There is a high possibility of costly errors associated with injection molding. Quality issues in these products may range from small surface defects to major issues that may affect the performance, safety, and functioning of the products. Injection molding defects may arise due to materials used, molding procedure, tooling design, or a combination of all three.
Injection molding of plastic materials is delicate and subject to defects that affect the product quality. Molding defects can be of different types and also occur due to various reasons. Here are some common types of plastic defects:
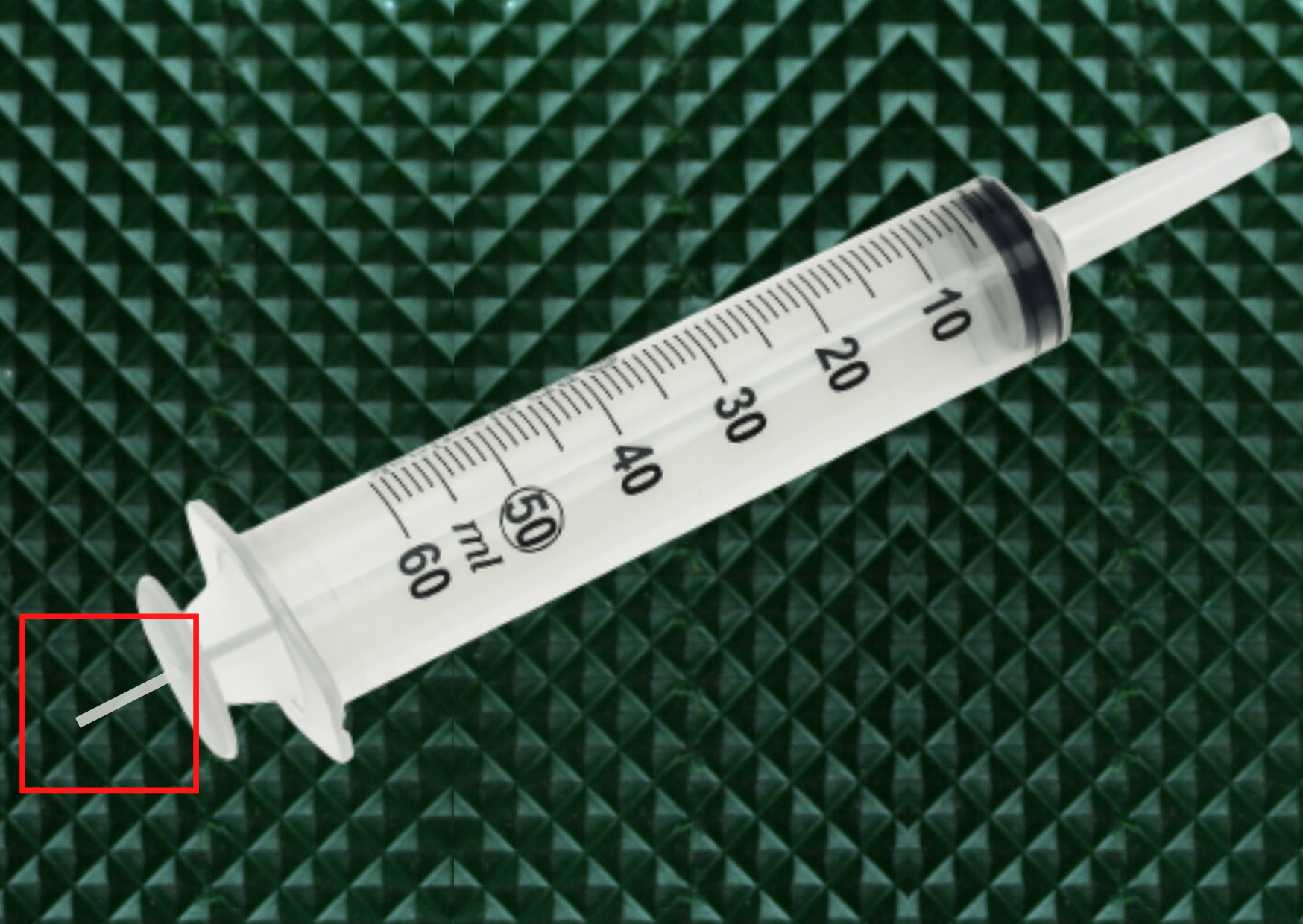
Flash
This is a deformation involving melted plastic solidifying outside and along the parting line between the two halves. Possible causes include distorted mold, high injection output, extra plastic injection, or inadequate mold clamping.
