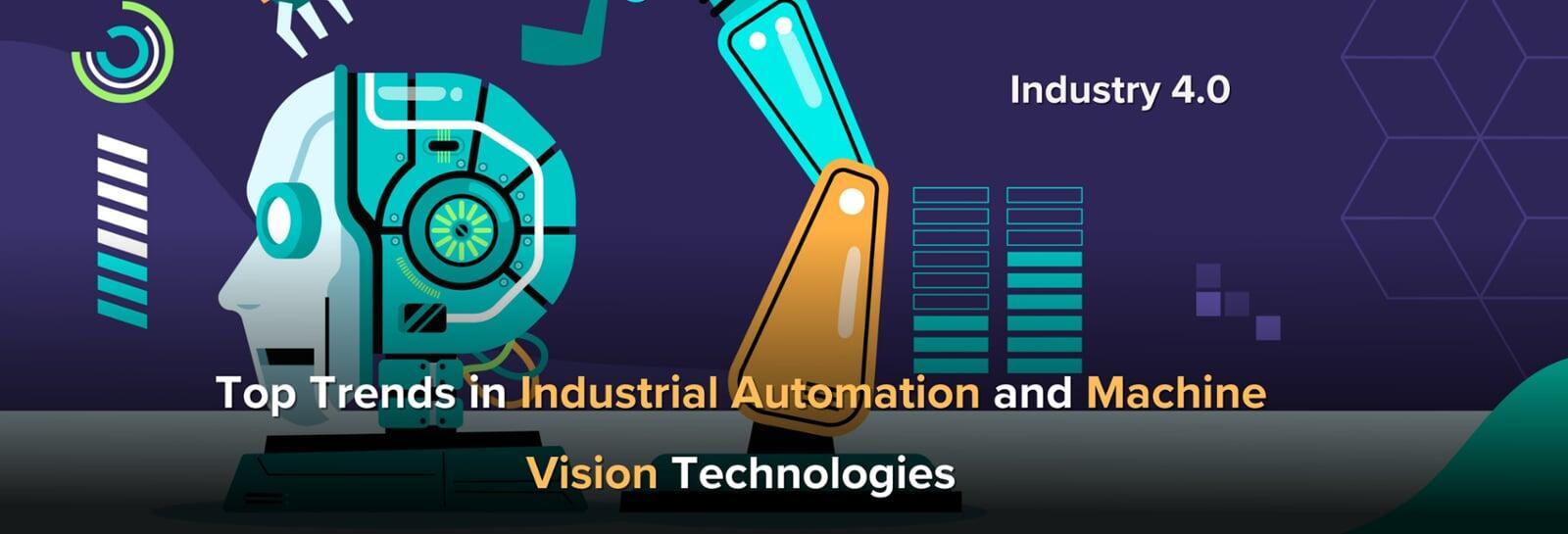
What Defines Industrial Automation and Machine Vision in 2025?
Industrial automation integrates robotics, artificial intelligence (AI), and IoT to streamline production processes, enhance accuracy, and minimize waste. Machine vision, a subset of this ecosystem, allows systems to "see" and interpret visual data, enabling real-time defect detection and adaptive manufacturing. In 2025, these technologies are characterized by:
Advanced AI Integration: Deep learning algorithms capable of predictive defect analysis.
Real-Time Analytics: Edge computing ensures immediate insights, empowering decision-makers.
Customization at Scale: Solutions tailored for specific industries like technical textiles, ensuring relevance and precision.
Machine vision enables manufacturers to address material-specific challenges in technical textiles such as tire cord fabrics and FIBCs, ensuring consistent quality and reliability.
How These Technologies Work: Trends for 2025
Trend 1: AI-Powered Vision Systems
Artificial intelligence remains the cornerstone of modern machine vision. By leveraging deep learning models, AI-powered systems in 2025:
Detect even the most minor defects with unparalleled accuracy.
Adapt to dynamic production environments in real time.
Provide actionable insights for process optimization.
For example, tire cord fabric production benefits immensely from convolutional neural networks (CNNs), which detect thread misalignment and coating inconsistencies, reducing waste and boosting product reliability.
Trend 2: Edge Computing for Real-Time Processing
- Edge-enabled systems in conveyor belt fabric production detect weak spots instantly without halting operations.
- Localized processing reduces downtime and enhances decision-making.
Trend 3: Collaborative Robots (Cobots)
Cobots are reshaping human-machine collaboration, offering flexibility and efficiency. Equipped with machine vision:
Cobots assist in defect identification and marking.
They reduce the strain on human workers by automating repetitive tasks.
They improve precision in cutting, stitching, and assembly processes.
Cobots ensure consistency and adaptability in geotextile production, particularly in high-speed operations.
Trend 4: Multi-Spectral and Hyper-spectral Imaging
- Detecting dye inconsistencies in geotextiles.
- Identifying invisible defects or contaminants in FIBC fabrics.
Trend 5: IoT-Enabled Smart Manufacturing
- Monitor real-time production metrics like tension and temperature.
- Alert operators about potential issues before they escalate.
Trend 6: Automation in Quality Assurance
- Perform 100% inspections at every stage of production.
- Detect defects in nonwovens, coated fabrics, and geotextiles with unmatched precision.
Overcoming Challenges in Adopting Advanced Technologies
Technical Innovations in Machine Vision
1) Enhanced AI Algorithms
AI in 2025 utilizes advanced neural networks that:
Predict defects before they occur.
Optimize real-time production parameters, minimizing disruptions.
Generative adversarial networks (GANs) simulate complex production scenarios, equipping manufacturers with insights for proactive decision-making.
2) Advanced Imaging Technologies
Technologies like 3D and thermal imaging enhance detection capabilities. Applications include:
Inspecting structural integrity in geotextiles.
Ensuring uniform coatings in conveyor belt fabrics.
3) Robotics with Integrated Vision
Modern robots combine advanced vision systems with dexterity, excelling in:
Precision cutting and assembly.
Automated inspections with minimal errors.
This innovation drives operational efficiency and cost savings.
Real-World Applications in Technical Textiles
1) FIBC and Conductive Fabrics
- Inspect conductive patterns for consistency.
- Detect defects like thread misalignment and incomplete stitching.
2) Conveyor Belt Fabrics
3) Geotextiles
- Ensuring tear resistance and permeability compliance.
- Identifying dye and pattern inconsistencies for high-performance applications.
4) Tire Cord Fabrics
- Thread alignment to maintain structural integrity.
- Coating uniformity to meet industry-specific standards.