point and minimizes the wastage of material.
- It automatically blocks the Spout cutter in case of defects.
- Inspects every inch of fabric using the highest quality cameras.
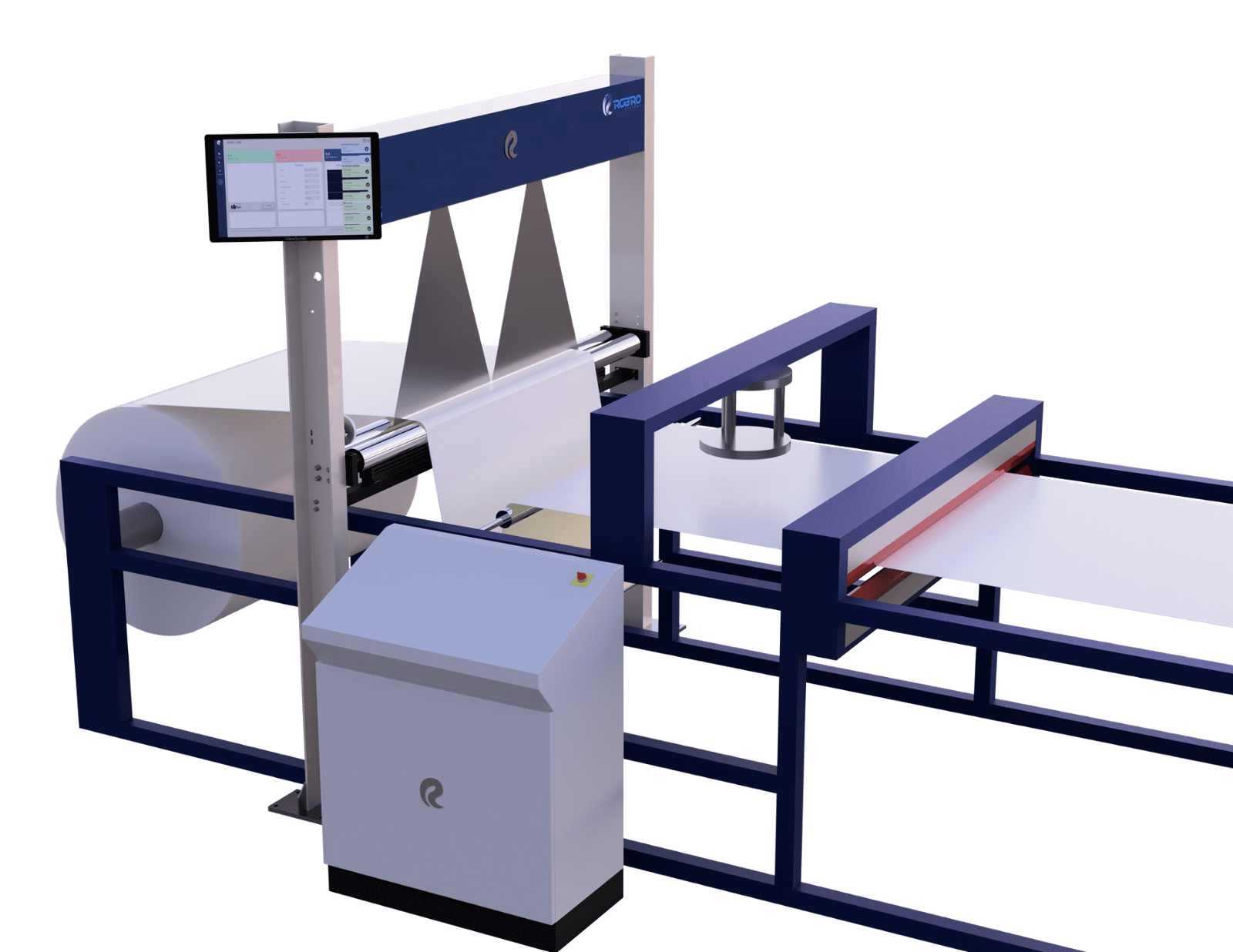
Features of KWIS
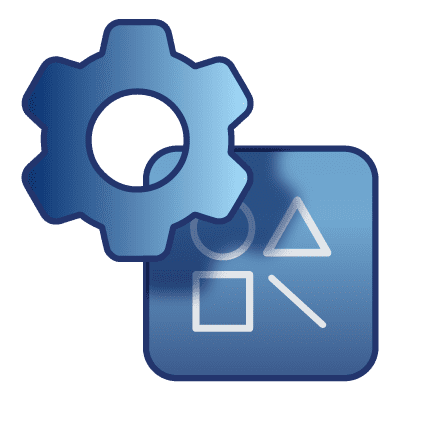
Cutter block function
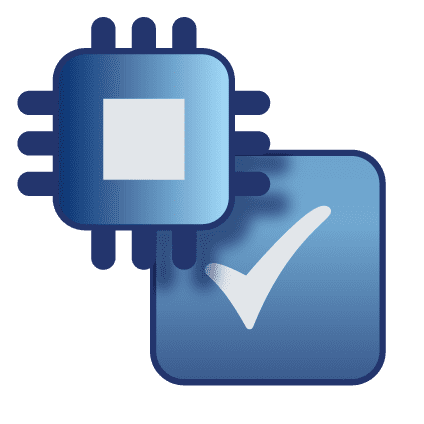
Precise and ultra fast AI machine vision
KWIS' AI Engine identifies all defects, as small as 2 mm, and at speeds up to 120 meters/minute.