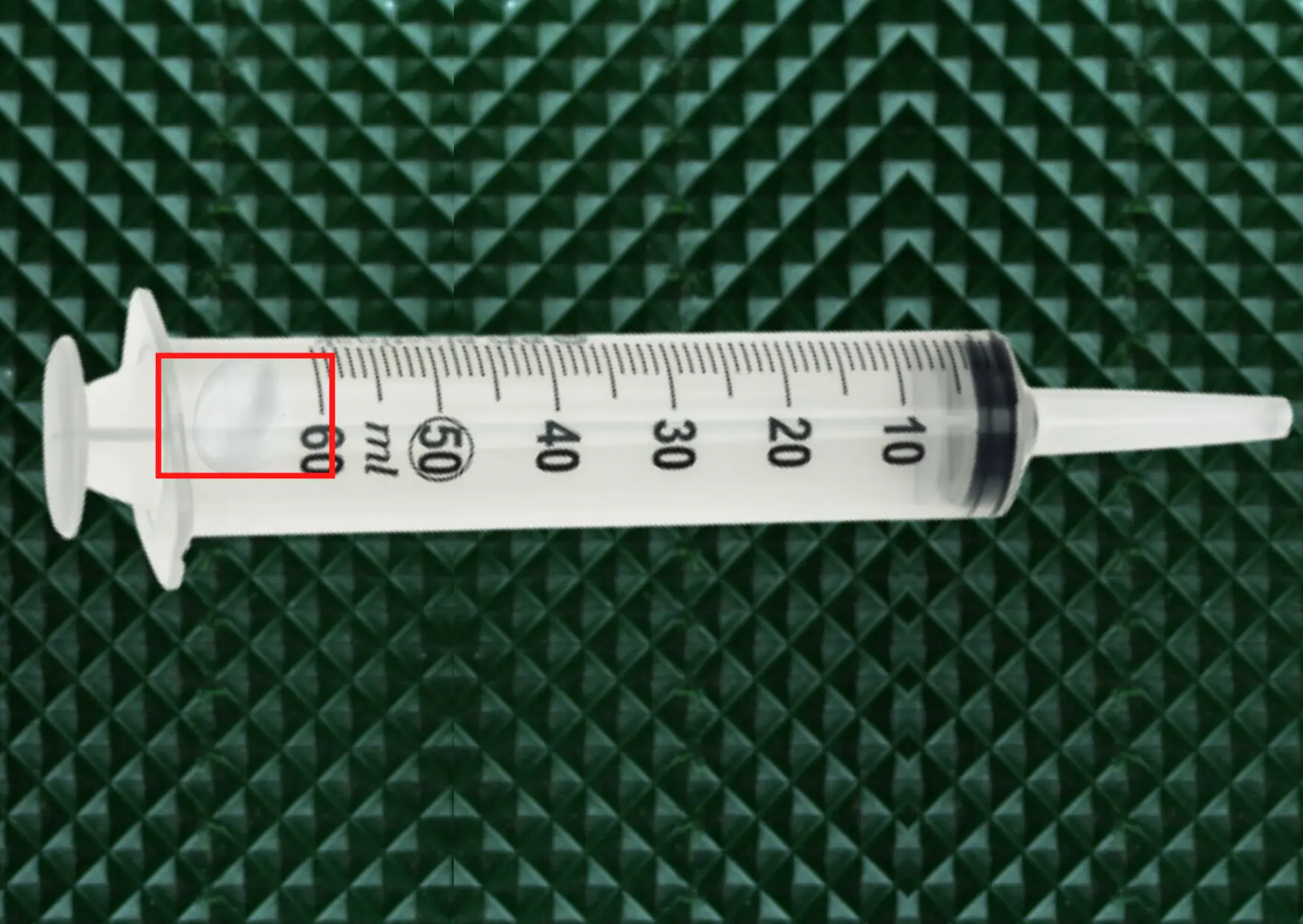
Shrinkage
Also known as a shrink mark, this deformation is a dent in the molded product’s surface. As melted plastic solidifies within the mold, causing inadequate plastic volume results in shrinkage, which causes the dent. Shrinkage inside the molded plastic is known as void.
