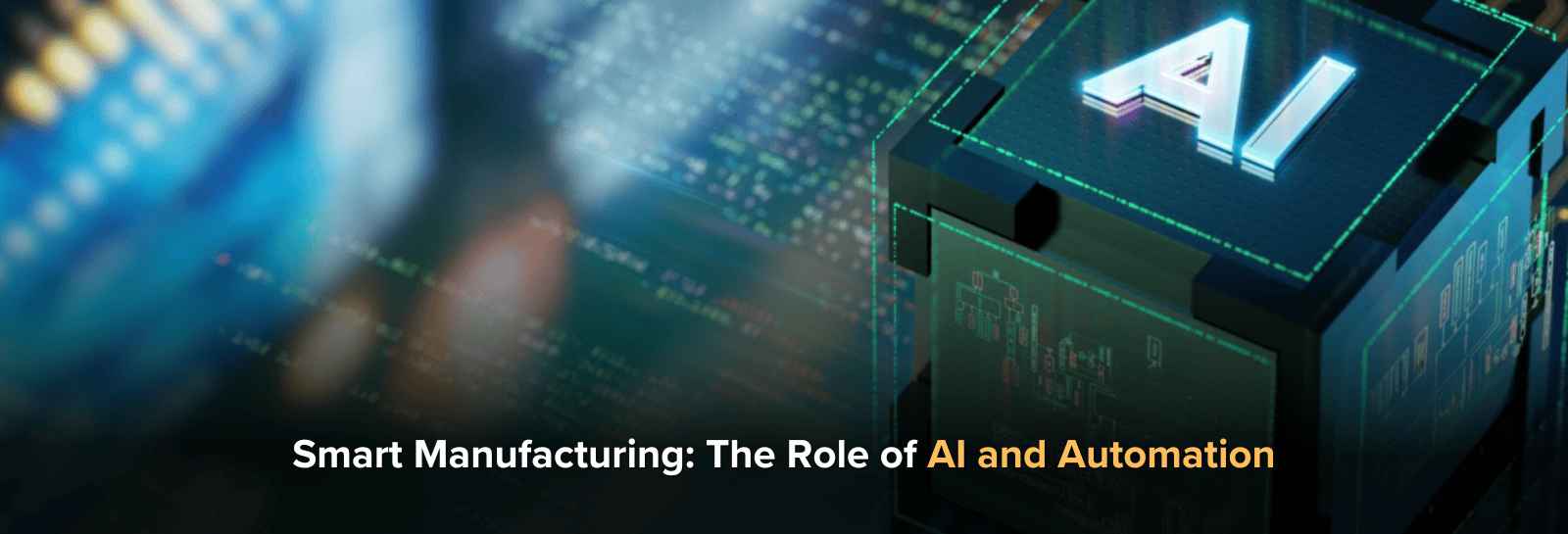
The Evolution of Smart Manufacturing
1) From Traditional to Smart Factories
2) The Role of Industry 4.0
Industry 4.0 represents the convergence of digital technologies with industrial processes, leading to intelligent and interconnected manufacturing ecosystems. AI-driven analytics, cloud computing, IoT sensors, and cyber-physical systems work together to create adaptive and self-optimizing production environments that respond dynamically to changing demands. Companies leveraging Industry 4.0 can benefit from increased visibility into production lines, enhanced process optimization, and reduced operational risks. This revolution sets new standards for productivity, cost reduction, and product customization at scale.
Key Technologies Driving AI and Automation in Smart Manufacturing
Benefits of AI and Automation in Smart Manufacturing
1) Enhanced Productivity and Efficiency- AI-driven automation accelerates production cycles, minimizes downtime, and streamlines manufacturing processes, leading to higher output and reduced operational costs. Automated systems can work 24/7 without fatigue, ensuring continuous production and consistent quality. Real-time data analytics further optimize workflow efficiency by identifying inefficiencies and recommending adjustments, resulting in leaner operations and faster turnaround times.
2) Improved Quality Control—Machine vision systems equipped with AI analyze products in real-time, detecting defects with an accuracy rate exceeding 99.99%. Automated quality control ensures that only defect-free products reach the market, reducing waste and improving customer satisfaction. These systems use advanced imaging and deep learning algorithms to detect even the slightest deviations from quality standards, ensuring that every product meets regulatory and consumer expectations.
3) Predictive Maintenance and Reduced Downtime- AI-powered predictive maintenance algorithms analyze equipment performance, predicting failures before they occur. This proactive approach reduces unplanned downtime, extends machine lifespan, and minimizes maintenance costs. Traditional maintenance methods rely on fixed schedules or reactive repairs, but AI-driven systems continuously assess machine conditions, scheduling maintenance only when necessary, thereby reducing costs and improving asset longevity.
4) Energy and Resource Optimization- Smart manufacturing reduces energy consumption by optimizing machine performance and production schedules. AI-driven energy management systems analyze usage patterns, adjusting power consumption to minimize waste and enhance sustainability. Smart grids and AI-integrated control systems improve efficiency by dynamically allocating resources based on demand, leading to lower operational costs and reduced environmental impact.
5) Supply Chain Optimization- AI-driven analytics improve supply chain management by predicting demand fluctuations, optimizing inventory levels, and reducing lead times. Logistics automation enhances warehouse operations, reducing errors in order fulfillment and improving delivery speed. Predictive analytics enable manufacturers to anticipate supply chain disruptions, ensuring resilient and agile operations that adapt quickly to market shifts.
6) Workplace Safety and Human-Machine Collaboration—Smart manufacturing reduces workplace accidents and enhances worker safety by automating hazardous tasks and deploying collaborative robots. AI-powered monitoring systems detect potential safety risks and provide real-time alerts to prevent accidents. AI-driven ergonomics analysis can also improve workplace design, minimizing strain-related injuries and improving overall worker well-being.