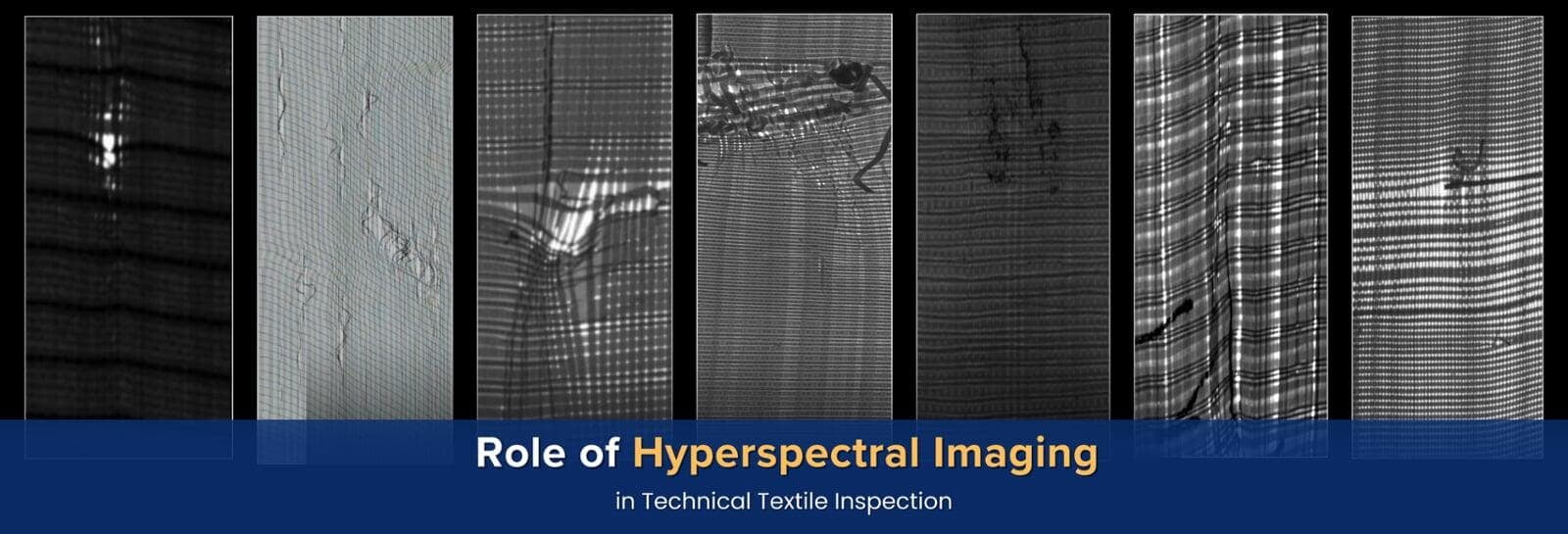
Key Features
- Hyper-spectral imaging (HSI) captures a vast spectrum of light across hundreds of bands, providing detailed chemical and physical profiles of technical textiles.
- It helps detect subtle variations in materials, like weave patterns, fiber composition, or chemical treatments, that traditional methods may miss.
- Robro Systems' Kiara Web Inspection System (KWIS) integrates HSI for real-time analysis, identifying defects directly on the production line.
- KWIS ensures uniformity and quality in materials like conductive FIBC bag fabrics by detecting coating inconsistencies early.
- HSI allows non-destructive testing and offers data-driven insights, enabling manufacturers to optimize processes and predict defects.
- With AI integration, KWIS learns from past defect patterns, improving detection accuracy.
- Adopting HSI has led to cost savings, reduced waste, and enhanced product quality for manufacturers using Robro Systems' solutions.
- The global hyper-spectral imaging market is expected to grow significantly, driven by its advantages in industrial quality control.
Understanding Hyper-spectral Imaging
Unlike conventional imaging systems that capture data in three spectral bands (red, green, and blue), hyper-spectral imaging captures a vast spectrum of light across hundreds of bands. This capability allows HSI to detect subtle differences in invisible materials to the naked eye or standard vision systems. By analyzing how materials absorb, reflect, or emit light, hyper-spectral imaging can provide a chemical and physical profile of a fabric.
For example, in technical textiles, variations in weave patterns, fiber composition, or chemical treatments can be identified with remarkable precision using HSI. This is particularly valuable for manufacturers like us, who must ensure uniformity in materials such as conductive textiles or flame-resistant fabrics.
