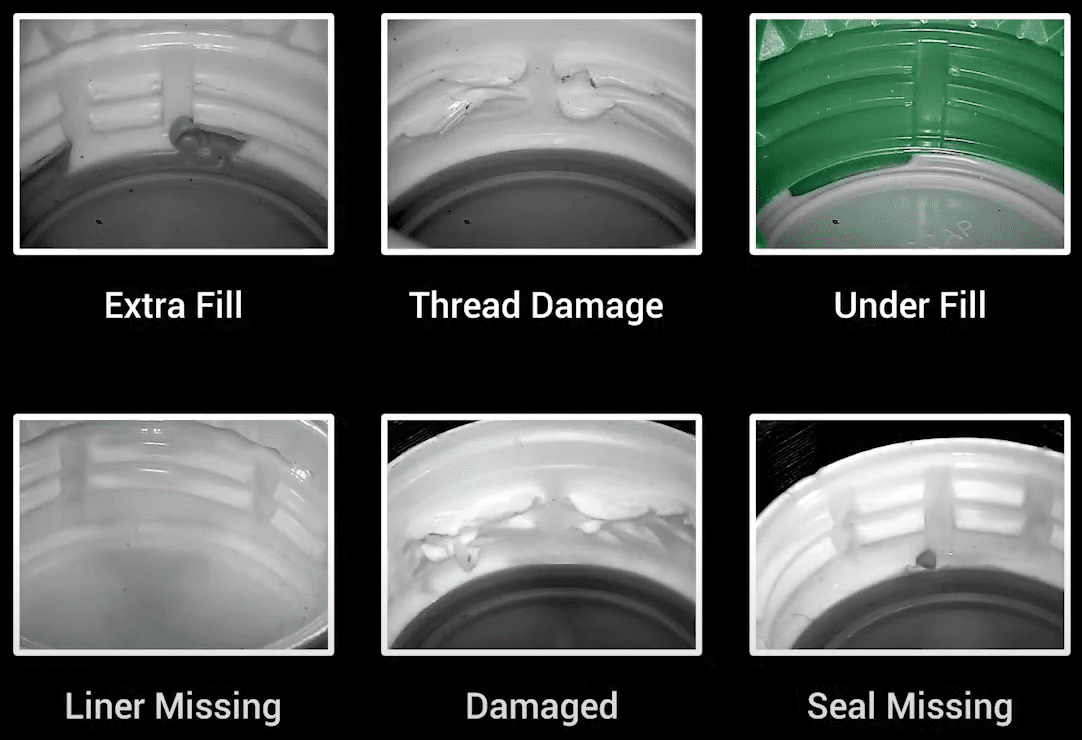
Identify. Sort.
Vision systems powered by AI algorithms are quick to identify the correct type of part or defect in a given product by scanning them at high speeds. It is often followed by an action step that aims to sort items into desired categories.
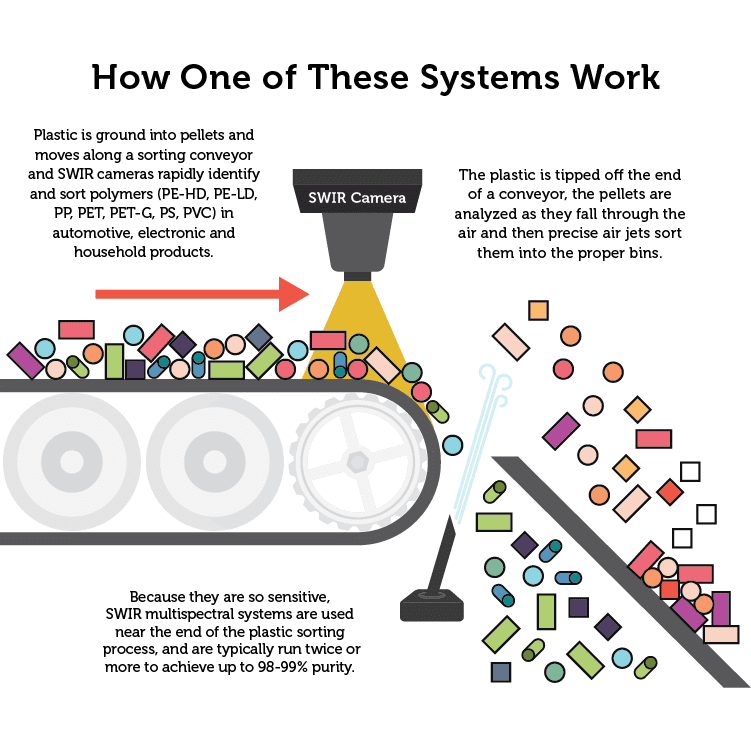
We have just the solution for your Sorting needs!
We have just the solution for your Sorting needs!
An estimated 30% of Industrial Production time goes into the final inspection or product sorting phase of production. It employs over 40% of the workforce at times. Even then, errors occur due to human oversight or plain complexity of the sorting process. This leads to wasted efforts and inaccurate product sorting that is not able to demand the level of premium in the market that it deserves.