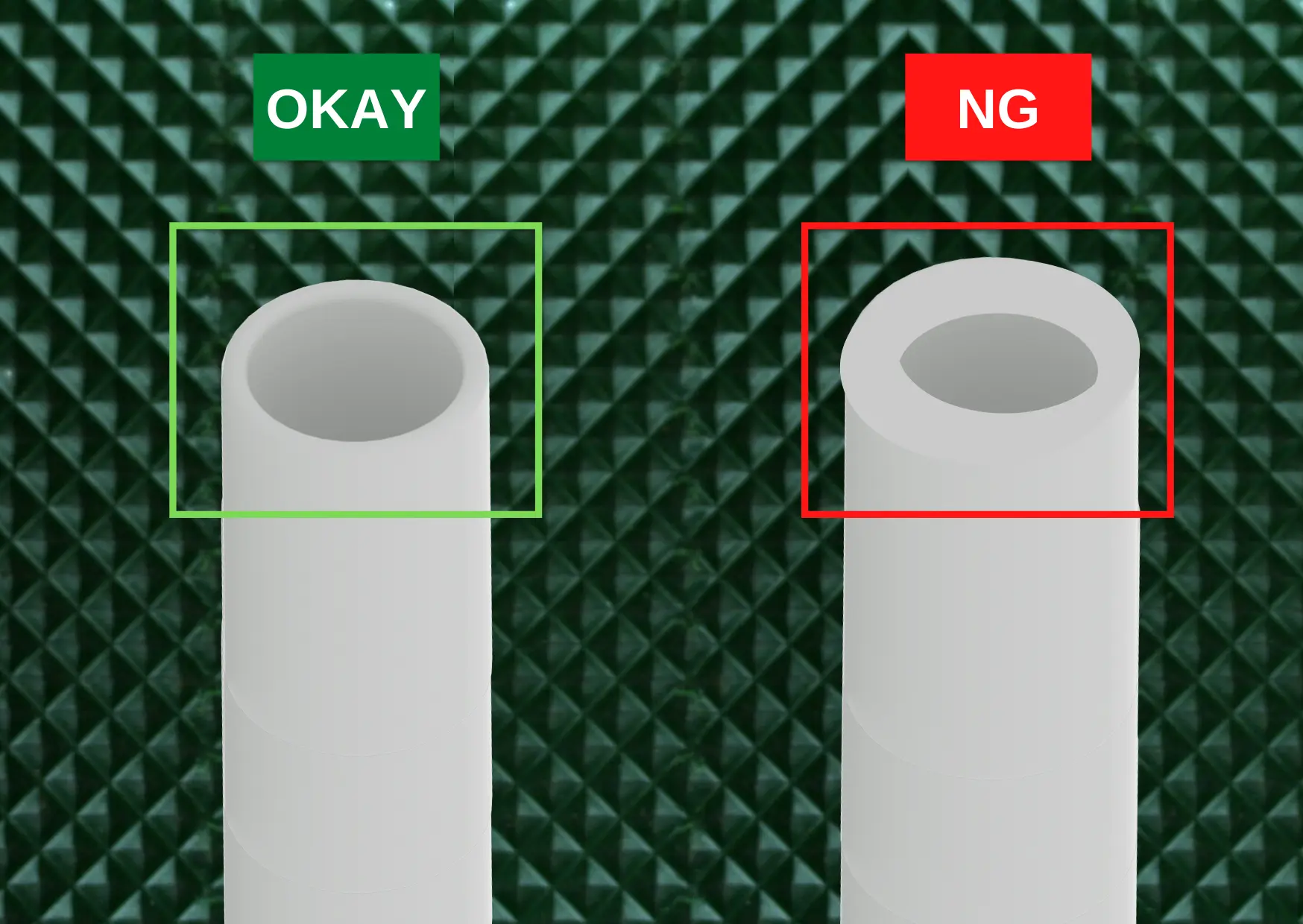
Warpage
It is a deformation wherein the molded products warp in a single direction. These defects may occur due to mold release failure or varying shrinkage rates due to the directional flow of plastic within the mold.
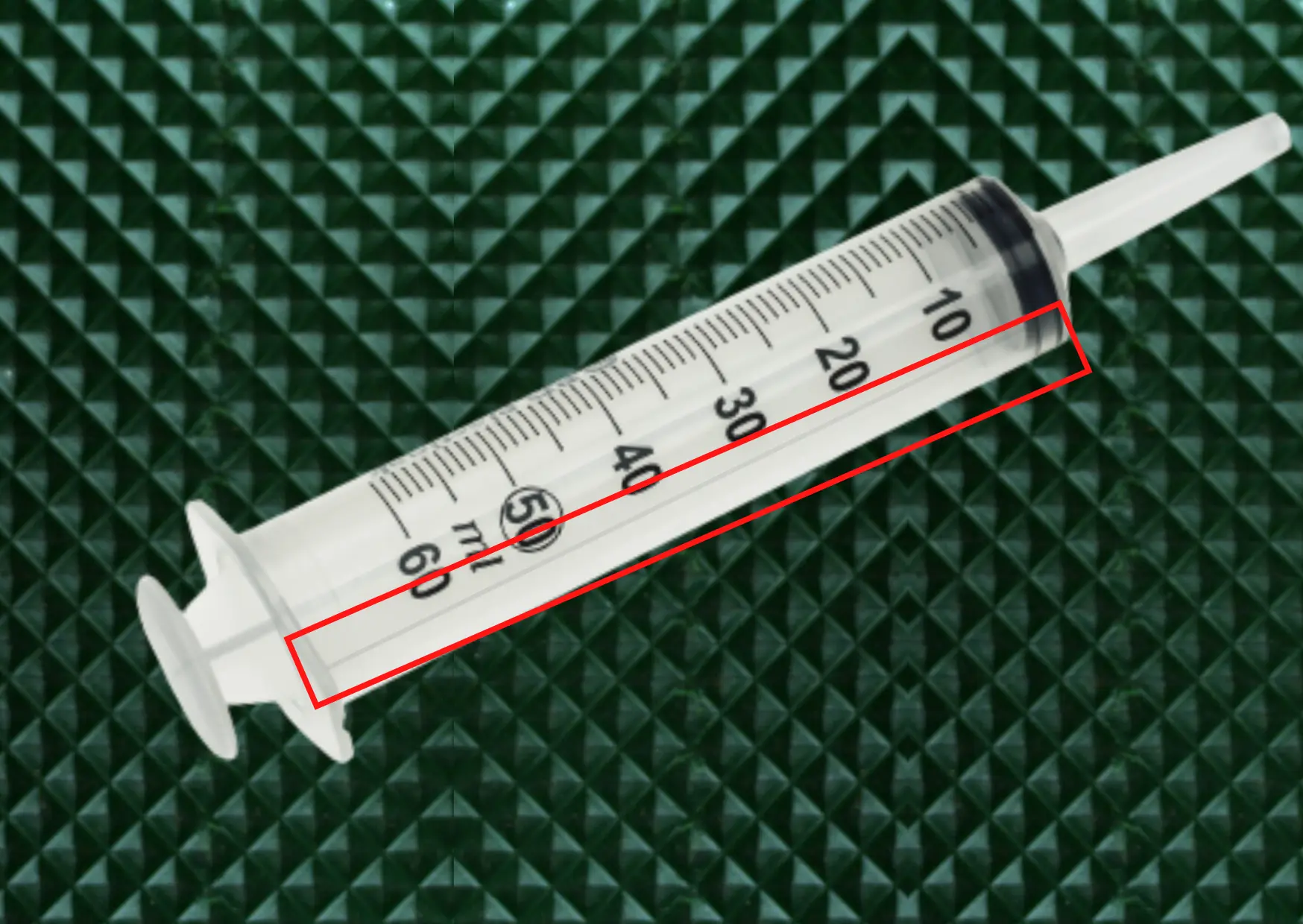
Weld lines
Weld surface defects wherein the weld or the parts where the