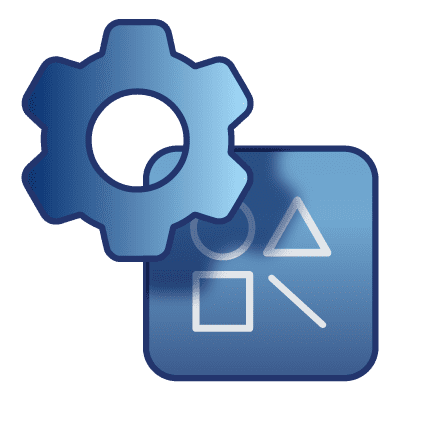
Easy to use touch (HMI)
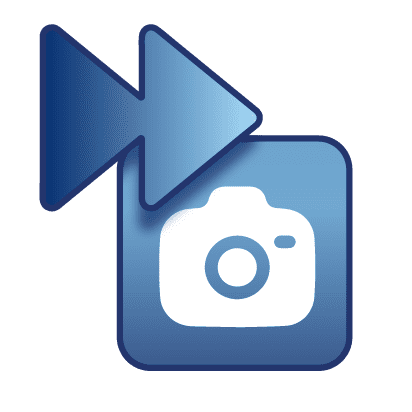
Detects all types of fabric defects accurately
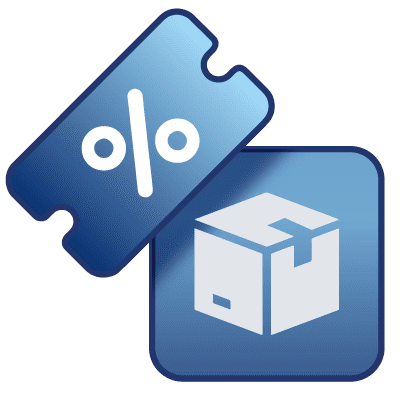
Self-learning AI system
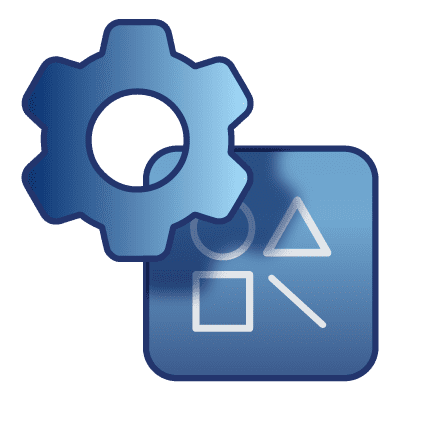
Circular fabric model
Customize Defect Detection
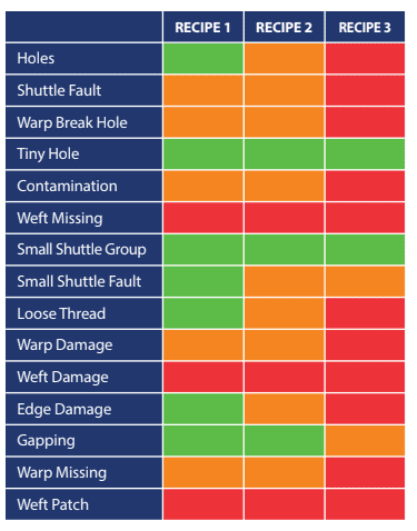
Benefits of KWIS for FIBC Industry
- By blocking the spout cutter and stopping at optimum cut point, KWIS reduces Wastage by 45-50% for Side, 65-70% on U-Panel, and 50% on each side for Tubular.
- Our system has an accuracy up to 99.95% and it increases further as its AI algorithm trains itself and quickly adapts to your production process and fabric types.
