Manufacturing industry is highly dynamic and the first impression of the products and brands is their packaging. If a defect or mislabel is not noticed before reaching the customers, the outcomes can be disastrous.
Research shows that consumers form their first impression about products in only seven seconds. Can you imagine the possible results if your factory overlooked packaging and print defects? Such unnoticed defects may result in severe losses for your business, which makes inspection for quality control a crucial function.
Here are some common printing and packaging errors:
Types of Packaging and Possible Defects-
Packaging Type | Critical defects | Major defects | Minor defects |
Glass containers | Penetrating checks and cracks Contamination with dust, insects, other foreign matters Chipped or broken finish | Glass weight less than minimum specified Non-functional stretching bead Leaner is over standard norms | Wavy appearance Stones Uneven outer surfaces |
Plastic packages | Breaks or cracks Thickness is below specified limits Rough cut off resulting in leaky closure | Below minimum weight Dimensions outside limits Leaner’s over standard norms | Streaky pigmentation due to inadequate binding |
Closures | Crack in metal caps Missing liners Outside permissible stress cracking dimension | Loose or hanging liners Orange or rough pill surfaces Consumer-related faults | Scratches on the caps’ external surfaces |
Metallic packages | Seals leakages Cracks on ends or body Contamination | Dents affecting closing efficacy Out of round at open ends | External scratches |
Labels | Incorrect copy or size Tears and holes In stick together Missing colours | Rough weight edges | Loose bonding Improper label identification |
Blister packages | Holes or cracks Wall thickness below specified norms | Embedded foreign particle Visual defects Discolouration | Drawing or mould lines |
Cartons | Dimensions beyond tolerance limits Tears or holes | Scoff surfaces Ink spreading | Outer surface stains |
Aluminium foil | Core damages Missing sealing layer | Width variations Poor resistance | Lamination scratches Bead over foil surface Improper sealing |
Limitations Of Manual Inspection
Traditionally, manual inspection is common practice in the packaging and printing industry. However, this method of quality control has certain limitations as below:
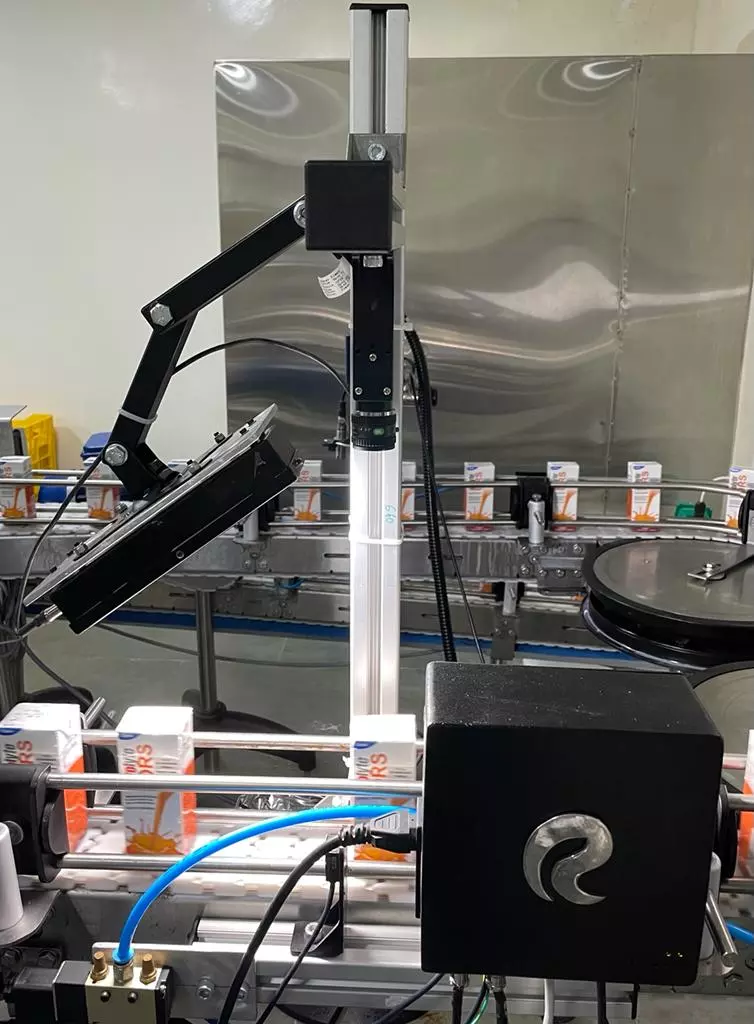
The printing and packaging industry faces several challenges and line cameras can significantly improve quality control requirements. Machine vision technology can open new opportunities and is capable of providing the best method to detect defects and are customisable based on the specific requirements of your production line.