flow of melted plastic meets within the mold appear as a pattern or groove. Weld lines may result due to inadequate injection pressure and speed or low temperature or fluidity of the melted plastic during the injection molding process.
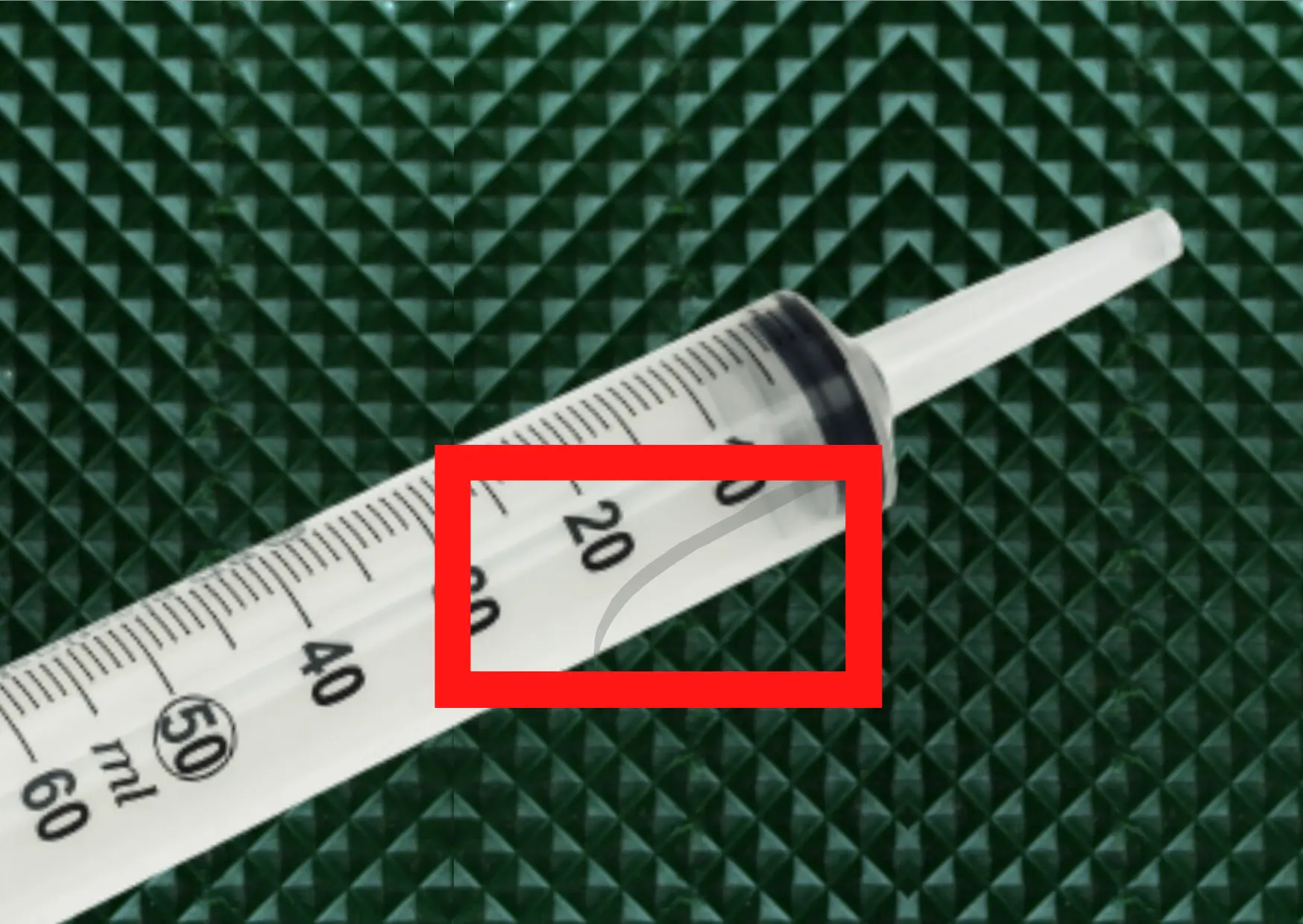
Flow lines
Flow lines are also surface defects that appear as wavy streaks forming ripple-like