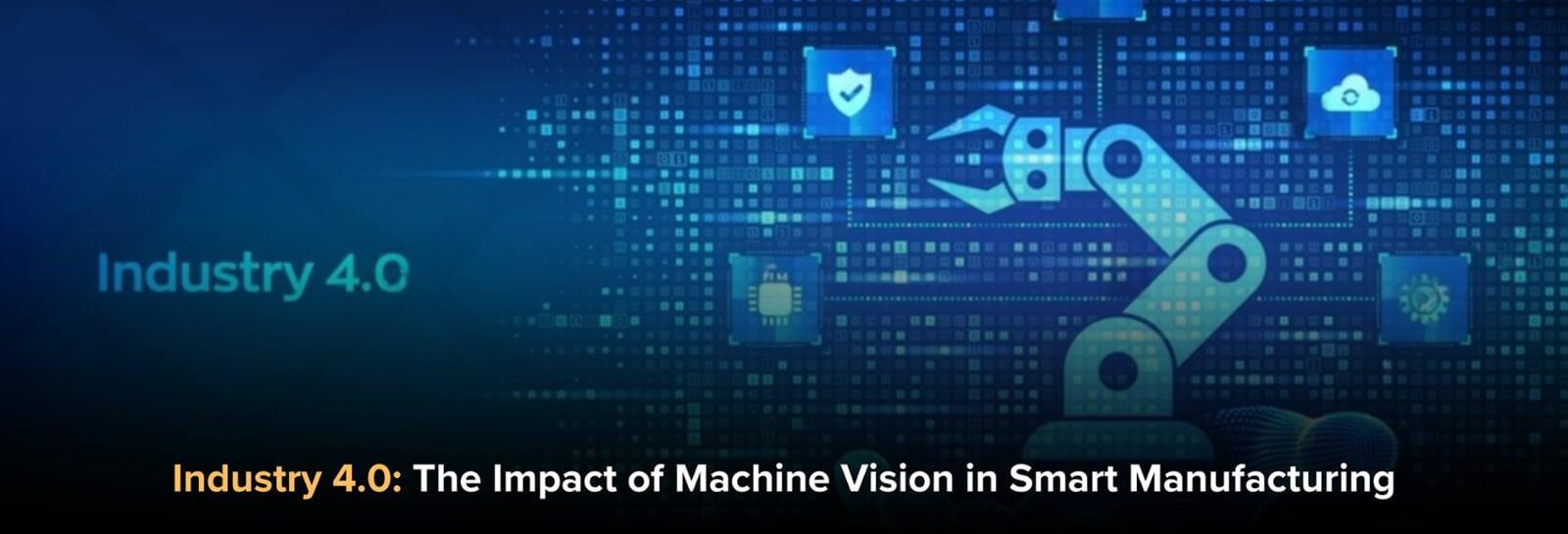
Key Features
Industry 4.0 integrates advanced technologies like AI, machine learning, IoT, and robotics into manufacturing processes, enhancing automation and efficiency.
Machine vision systems play a crucial role in automating defect detection, improving product quality, and increasing production speed in textile manufacturing.
Smart manufacturing leverages real-time data and AI-driven systems to adapt production lines dynamically, minimizing downtime and maximizing throughput.
Machine vision ensures precise inspection of fabrics, detecting defects like holes, uneven weave, and discoloration with high accuracy.
The adoption of AI in manufacturing reduces waste by allowing for early defect detection, saving raw materials, and reducing rework costs.
Machine vision solutions are scalable and can be integrated into existing production lines without significant infrastructure changes.
Advanced defect detection systems help textile manufacturers meet stringent quality control standards, ensuring consistent output and customer satisfaction.
What is Industry 4.0 and Smart Manufacturing?
How Machine Vision Drives Efficiency in Smart Manufacturing
1) Real-Time Defect Detection
2) Improved Quality Control
2) Enhanced Automation
Overcoming Challenges in Machine Vision Adoption
1) High Initial Investment
2) Compatibility with Legacy Systems
3) Data Management
Key Innovations in Machine Vision for Smart Manufacturing
1) Advanced Camera Technology
2) AI-Powered Defect Detection
3) Edge Computing for Faster Analysis
Real-World Applications of Machine Vision in Technical Textiles
1) Tire Cord Manufacturing
2) Conveyor Belt Fabrics
How Robro Systems is Leading the Charge in Machine Vision for Smart Manufacturing
Robro Systems is committed to providing innovative, AI-powered machine vision solutions that meet the specific needs of the technical textile industry. Our flagship product, the Kiara Web Inspection System, is designed to optimize fabric inspection processes and ensure the highest product quality.