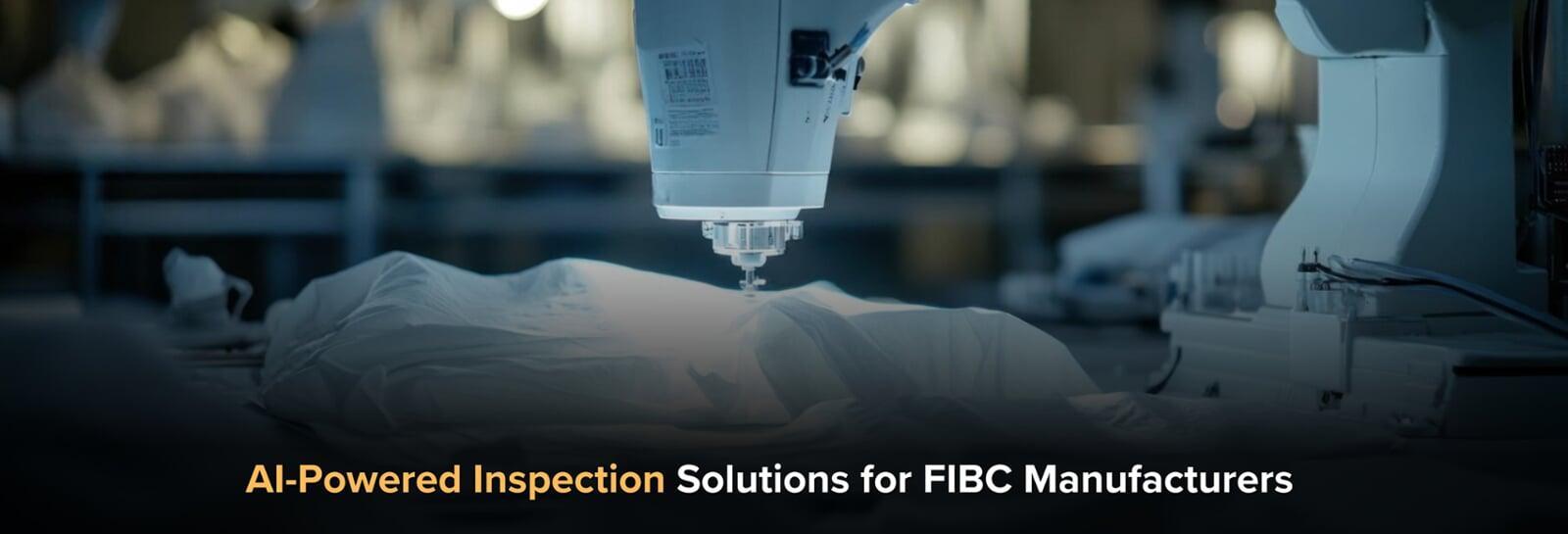
Flexible Intermediate Bulk Containers (FIBCs), commonly known as bulk bags, are critical in agriculture, chemicals, construction, and pharmaceutical industries. These high-capacity fabric containers are designed to efficiently handle, store, and transport dry bulk materials. However, ensuring the structural integrity and quality of FIBCs is paramount, as defects in stitching, fabric strength, contamination, and labeling errors can lead to material losses, safety hazards, and regulatory non-compliance.
Traditional inspection methods rely on human operators and are labor-intensive, slow, and prone to errors. AI-powered inspection solutions are transforming the industry by offering real-time, high-precision defect detection. These solutions enhance quality control, reduce waste, and improve manufacturing efficiency. This blog explores how AI-driven inspection systems are revolutionizing FIBC manufacturing.
What is FIBC?
Challenges in Traditional FIBC Inspection
1) Human Dependency and Inconsistency-Manual inspection relies on visual assessment by operators, which introduces subjectivity and inconsistency. Fatigue, distractions, and human error can lead to missed defects, compromising product quality and safety.
2) Time-Intensive and Costly—Inspecting every bulk bag is time-consuming, especially in high-volume production environments. This increases labor costs and slows down manufacturing throughput.