patterns around the gate. Lower temperature of injected melted plastic or slower injection speed may result in lesser fluidity of plastic within the mold forming the streaks.
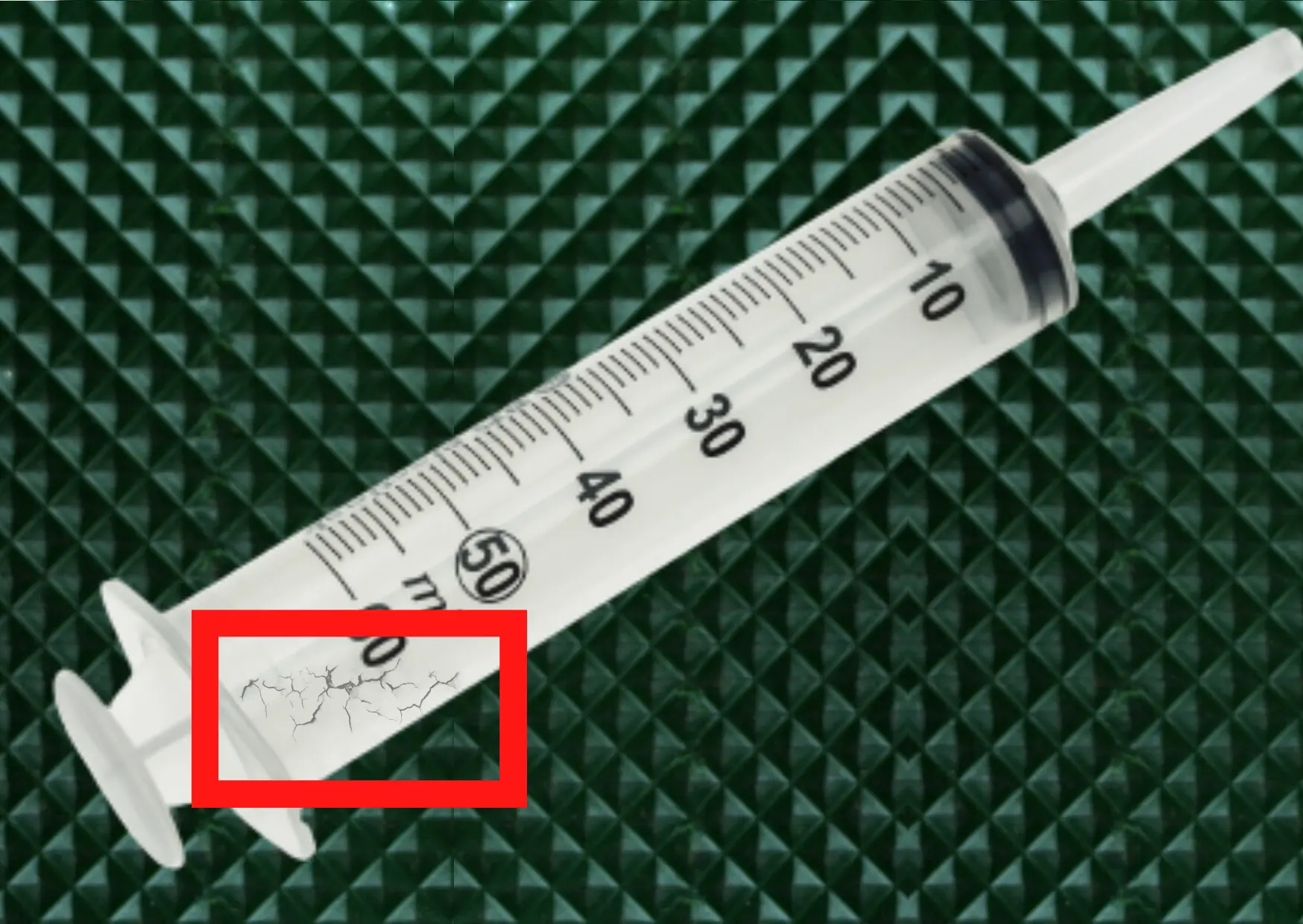
Cracking and crazing
Another kind of surface defect is where fine lines and cracks occur. Such fractures and cracks may result due to internal or external stress.
