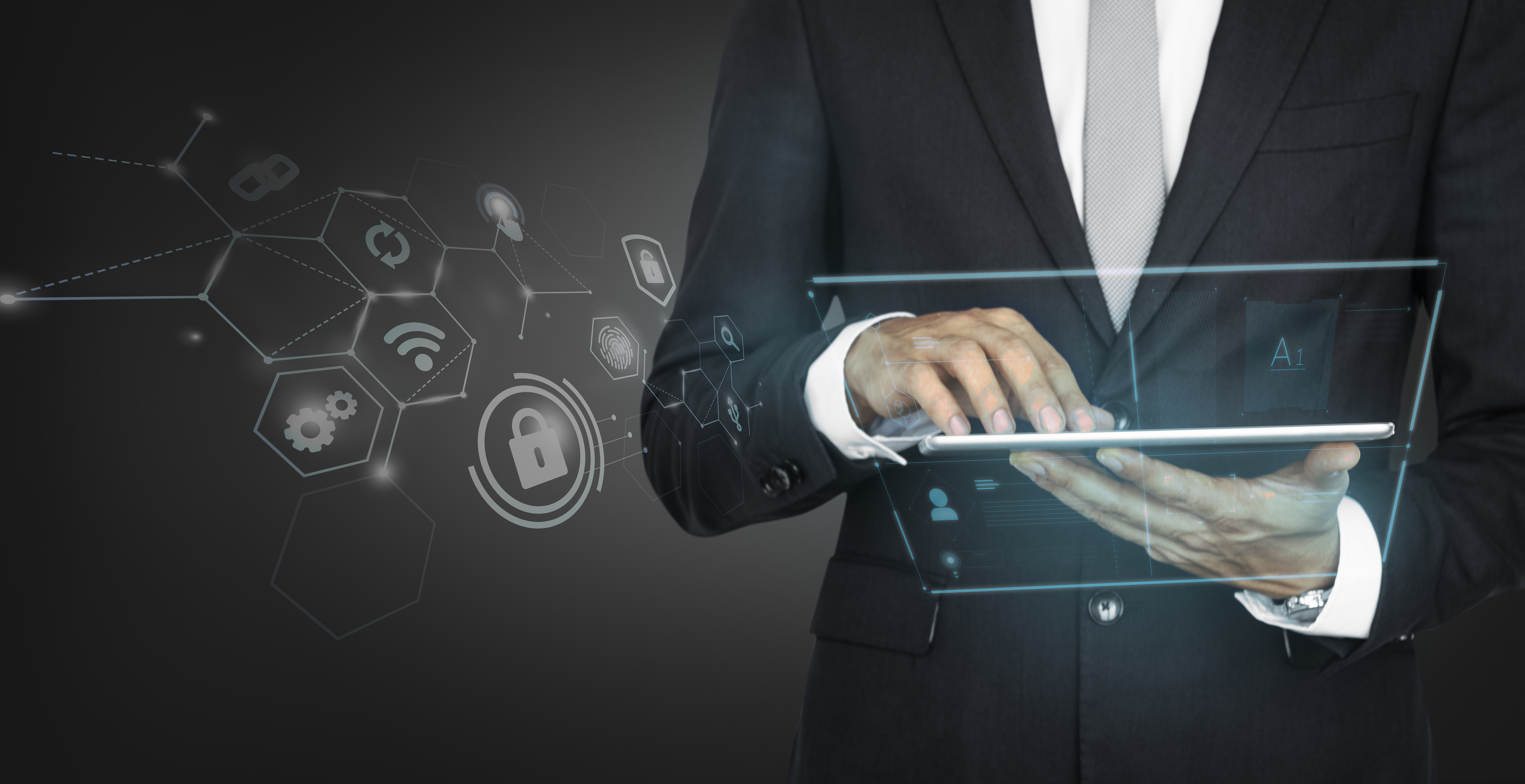
Human errors in manufacturing may result in defective products and material wastage. Defects may result in wastage at different times during the manufacturing process. A minor defect may require discarding the material or being repurposed, which increases costs and production time.
Small defects if unchecked can escalate into larger defects, which can significantly impact the manufacturing process and costs. The need for reducing wastage to zero has been an instrumental factor driving the demand for quality inspection systems.
AI in manufacturing uses machine vision technology to detect defects and reduce wastage to zero. These use advanced technologies, such as high-end cameras, deep learning, and data analytics to detect defects with almost 100 per cent accuracy.
How AI can be used for
zero wastage?
Advanced AI-enabled visual inspection systems can be trained for identifying any defects in the manufacturing process. These are intelligent systems that learn from the data. Manufacturers can train these systems to identify defects during the production process. The system will automatically send alerts in case of any manufacturing anomaly, which allows the people to rectify the defect before it affects other products or wastes additional materials.
Manufacturers can use a reliable AI-enabled defect detection system to implement automated checks and improve the quality control process, which ensures products adhere to the stringent norms of the regulatory bodies.