- KWIS eliminates slow and manual Inspection steps in the production process improving production speeds. This is more-so during 2-side inspection of tubular fabrics.
- KWIS removes the need for manual inspection labor, saving you time, money, and providing a more efficient alternative.
- No need for callbacks, reworks, or rejections as our system assures the quality of your products.
Defects Categories
Defects Categories
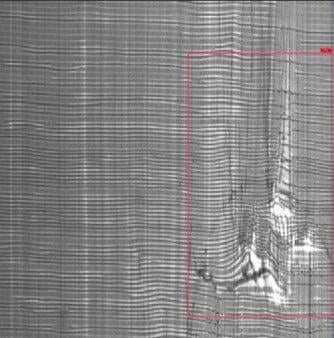
Holes
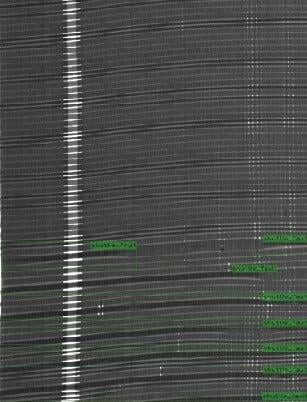
Shuttle Fault
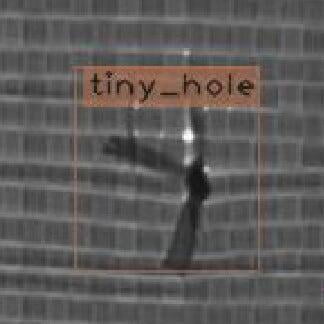
Tiny Hole
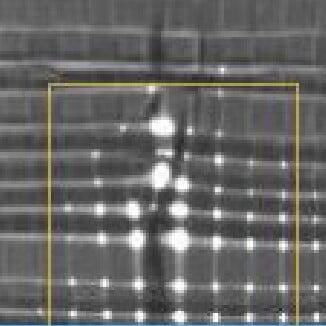
Warp Break Hole
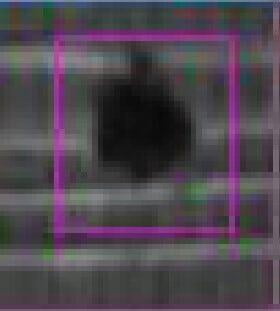
Contamination
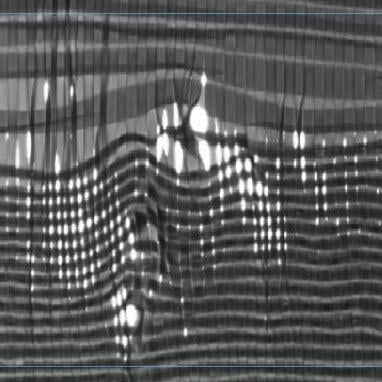
Weft Missing
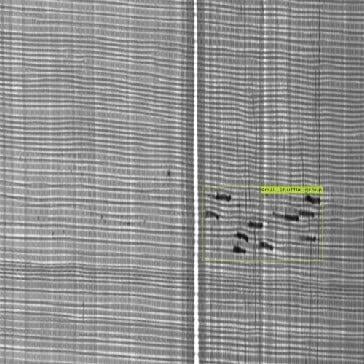
Small Shuttle Group
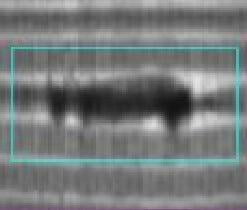
Small Shuttle Fault
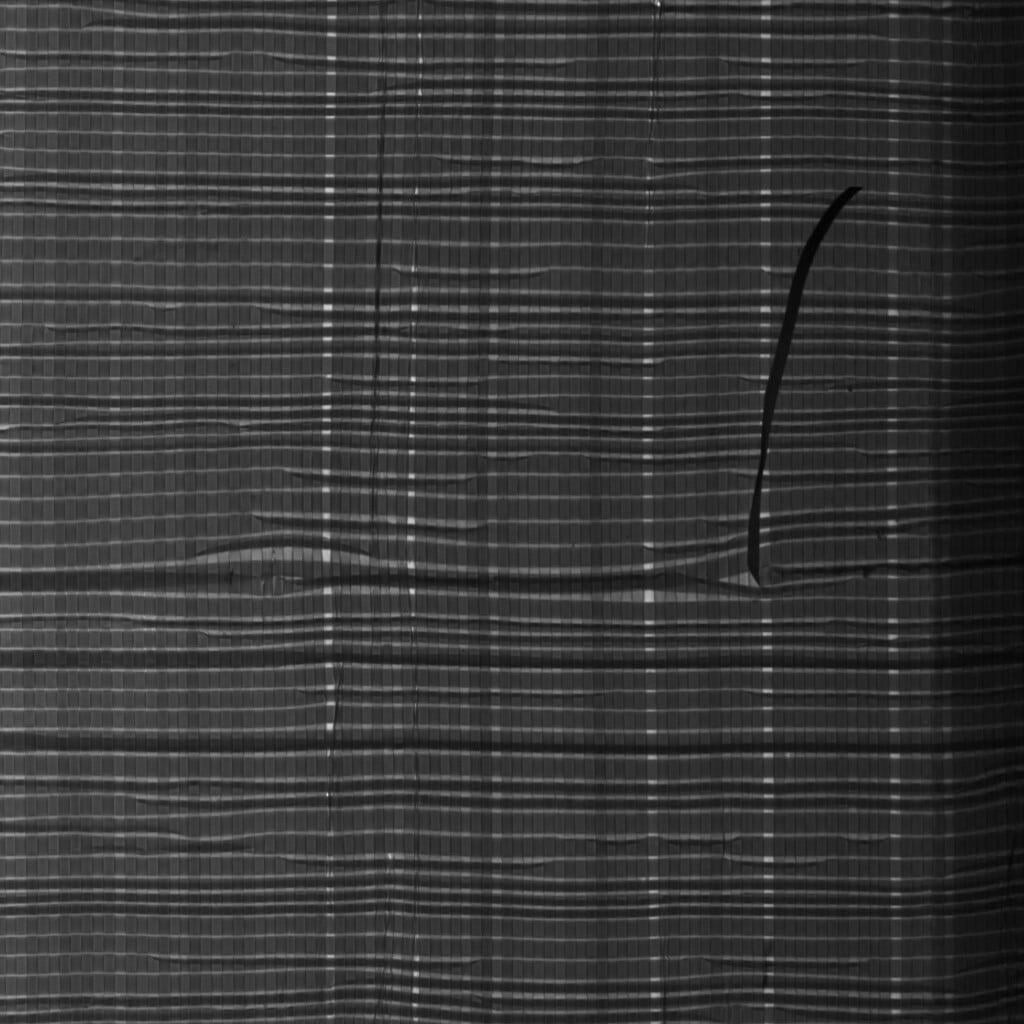
Loose Thread
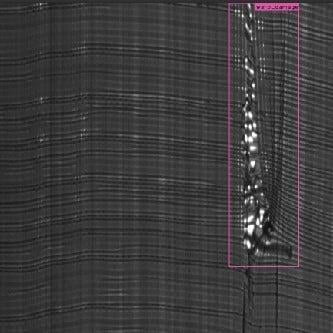
Warp Damage
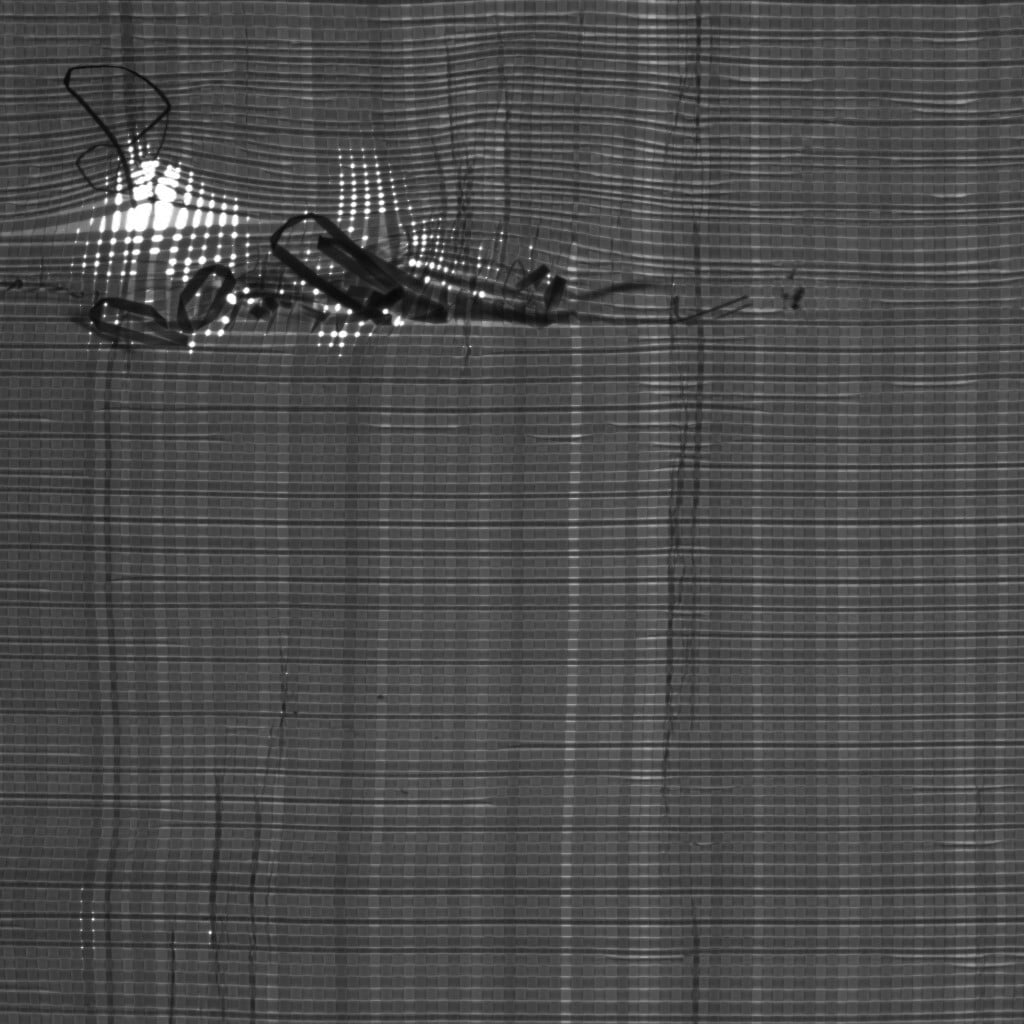
Weft Damage
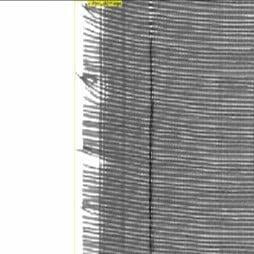
Edge Damage
KWIS - Resources
GUI and Reports & Analytics