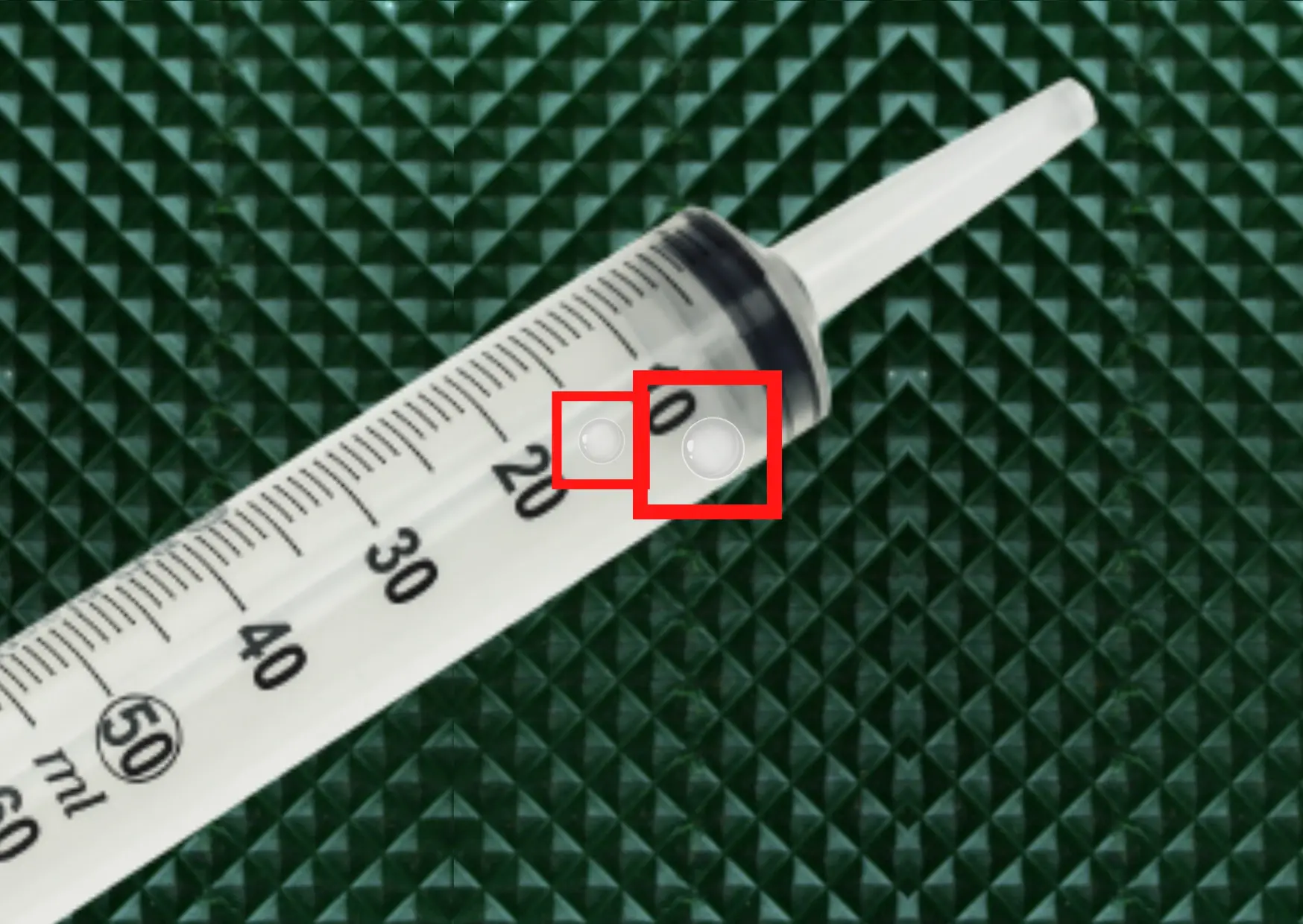
Vacuum voids or air pockets
Stuck air within the mold cavity appears as bubbles. Possible causes include material shrinkage, insufficient cooling, and incomplete injection pressure.
