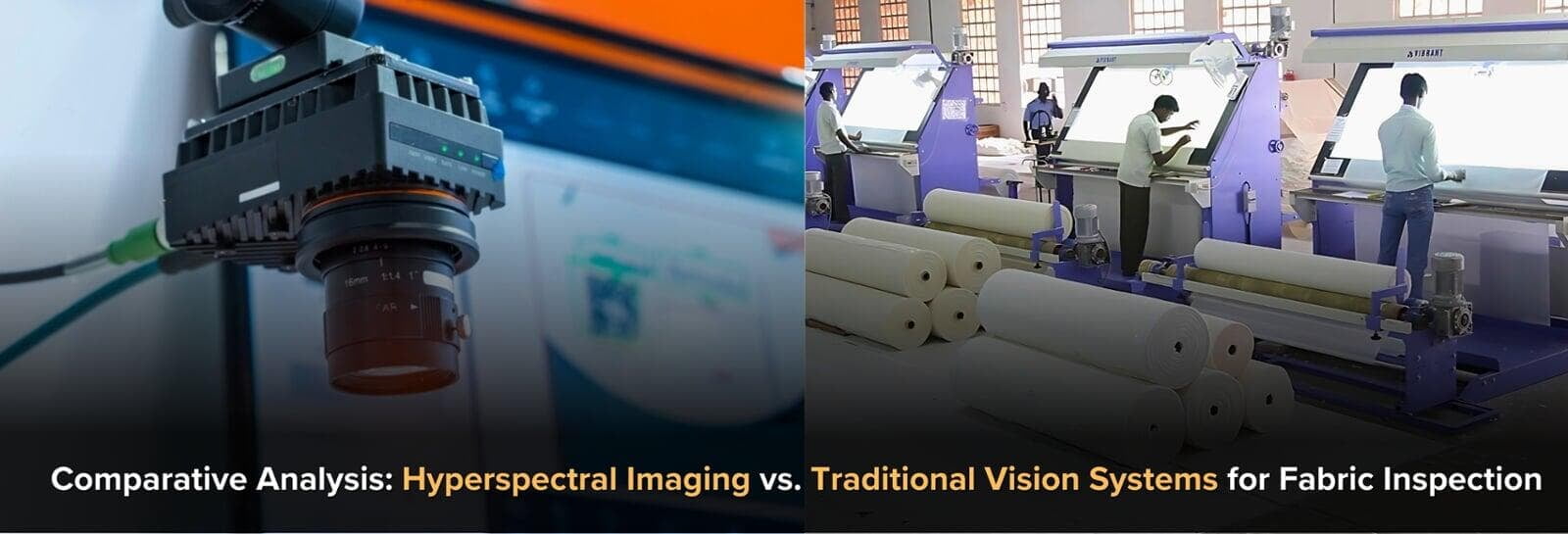
Fabric inspection ensures product quality, particularly in technical textiles, automotive fabrics, and medical textiles. While traditional vision systems have been the go-to solution for many years, hyperspectral imaging (HSI) technology is a game-changer for manufacturers looking to take quality control to the next level. This blog explores the strengths and limitations of traditional vision systems and HSI, with real-time examples of how HSI is revolutionizing fabric inspection.
Key Features
Hyperspectral imaging (HSI) captures surface-level and internal defects, offering a more comprehensive inspection than traditional vision systems, which only detect surface issues.
HSI enables real-time, non-destructive testing, essential for industries like technical textiles, where fabric integrity must be maintained throughout the inspection.
Traditional vision systems are faster but limited to visible light, while HSI can capture data across a more comprehensive spectral range (UV, IR), making it more versatile for advanced materials.
HSI allows for detailed material classification, improving the quality control of high-performance textiles like fire-resistant and medical fabrics.
Though HSI requires a higher initial investment, its long-term cost savings through defect reduction and product optimization justify the expense.
Companies have reported significantly reduced defects and improved product quality in practical applications, especially in sectors with stringent quality requirements like technical textiles.
Market trends show rapid growth for HSI in industries such as textiles, driven by increasing demands for precision and quality.
