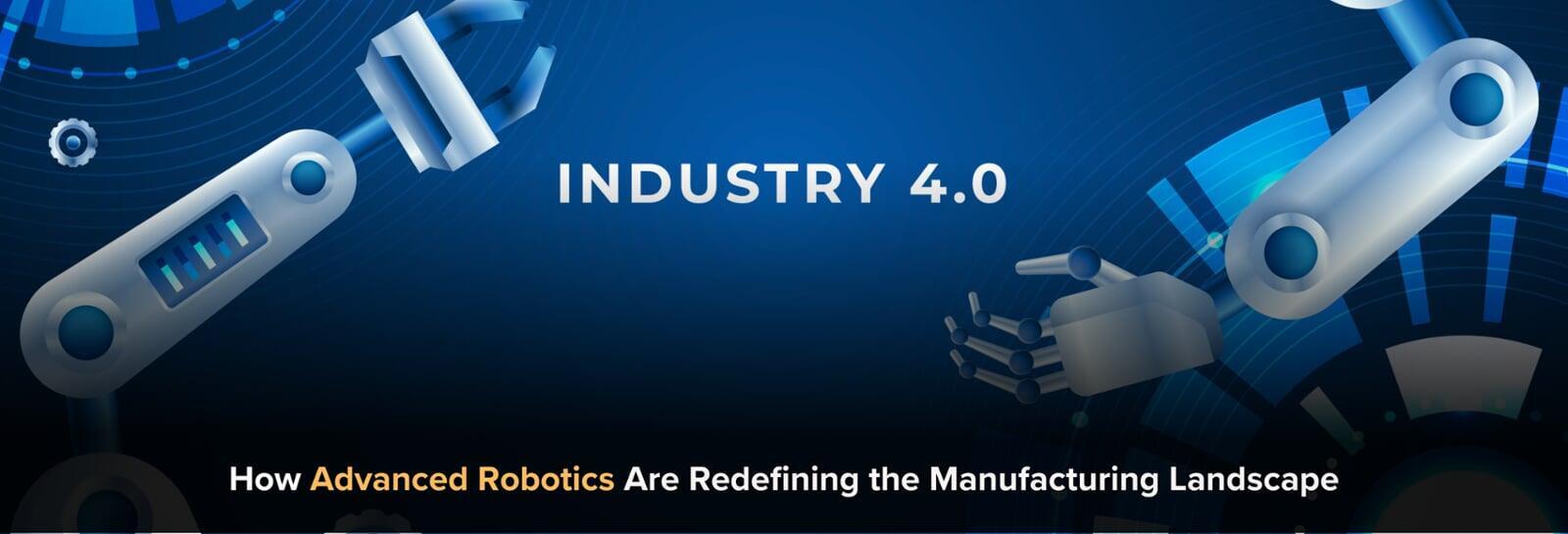
What Are Advanced Robotics in Manufacturing?
How Advanced Robotics Are Transforming Manufacturing
1) Precision-Driven Quality Control
2) Accelerated Production Cycles
3) Enhanced Worker Safety
4) Real-Time Monitoring and Adjustments
5) Sustainability Through Waste Reduction
Overcoming Challenges in Robotic Integration
1) High Initial Costs
2) Integration with Existing Systems
3) Skill Gaps
4) Maintenance and Downtime
Technical Innovations Propelling Advanced Robotics
Machine Vision Systems- Machine vision technology empowers robots to inspect technical textiles with unmatched precision. Cameras with high resolutions and AI algorithms analyze fabric weaves, detect micro-defects, and evaluate coating uniformity. For example, machine vision ensures precise alignment and thickness in tire cord manufacturing, reducing material wastage and enhancing product reliability.
AI-Driven Adaptability—Advanced robotics leverage AI to adapt dynamically to varying production conditions. For example, robots used in airbag fabric production can adjust their inspection thresholds based on detected patterns or anomalies, ensuring consistent quality even in high-speed operations. This adaptability enhances production efficiency and minimizes human intervention.
Collaborative Robotics (Cobots)- Cobots, designed to work alongside human operators, are revolutionizing tasks like material handling and quality inspection in the technical textiles industry. Their ability to perform repetitive tasks accurately allows human workers to focus on more strategic roles, fostering a collaborative manufacturing environment.
Enhanced Mobility and Flexibility- Modern robots are built with modular designs, enabling them to switch between tasks such as defect detection in airbag fabrics and conveyor belt material analysis. This flexibility reduces capital expenditure by allowing manufacturers to use the same robotic systems across different production lines.
IoT-Enabled Data Analytics- IoT integration enables robots to collect, process, and share real-time data across the manufacturing ecosystem. This data helps optimize production parameters, predict maintenance needs, and improve efficiency. For instance, IoT-enabled robots in technical textiles can analyze environmental conditions, such as humidity and temperature, and adjust processes accordingly.
Real-World Applications of Robotics in Technical Textiles
Airbag Fabric Inspection—Robotic inspection systems scan airbag fabrics for defects such as weak weaves or uneven coatings. They use machine vision and AI to identify potential flaws early, ensuring only high-quality materials proceed to assembly. This guarantees passenger safety and reduces material wastage by preventing defective batches from progressing.
Tire Cord Fabric Manufacturing- Tire cord fabrics require consistent tensile strength and coating uniformity. Robotic systems analyze these parameters during production, using AI to classify defects and suggest real-time corrections. This ensures compliance with stringent automotive standards while minimizing resource wastage.
Conveyor Belt Fabric Optimization- Even minor defects can compromise product durability in conveyor belt manufacturing. Robotic systems with sensors and AI algorithms inspect fabric layers for strength and adhesion quality. Manufacturers can take corrective actions by identifying issues early enhancing product reliability and lifespan.
Coated Technical Textiles- Advanced robotics are instrumental in inspecting coated textiles, ensuring the application of uniform coatings without bubbles, wrinkles, or inconsistencies. These systems detect imperfections and provide actionable insights to refine coating processes, reducing material costs and improving production outcomes.
Robro Systems: Driving Innovation in Advanced Robotics
Customized Solutions for Industry-Specific Needs- Robro Systems provides tailored robotic solutions designed to meet the unique challenges of technical textile manufacturing. From defect detection to automated material handling, our systems are engineered to enhance productivity and quality.
Seamless Integration for Maximum Efficiency- Our robotic systems are designed for seamless integration with existing production lines. With modular configurations, they adapt to different manufacturing needs, ensuring maximum flexibility and utility.
Innovation and Excellence- Robro Systems prioritizes innovation, combining AI, machine vision, and industrial expertise to deliver state-of-the-art solutions. Continuously investing in research and development ensures our customers stay ahead in a competitive market.
Conclusion
Robotics' integration into real-world applications, such as inspecting airbag fabrics, tire cords, and conveyor belts, demonstrates its significant impact on quality control and operational excellence. These systems ensure defect-free production while reducing waste and optimizing resources—a critical requirement for modern manufacturers striving for sustainability and competitiveness.
For manufacturers in technical textiles, leveraging robotic systems is no longer optional but essential to stay ahead in an ever-evolving industry. The combination of precise defect detection, predictive analytics, and seamless human-robot collaboration offers a competitive advantage that cannot be overlooked.
At Robro Systems, we understand the intricate needs of technical textile manufacturers. Our tailored solutions, such as the Kiara Vision System, embody cutting-edge robotics and AI to deliver unmatched inspection capabilities. From ensuring consistent quality to boosting production efficiency, Robro Systems is your partner in navigating the future of smart manufacturing.