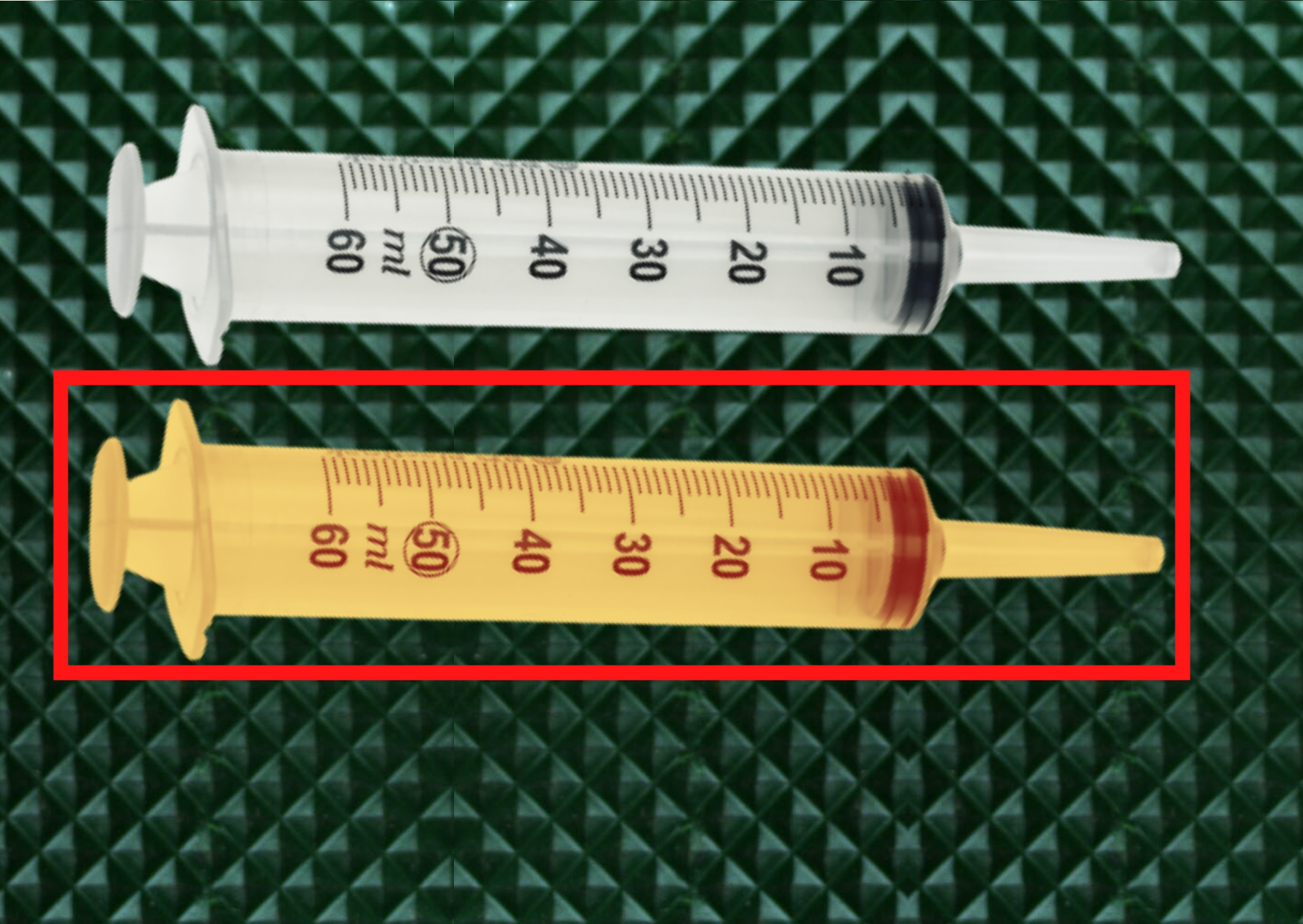
Discoloration
Also known as color streaking, discoloration results when the molded product color is different from the intended color. Often discoloration occurs in localized areas and doesn’t affect the products’ strength. Some causes for color streaking include insufficient mixing of the masterbatch, residual resins or leftover pellets in the nozzle or hopper, incorrect thermal stability of the colorant, or use of different molds from previous runs.
Machine vision to identify molding defects
Detect Every Injection Molding Defect Accurately with AI Vision & Machine Learning
Adhering to stringent global standards for quality assurance is shifting plastic product manufacturers from manual inspection to machine vision technologies to identify defects. Automated inspection not only decreases the costs, but significantly enhances the product quality.