Traditional Vision Systems: Efficiency and Limitations
Traditional machine vision systems use optical cameras to capture high-resolution images of the fabric as it moves along the production line. The system then analyzes these images to detect surface-level defects such as tears, stains, or weaving inconsistencies. Traditional vision systems have proven fast, cost-effective, and can inspect standard fabrics for many industries. However, these systems have limitations when detecting deeper internal issues within the fabric.
Advantages:
Speed: Traditional vision systems are highly efficient and ideal for fast-moving production lines.
Affordability: These systems have been used for years, making them relatively inexpensive to install and maintain.
Challenges:
Surface-Level Only: Traditional systems are restricted to detecting defects visible on the surface, leaving more complex internal issues undetected.
Environmental Sensitivity: Variations in lighting conditions can affect the accuracy of traditional vision systems, leading to missed defects or false positives.
Traditional vision systems provide an adequate solution for many manufacturers producing basic textiles. However, more advanced systems like hyperspectral imaging are necessaryfor technical textiles requiring deeper analysis.
Hyperspectral Imaging: The New Standard in Precision
Benefits:
Comprehensive Defect Detection: HSI detects both surface-level and internal defects, including inconsistencies in fabric composition, moisture content, and even chemical composition.
Non-Destructive Testing: HSI can inspect fabrics without causing physical damage, ensuring the integrity of the product during the inspection process.
Material-Specific Insights: The technology allows for a detailed analysis of the fabric’s chemical and physical properties, making it ideal for high-performance applications like technical textiles, medical textiles, and protective gear.
Challenges:
Higher Costs: HSI systems are more expensive than traditional vision systems, but the long-term benefits of quality control and waste reduction often justify the investment.
Slower Inspection Speeds: While HSI isincredibly detailed, it is generally slower than traditional systems, making it less suited for ultra-fast production lines.
Comparative Analysis: Traditional vs. Hyperspectral
Feature | Traditional Vision Systems | Hyperspectral Imaging |
Inspection Depth | Surface-level defects only | Surface and internal defects |
Speed | High-speed, fast inspection | Slower, more detailed inspection |
Cost | More affordable | Higher upfront investment |
Versatility | Limited to visible light | Full-spectrum analysis (UV, IR) |
Suitability | Standard fabric defects | High-performance, technical textiles |
Sensitivity to Environment | Sensitive to lighting conditions | Less affected by lighting issues |
This is a Heading
At Robro Systems, the integration of hyperspectral imaging has transformed fabric inspection processes, particularly in industries requiring the highest quality control levels. For example, one client specializing in fire-resistant textiles implemented Kiara Vision AI with HSI to detect chemical inconsistencies in protective fabrics. Traditional systems could not catch these discrepancies, which could have compromised the product’s fire-resistant properties. With the addition of HSI, the manufacturer achieved a 35% reduction in defects, ensuring higher end-user safety.
Another case involved the inspection of medical textiles, where moisture content is a critical factor in maintaining the material's sterility. Traditional vision systems could not adequately detect inconsistencies in moisture levels, which could lead to failed sterilization and product recalls. After incorporating hyperspectral imaging, the manufacturer identified and corrected these defects earlier in the production line, leading to a 25% improvement in product quality.
Industry Insights and Market Growth
The market for hyperspectral imaging is proliferating, driven by increased demand for precision in industries like textiles, food, agriculture, and healthcare. A report by Markets and Markets projects the hyperspectral imaging market to grow from USD 12.5 billion in 2021 to USD 17.6 billion by 2026, at a CAGR of 7.1%. This growth reflects a broader trend toward adopting advanced quality control solutions as manufacturers seek to maintain competitiveness in increasingly demanding markets.
Conclusion: The Future of Fabric Inspection
As textile manufacturers face increasing pressure to deliver high-quality products, choosing the right inspection technology becomes critical. While traditional vision systems offer speed and affordability, hyperspectral imaging provides unparalleled precision, making it the preferred choice for industries requiring more profound, comprehensive inspections.
At Robro Systems, we are dedicated to helping manufacturers optimize their fabric inspection processes. Our KWIS integrates hyperspectral imaging to deliver precise, real-time defect detection, ensuring higher product quality and reduced waste. Whether you’re looking to upgrade your current inspection setup or explore the benefits of hyperspectral imaging, Robro Systems has the solution to meet your needs.