The KWIS generates an advanced analytics report on the type of defects, quality trends, operator performance report and other important analytics that helps business owners track the production process and assure quality control.
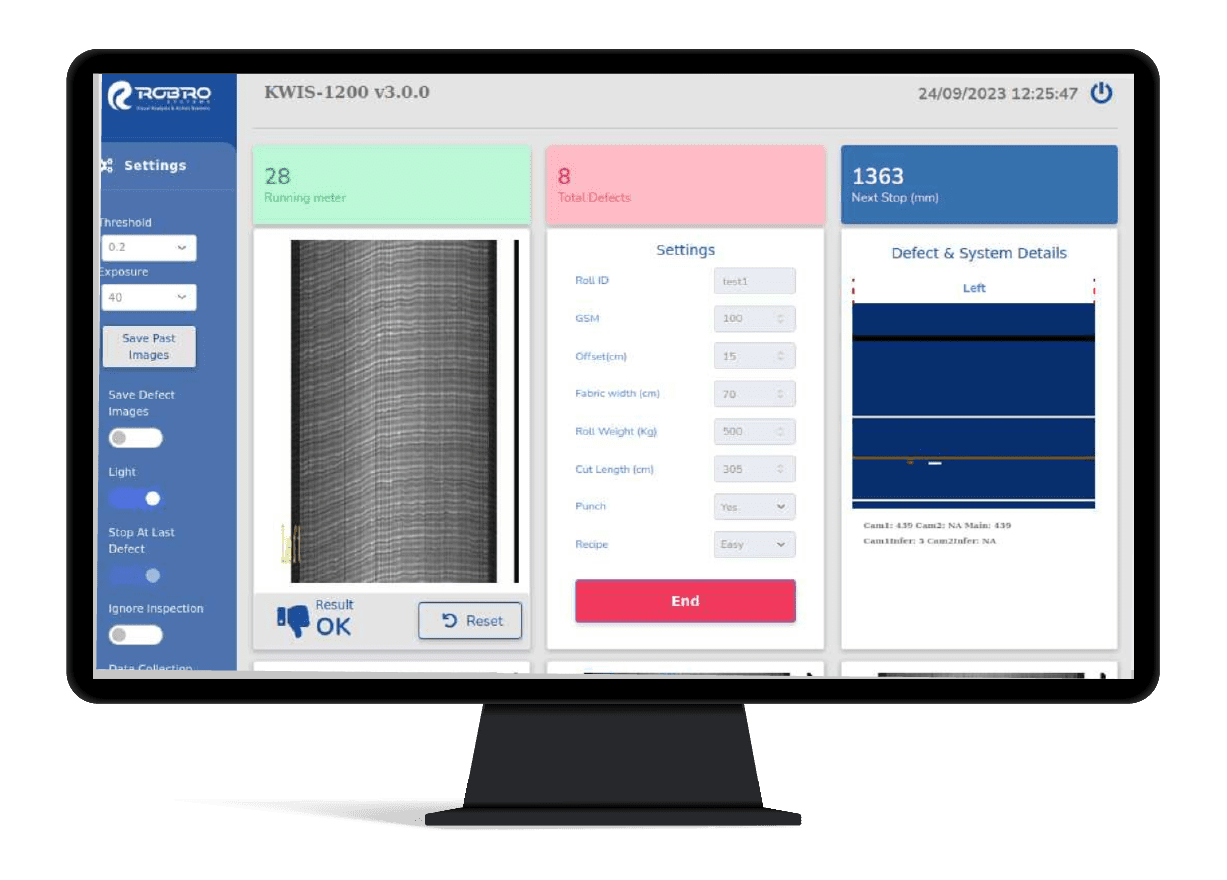
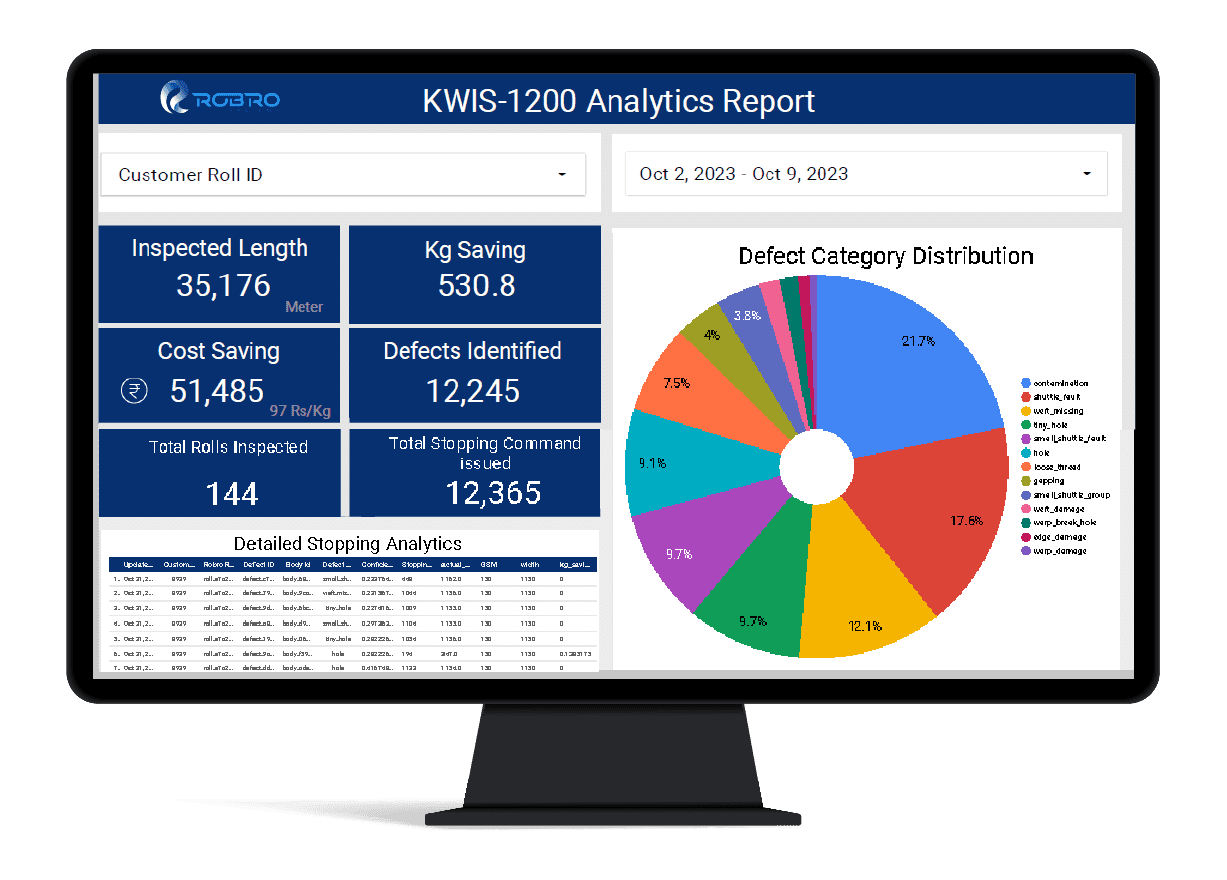
Testimonials
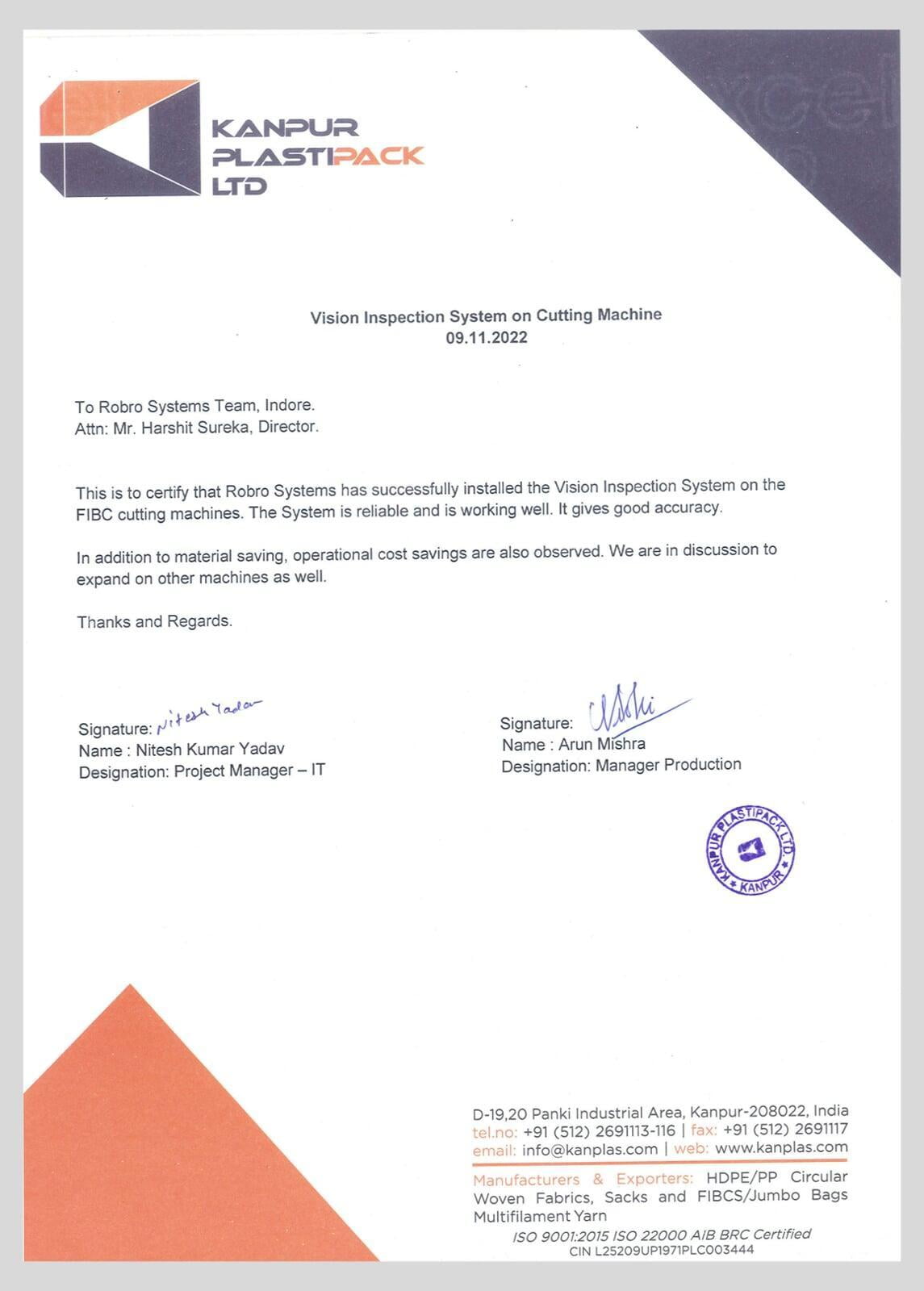
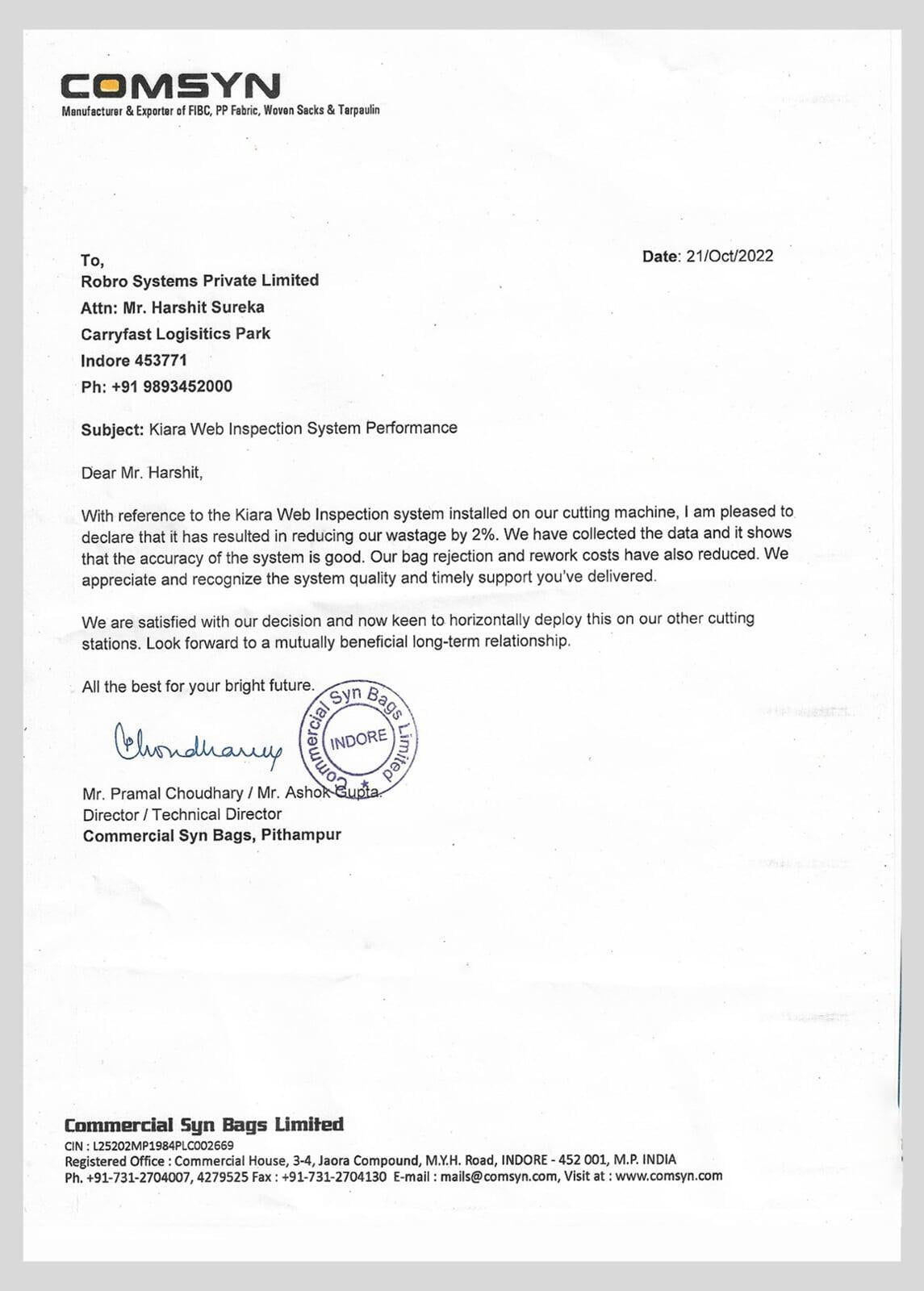
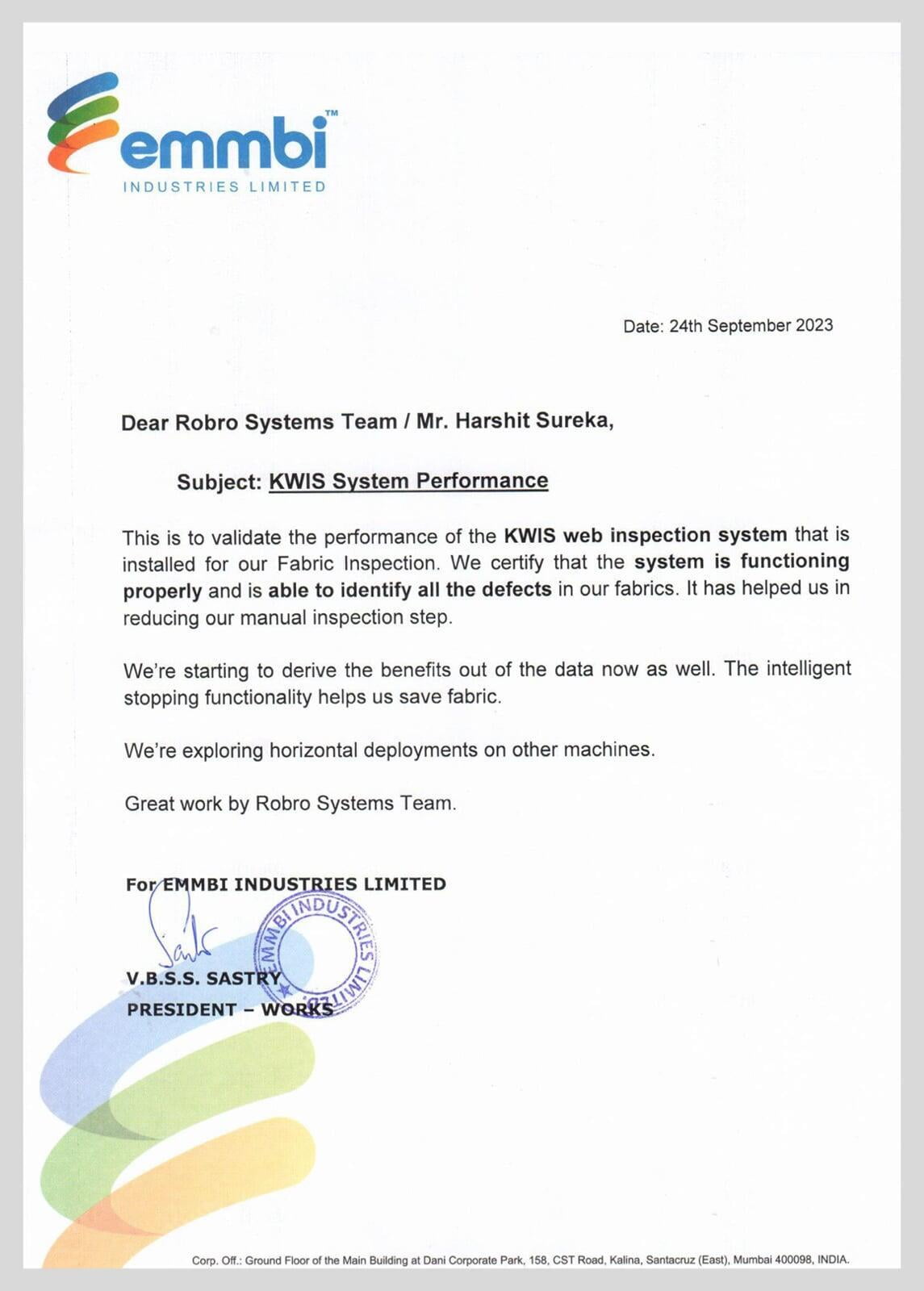
Our Clients
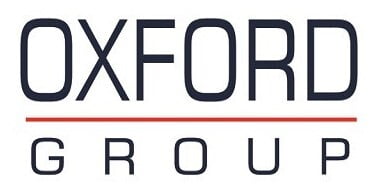

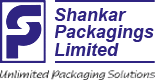
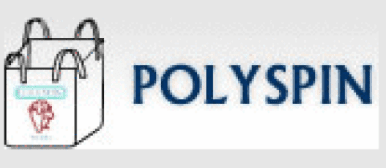
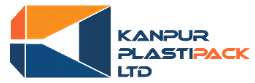
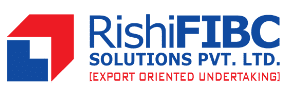
