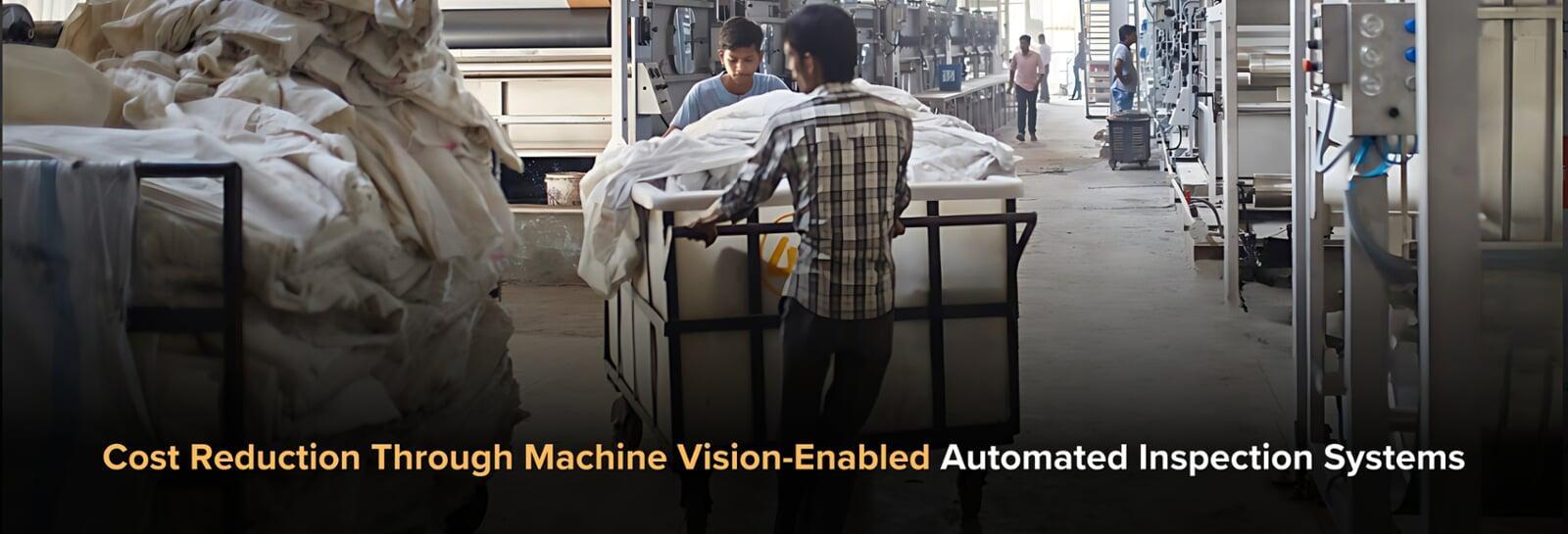
What is Machine Vision and Automated Inspection?
How Does Machine Vision Enable Cost Reduction?
1) Real-time Defect Detection
2) Reduction in Labor Costs
3) Improved Process Efficiency
4) Minimizing Waste
5) Enhanced Yield and Quality Control
Overcoming Challenges in Machine Vision Adoption
Despite its numerous benefits, implementing machine vision systems has specific challenges. Understanding these challenges and how to address them is essential for their successful adoption.
1) Integration with Existing Systems
2) Cost of Implementation
3) Complexity of Image Processing
4) Training and Skill Development
Benefits of Machine Vision Systems in Cost Reduction
1) Higher Production Output
2) Reduction in Scrap and Rework
3) Lower Labor Costs
4) Minimizing Material Waste
5) Improved Customer Satisfaction
Technical Innovations in Machine Vision for Cost Reduction
1) AI and Deep Learning
2) Hyperspectral Imaging
3) 3D Imaging and Depth Sensing
4) Edge Computing
5) Multi-Camera Systems
Real-World Applications of Machine Vision in Cost Reduction
Conclusion
Machine vision systems have the potential to significantly reduce manufacturing costs by automating inspection, improving quality control, and increasing efficiency. In the technical textile industry, where precision and quality are paramount, these systems help ensure that products like FIBC bags, tire cords, and conveyor belts meet the highest standards while reducing waste, labor costs, and rework.
At Robro Systems, we specialize in providing machine vision solutions that optimize production processes. Our Kiara Web Inspection System (KWIS) is designed to help manufacturers in the technical textile industry improve defect detection, minimize waste, and reduce operational costs. Whether in tire cord production, conveyor belt manufacturing, or FIBC inspection, Robro Systems has the right solution.
Ready to enhance your quality control processes and reduce costs? Contact Robro Systems today to learn more about our innovative machine vision solutions and how they can transform your production line.