Traditionally, quality inspectors conducted manual inspections, which is a cumbersome and repetitive task, often resulting in fatigue. As a result, molding defects may be overlooked, leading to costly rework, product recalls, and higher personnel costs. Camera vision systems can overcome all these limitations of manual inspections
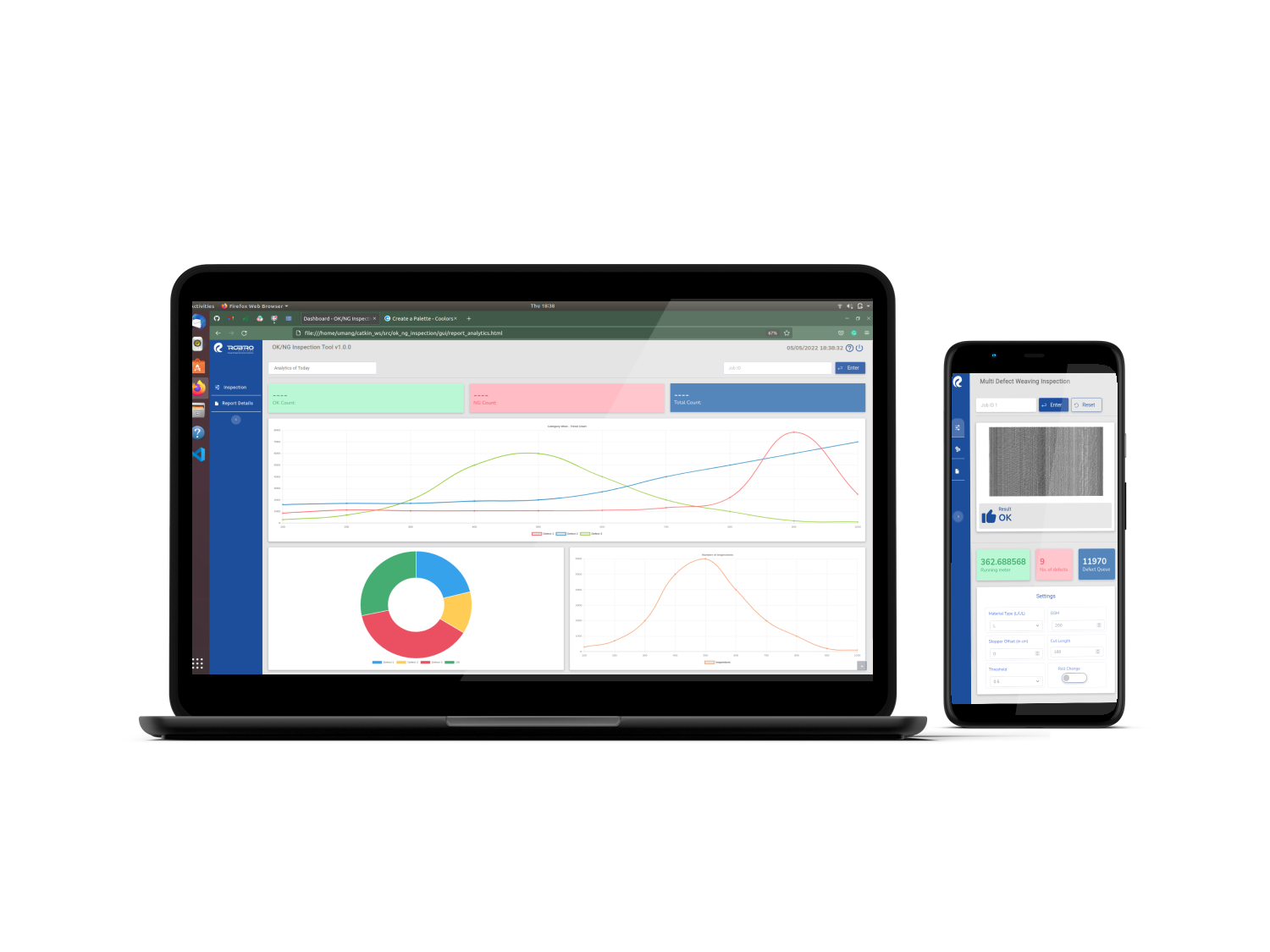
Advanced solutions capture high-resolution images that include Good and No Good results. This allows the software to omit anomalies within the specified tolerance levels and flag those products that have significant defects.
Modern injection molding defects troubleshooting systems combine deep learning, artificial intelligence, and real-time software to deliver accurate and consistent vision inspection and defect detection. Most systems are easy to set up and install and are customizable to suit the specific requirements of every company.
Contrary to common belief, these systems are affordable, and the initial capital investments can be recovered within a short period. These systems reduce personnel costs, rework and recalls, and wastage, which significantly improves profitability. The cost savings coupled with higher quality quickly recover the initial expenditure of setting up machine-based vision systems to identify molding defects.