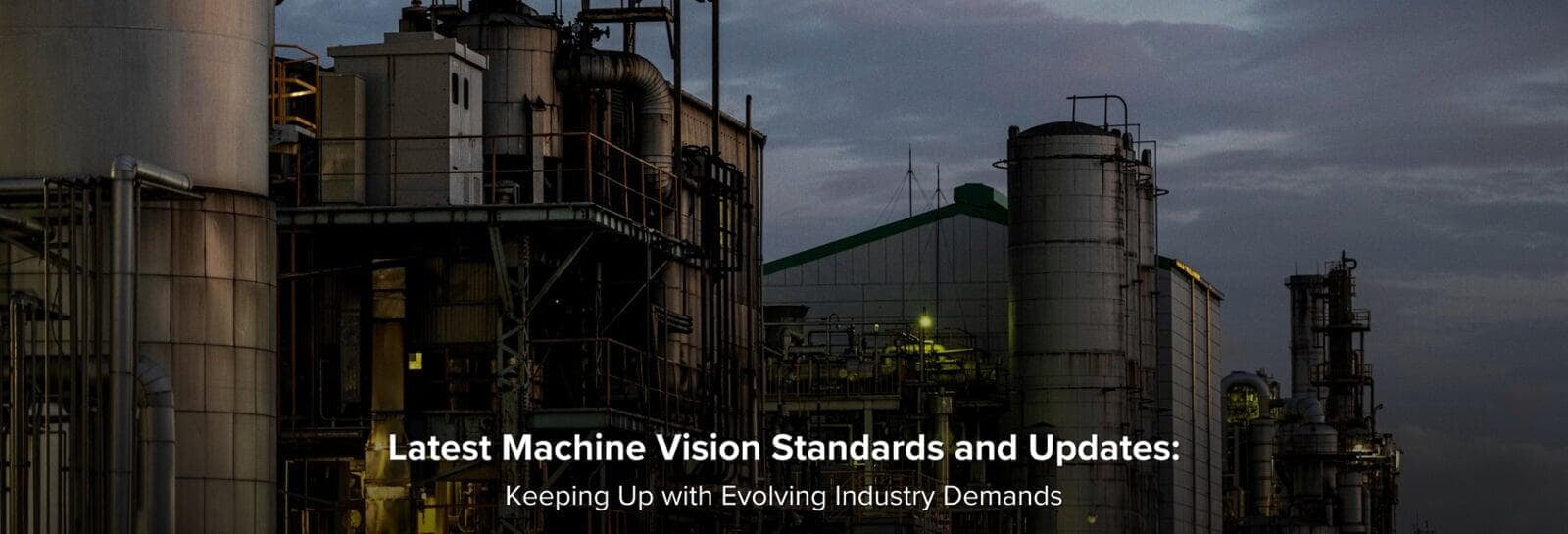
What Are Machine Vision Standards?
Why Standards Matter:
- Interoperability: Ensures machine vision systems can operate across platforms without compatibility issues.
- Performance: Establishes benchmarks for image quality, processing speeds, and accuracy, critical for high-speed manufacturing processes.
- Compliance: Many industries require machine vision systems to adhere to specific regulatory standards for safety, environmental impact, and accuracy.
Example: In the automotive sector, machine vision systems must comply with ISO/TS 16949 standards to ensure precision and reliability in inspecting critical vehicle components like airbags, engines, and electronic systems.
The Latest Machine Vision Standards and Updates
Several key organizations and standards bodies oversee the development of machine vision standards, including the Automated Imaging Association (AIA), the European Machine Vision Association (EMVA), and the Japan Industrial Imaging Association (JIIA).
Here are the latest updates from these bodies:
GenICam 3.0
The Generic Interface for Cameras (GenICam) standard defines the interaction between machine vision cameras and software. The latest version, GenICam 3.0, introduces several improvements aimed at simplifying camera integration, especially in high-speed applications.
Main Update: GenICam 3.0 improves camera communication speeds and reduces latency, making it ideal for real-time applications like robotic inspection and autonomous vehicles.
Impact: This update allows manufacturers to achieve faster image acquisition and processing, which is critical for industries like pharmaceuticals, food processing, and electronics, where speed and accuracy are paramount.