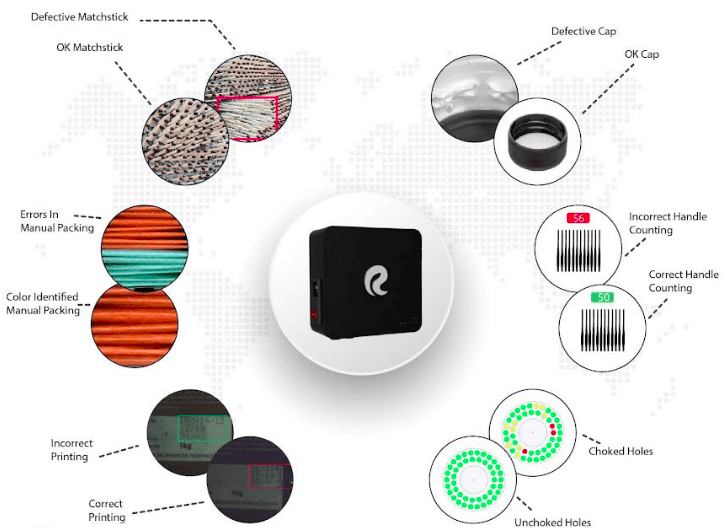
Factors affecting ROI for manufacturing companies
Automated inspection systems may require an initial capital expenditure, but can deliver higher ROI in the long term. Here are some factors you should consider while deciding on whether to invest in an automated system to reduce wastage or not:
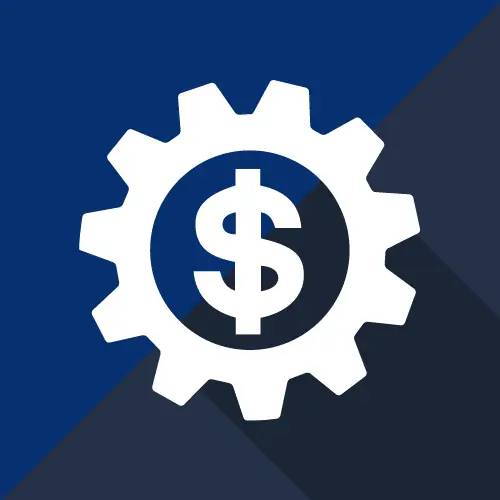
Cost of the machine vision system
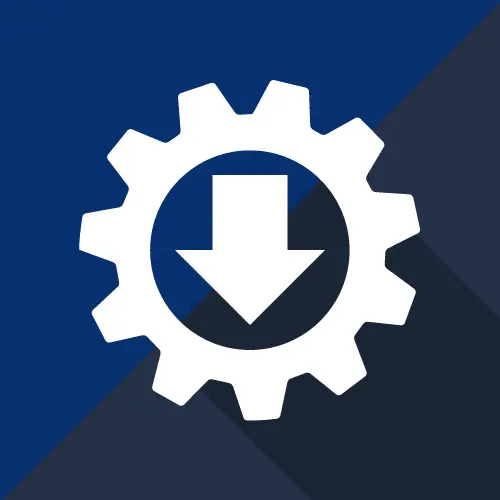
Downtime of the production lines
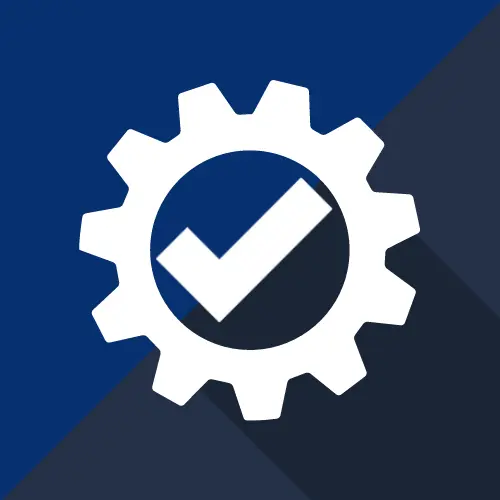
Acceptable product quality based on customers’ requirements
While making an investment decisions, you must also understand the benefits and the costs of deploying automated AI-enabled machine vision systems. Some of the advantages of these systems include:
Deploying a machine vision system entails certain expenses, such as the actual cost of the system, its maintenance, installation and integration, and training personnel to use the system. Initially, these costs may seem significant; however, these advanced systems provide several financial benefits like improved efficiency, increased products, lesser wastage, accuracy, and many more.
Additionally, other intangible benefits like brand reputation and eliminating the potential law suits further increases the profitability for the manufacturers. Moreover, as customers and regulatory authorities move towards sustainability, investing in machine vision systems to improve manufacturing efficiency and reducing wastage is sensible. AI-enabled vision technology delivers an attractive ROI and enhances sustainability and investing in this system is recommended to all manufacturers.