3) Limited Defect Detection Capabilities- Certain defects, such as micro-tears, contamination, or inconsistencies in tensile strength, may not be visible to the human eye. Traditional inspection methods lack the precision required to identify subtle quality issues.
4) Compliance and Safety Risks- FIBCs must adhere to strict industry standards such as ISO 21898 and UN hazardous goods packaging regulations. Inconsistent quality control can lead to rejected shipments, legal liabilities, and reputational damage.
How AI-Powered Inspection Systems Work
1) Machine Vision for High-Speed Detection
AI-powered systems use high-resolution cameras and advanced computer vision algorithms to scan FIBC surfaces, stitching, lifting loops, and seams. These systems can detect defects such as:
Broken or missing stitches
Fabric tears or weak spots
Contamination (foreign particles, oil stains, dust)
Improperly attached or missing labels
Print misalignment in branding and instructions
2) Deep Learning for Defect Classification
AI models trained on vast defect datasets can identify patterns and classify defects with 99.99% accuracy. These deep learning models continuously improve, learning from past inspections to enhance detection capabilities over time.
3) Real-Time Monitoring and Automation
AI inspection solutions integrate with manufacturing execution systems (MES) and industrial IoT (IIoT) platforms and provide real-time defect alerts. This allows manufacturers to take immediate corrective action, reducing material waste and minimizing production downtime.
4) Hyperspectral Imaging for Contaminant Detection
AI-powered hyperspectral imaging goes beyond traditional cameras by analyzing light wavelengths to detect contaminants invisible to the human eye. This is crucial for FIBCs used in food, pharmaceutical, and chemical applications where contamination risks must be mitigated.
Key Benefits of AI-Powered FIBC Inspection
1) Unparalleled Accuracy and Consistency—AI-powered inspection systems eliminate human subjectivity, achieving near-perfect defect detection and ensuring uniform quality across all manufactured FIBCs.
2) Enhanced Production Efficiency—Automated inspection operates at high speeds, boosting production throughput by 300%. This enables manufacturers to meet increasing demand without compromising quality.
3) Reduced Waste and Rework- Early defect detection prevents defective products from progressing down the production line, reducing waste and rework costs. Manufacturers can optimize material usage and minimize resource wastage.
4) Compliance with Industry Standards—AI-powered systems ensure that FIBCs consistently meet ISO, UN, and other regulatory requirements, reducing the risk of non-compliant shipments and legal complications.
5) Data-Driven Quality Control- AI-based inspection solutions generate real-time analytics, enabling predictive maintenance and process optimization. Manufacturers can track defect trends, pinpoint recurring issues, and refine production strategies.
Future of AI in FIBC Quality Control
1) Predictive Analytics for Defect Prevention—AI-driven analytics can detect defects and predict potential quality issues before they occur, allowing for proactive intervention.
2) Robotics-Integrated Inspection- Future AI solutions will incorporate robotic arms equipped with high-precision sensors, further automating the inspection process and eliminating human intervention.
3) Blockchain for Traceability- AI-powered quality data and blockchain technology will enable complete traceability, ensuring end-to-end transparency in FIBC manufacturing and supply chains.
4) Quantum Computing for Advanced Image Processing- Quantum-enhanced AI algorithms will significantly improve defect recognition speed and accuracy, setting new benchmarks for FIBC inspection technology.
Conclusion
AI-powered inspection solutions are transforming FIBC manufacturing by providing unmatched precision, speed, and reliability in quality control. By integrating deep learning, machine vision, hyperspectral imaging, and real-time analytics, these systems offer 99.99% defect detection accuracy, 300% faster production speeds, and reduced material waste. As AI technology advances, the future of FIBC inspection will see predictive analytics, robotics, blockchain traceability, and quantum-powered image processing redefining industry standards. For FIBC manufacturers, adopting AI-driven inspection is no longer an option—ensuring product quality, regulatory compliance, and competitive advantage in a rapidly evolving market is necessary.