A report from the International Society for Optics and Photonics (SPIE) suggests that GenICam 3.0 can reduce camera response times by up to 15%, improving overall system efficiency in real-time automation applications.
USB3 Vision 2.0
USB3 Vision is another widely adopted standard for machine vision systems. The latest USB3 Vision 2.0 update introduces higher bandwidth capabilities, enabling faster data transmission from cameras to processing units.
Main Update: USB3 Vision 2.0 supports data transfer rates of up to 5 Gbps, making it suitable for high-resolution image processing in complex industrial environments.
Impact: Manufacturers using high-resolution cameras for detailed inspections—such as detecting small textile defects or inspecting printed circuit boards—can process images faster without sacrificing quality.
A survey by Vision Systems Design indicates that companies implementing USB3 Vision 2.0 have seen a 20-30% improvement in data transfer speeds compared to earlier USB versions.
CoaXPress 2.1
The CoaXPress (CXP) standard is designed for high-speed image and video transmission over coaxial cables. CoaXPress 2.1 enhanced data transmission rates while maintaining backward compatibility with older systems.
Main Update: CoaXPress 2.1 supports data rates of up to 12.5 Gbps per cable, enabling ultra-fast communication between cameras and vision systems.
Impact: This update is particularly relevant for high-speed applications like 3D imaging and real-time defect detection in aerospace and semiconductor manufacturing industries, where high bandwidth is crucial.
According to data from Automation World, companies using CoaXPress 2.1 have experienced a 30% increase in inspection speeds, thanks to the faster data rates and enhanced bandwidth capabilities.
Advancements in Imaging Standards
EMVA 1288 Update
The EMVA 1288 standard governs the performance characterization of image sensors and cameras. The latest update enhances guidelines for measuring dynamic range, sensitivity, and noise levels in machine vision cameras.
Main Update: The update introduces more stringent performance criteria for camera manufacturers, ensuring greater consistency in image quality across different camera models.
Impact: This is particularly beneficial for industries like pharmaceuticals and medical device manufacturing, where even the smallest image imperfections can lead to errors in quality control.
According to an EMVA study, the new EMVA 1288 standard reduces variability in sensor performance by up to 25%, leading to more reliable inspection processes in medical and pharmaceutical manufacturing.
Lighting Standards for Machine Vision
Lighting plays a critical role in machine vision applications. The latest lighting standards aim to improve energy efficiency and uniformity in illumination.
Main Update: The new lighting guidelines recommend using LED lighting systems with adjustable intensity and wavelength control, which allows for optimal lighting conditions for different materials and surfaces.
Impact: These lighting advancements enable machine vision systems to capture clearer images with minimal glare or shadowing, leading to more accurate inspections.
A report from LEDinside found that using standardized LED lighting in machine vision systems improved defect detection accuracy by 15% while reducing energy consumption by 10%.
AI and Machine Learning Integration
AI in Machine Vision: The Role of Standards
AI-enabled machine vision systems transform inspections, allowing for greater accuracy and faster decision-making. However, the need for standardized AI models and data-sharing protocols poses challenges for adoption.
Latest Update: Industry groups, such as the International Electrotechnical Commission (IEC), are working to develop AI-specific standards for machine vision applications. These standards focus on ensuring the interoperability of AI models and the secure sharing of data across systems.
Impact: AI-driven inspection systems are already being used in industries like food and beverage, where real-time defect detection can significantly reduce waste and improve product quality.
Research from MarketsandMarkets indicates that manufacturers integrating AI into their machine vision systems have seen up to a 25% reduction in defect rates, leading to significant improvements in quality control.
Cybersecurity Standards for Machine Vision
Cyber Security Protocols in Machine Vision
Main Update: The latest cybersecurity protocols focus on encrypting data transmitted between cameras and processing systems and securing IoT devices in machine vision networks.
Impact: Ensuring the security of machine vision systems is particularly important in sectors such as defense: Staying Ahead with Machine Vision Standards, aerospace, and critical infrastructure, where data breaches can have severe consequences.
A Gartner report found that manufacturers adopting the latest cybersecurity protocols for machine vision systems reduced the risk of cyber attacks by 40%, protecting data and operations.