In the Pharma industry, broken, damaged and cracked pills need to be identified and sorted accordingly as per color or type of defect.
Waste Sorting is an essential requirement of cities to sort and classify different wastes to aid the process of Recycling and dumping.
Vision based sorting helps to classify types of defects found in bottle caps, which eliminates the manual seggregati
Depending on the type of defect, the operation required to refurbish a cap is decided. Hence, it is critical that in a single lot, same type of defects are there, so that machines and operators can efficiently move to fix them.
Sorting diamonds based on size is critical when bagging diamonds before sending them for placement on jewelry.
Selected Case Study
View this case study of how cap sorting helped a business-owner automate his operations.
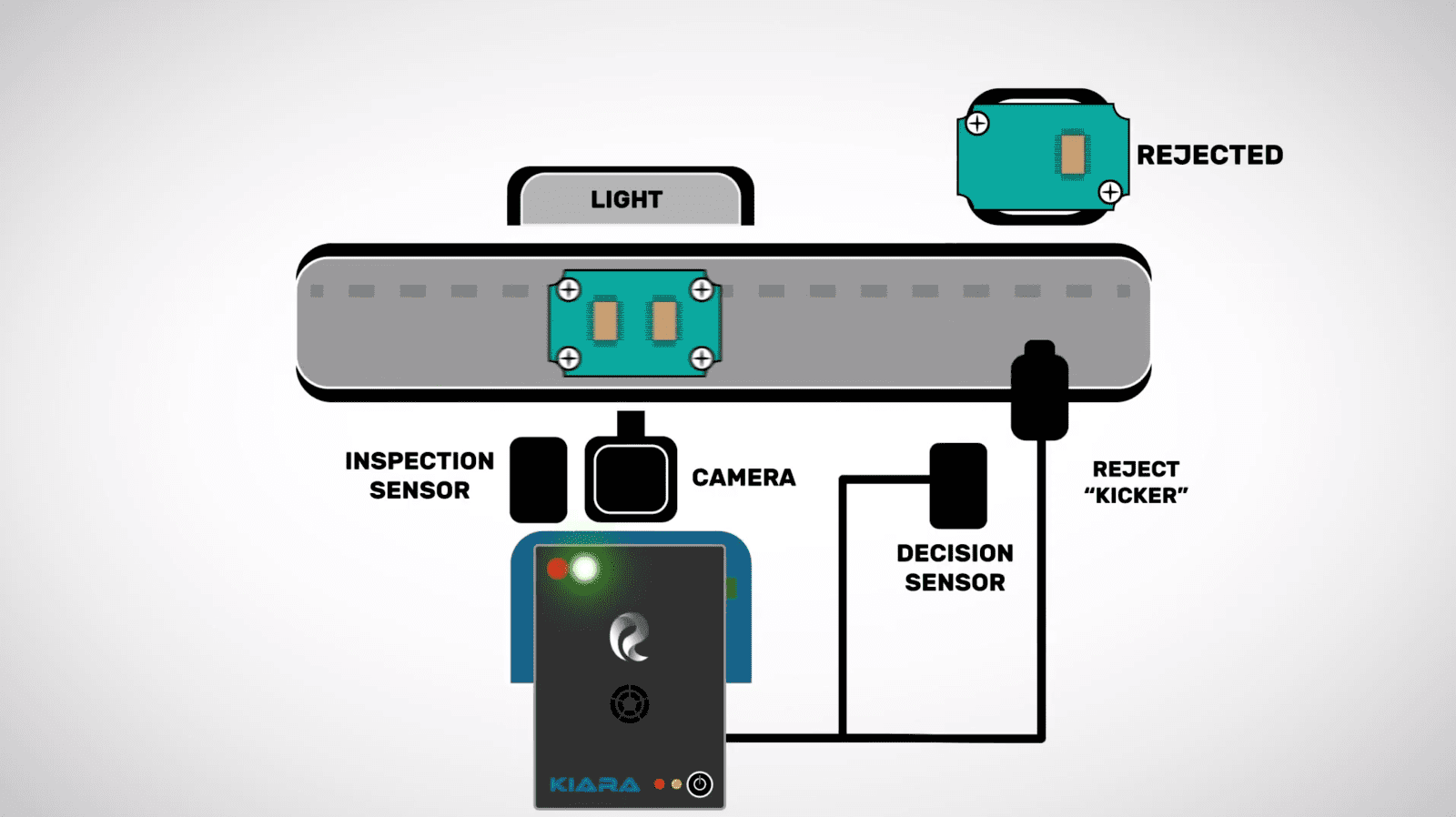
How it works!
Items are marked as different categories that need to be sorted separately. A human-in-the-loop AI training methodology works best. The continuous learning system becomes smarter as more and more defects are fed into it.
This trained model is fed into the Kiara Vision Platform™ which connects with a camera installed on the line. Upon the part coming in front of the camera, a sensor signals the camera to capture an image. The image is compared against pre-learnt models and a category is decided based on the same. An actuator is connected to the Kiara Vision Platform™ that performs the desired sorting operation.