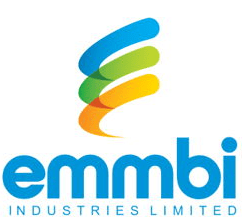
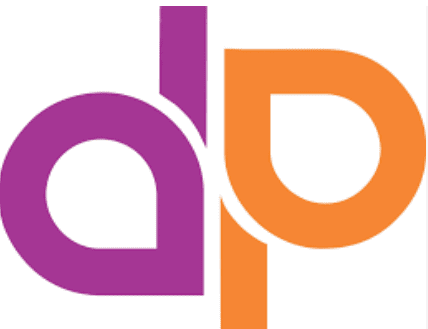
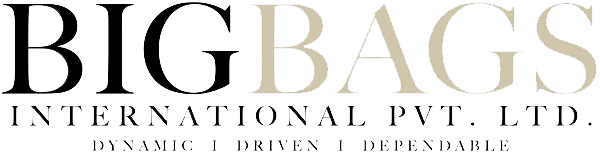
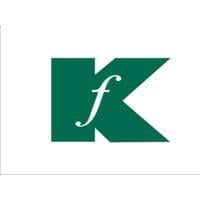
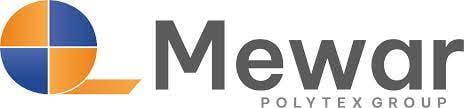
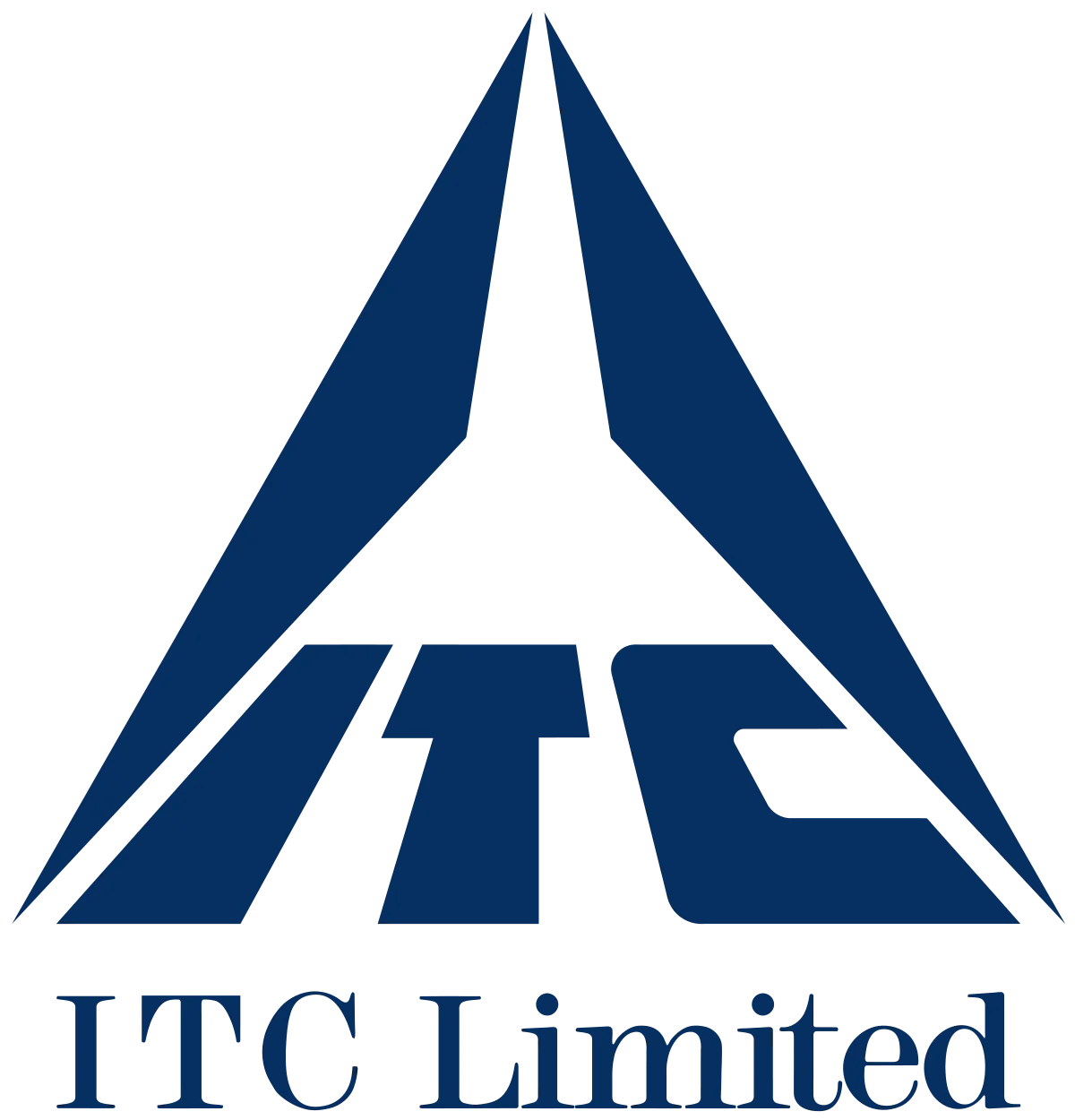
Frequently Asked Questions
What types of defects can KWIS identify in FIBC manufacturing?
KWIS is trained to identify 15 different categories of defects. These include holes, warp and weft damage, shuttle faults, knots, loose threads, contamination, gapping, edge damage among others.
What is the difference between inspection for flat and circular fabric?
Inspection is done only from the top side for flat fabrics. However, defects at the bottom surface in circular and tubular fabrics need additional cameras in the bottom for inspection.
How does KWIS enhance quality in FIBC manufacturing?
The Kiara Web Inspection System identifies all defects and takes action to eliminate them at an early stage. This ensures defects aren’t passed onto subsequent production stages and improves overall quality.
How does KWIS contribute to waste reduction in FIBC production?
By identifying defects early on in the cutting stage and cutting out only the defected portion, KWIS avoids wastage of any good fabric. In the case of U-panel fabric, it allows for spout blocking and enables more salvage of fabric. This reduces overall waste by over 65%.
What is the return on investment (ROI) period for KWIS in the FIBC industry?
The typical return on investment for the Kiara Web Inspection System installed on an FIBC Cutting machine is 12 months. This includes waste saving, labor cost reduction, quality improvement, and re-work reduction, and data digitization that helps in improving loom and operator efficiency.
How small of a defect can KWIS identify in FIBC manufacturing?
Typical installations are installed to identify defects as small as 1-2 mm.