Industry Challenges in Quality Control
The technical textile industry faces several challenges in maintaining quality standards:
1) Diverse Material Properties
Technical textiles often feature complex fibers, coatings, and treatment blends. Traditional inspection methods, like manual checks or RGB imaging, struggle to detect subtle variations in such materials.
2) High-Speed Production
In fast-paced production lines, defects like uneven coatings, fiber misalignment, or minor surface imperfections can go unnoticed until the final quality check. By that time, significant waste may have already accumulated.
3) Increasing Customer Demands
With end-users expecting defect-free and high-performing products, manufacturers must invest in advanced quality control systems that meet stringent requirements without slowing down production.
Robro Systems' Approach: Bringing Hyper-spectral Imaging to the Forefront
Robro Systems, a leader in industrial automation and machine vision solutions, has taken a forward-thinking approach to these challenges by integrating hyper-spectral imaging into their inspection systems. The Kiara Web Inspection System (KWIS) is a prime example of this technology's capabilities. It's designed to address the unique needs of technical textile manufacturers, ensuring that defects are caught before they impact the final product.
1) Real-Time Analysis for Immediate Action
One of KWIS's standout features is its ability to analyse materials in real time. Unlike conventional inspection methods that rely on sampling and post-production checks, KWIS captures and processes hyper-spectral data directly on the production line. This allows manufacturers to identify variations in fabric composition, coating consistency, or structural integrity instantly.
For example, during the production of conductive FIBC (Flexible Intermediate Bulk Container) bag fabrics, KWIS detected inconsistencies in the conductive coating's distribution across the fabric surface. This early detection helped prevent a significant batch of materials from being shipped with defects, saving both time and costs associated with reworking or scrapping materials.
2) Enhanced Defect Detection Accuracy
The precision of hyper-spectral imaging extends beyond surface-level inspection. KWIS can detect defects not visible through traditional vision systems, such as minor color deviations, differences in fiber density, or the presence of foreign materials. These subtle differences can have a major impact on product performance for technical textiles like tire cord fabrics and conveyor belt fabrics.
In a recent deployment, Robro Systems used KWIS to inspect a batch of tire cord fabric for a leading automotive supplier. The system successfully identified variations in fabric density that could have compromised the cords' strength. With KWIS, the manufacturer could adjust their production process immediately, ensuring that only top-quality materials reached their customers.
Technical Advantages of Hyper-spectral Imaging in Textile Inspection
1) Detailed Spectral Information
Hyperspectral imaging can differentiate between materials that look identical in the visible spectrum but have different chemical compositions. This capability is crucial for detecting chemical impurities, incorrect dye concentrations, or improper treatments.
2) Non-Destructive Testing
HSI enables non-destructive testing, meaning manufacturers can perform in-depth inspections without damaging the fabric. This is particularly important for high-value technical textiles, where minimizing waste is a priority.
3) Data-Driven Insights
The large volume of data generated by hyperspectral imaging allows for advanced analytics, helping manufacturers identify trends, predict potential defects, and optimize production processes.
4) Integration with AI
Robro Systems has integrated AI algorithms with HSI technology in KWIS, allowing the system to learn from past defect patterns and improve its detection accuracy over time. This continuous learning process ensures that the inspection system becomes more effective the longer it operates.
The Real Impact: Cost Savings and Improved Quality
The practical benefits of implementing hyper-spectral imaging in textile inspection are significant. According to a report by MarketsandMarkets, the global hyper-spectral imaging systems market is projected to grow from USD 13.9 billion in 2021 to USD 25.2 billion by 2026, driven by its adoption in industrial quality control (source). For manufacturers like us, this technology has translated into measurable cost savings, improved product quality, and stronger customer relationships.
With Robro Systems' KWIS, we've seen a marked reduction in waste and rework costs. Defects that go unnoticed until post-production are detected in real-time, allowing us to address issues before they impact a full production run. This means less downtime, fewer rejected batches, and a more efficient production process.
A Future-Ready Solution for the Textile Industry
Conclusion
At a time when industry standards are constantly evolving and customer expectations are higher than ever, embracing innovative technologies like hyperspectral imaging is essential. With Robro Systems' advanced solutions like KWIS, we've maintained a competitive edge while delivering consistent, high-quality products. As a manufacturer, the ability to detect and correct defects before they become costly problems is invaluable—and it's clear that hyperspectral imaging is here to stay.
By investing in such future-ready inspection solutions, we are not only protecting our bottom line but also reinforcing our commitment to quality—a promise that our customers can count on.