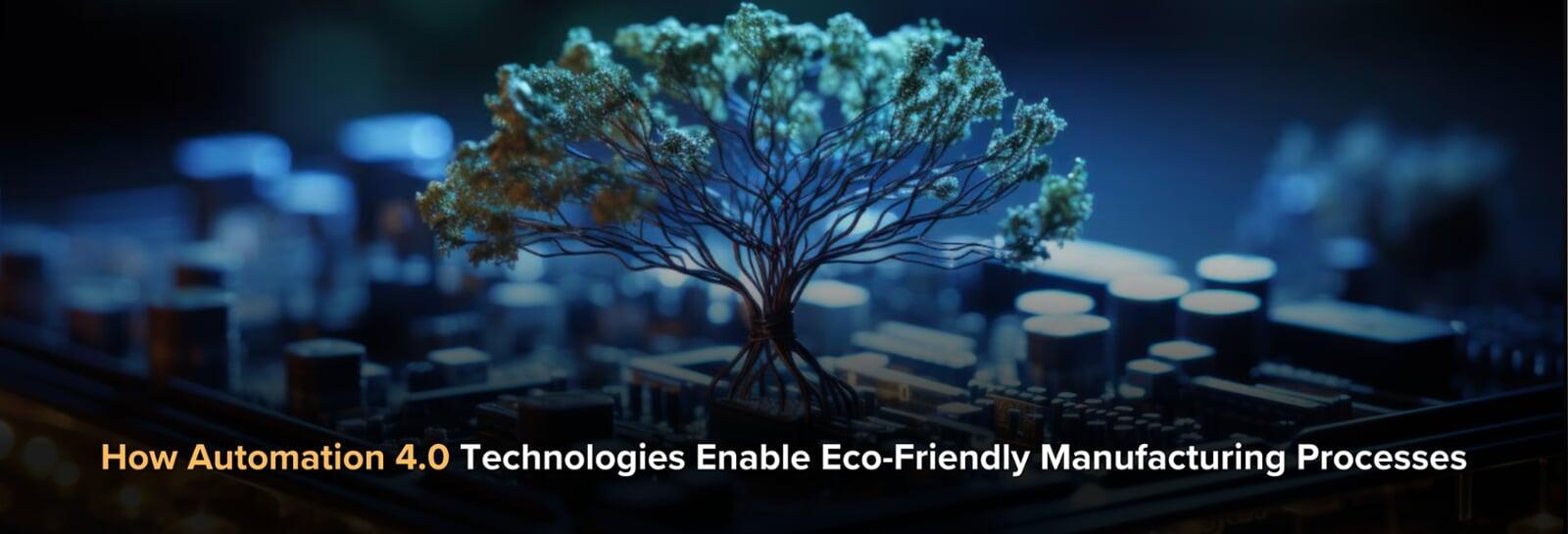
In the modern era, sustainability is no longer an option but a necessity. Manufacturing industries, particularly in technical textiles, are under increasing pressure to adopt environmentally friendly processes to align with global sustainability goals. With the advent of Automation 4.0, also known as Industry 4.0, technologies, industries now have access to tools that enhance efficiency and reduce environmental footprints. Automation 4.0—a combination of intelligent machines, advanced sensors, data analytics, and artificial intelligence—can revolutionize manufacturing by promoting eco-friendly practices.
Technical textile industries, which produce specialized fabrics like conveyor belts, tire cords, and geotextiles, are increasingly leveraging automation 4.0 technologies to minimize waste, optimize resource usage, and achieve higher precision in production. This blog delves into how Automation 4.0 technologies enable eco-friendly manufacturing processes, highlighting their benefits, challenges, technical innovations, and real-world applications.
What is Automation 4.0?
What is Automation 4.0?
Automation 4.0, the Fourth Industrial Revolution, refers to integrating advanced technologies into manufacturing systems to create more innovative, efficient, and sustainable operations. These technologies include the Internet of Things (IoT), Artificial Intelligence (AI), Machine Learning (ML), robotics, cloud computing, and big data analytics. Automation 4.0 ensures precision in technical textile manufacturing, reduces human error, and enhances overall productivity while supporting eco-friendly initiatives.
Automation 4.0 facilitates real-time monitoring, data-driven decision-making, and predictive maintenance, ensuring efficient resource utilization. For example, when inspecting technical textiles like FIBC fabrics or coated materials, automated systems with AI-driven defect detection minimize waste by ensuring that only high-quality products proceed to the next production stage.
How Automation 4.0 Technologies Enable Eco-Friendly Manufacturing
How Automation 4.0 Technologies Enable Eco-Friendly Manufacturing
1) Waste Reduction through Smart Inspection Systems
1) Waste Reduction through Smart Inspection Systems
Traditional inspection processes waste significantly due to human error or delayed defect detection. Automation 4.0 introduces innovative inspection systems that use AI and machine vision to identify real-time defects. For example, Kiara Web Inspection Systems for Technical Textiles by Robro Systems utilizes high-precision cameras and AI algorithms to detect even minute defects in fabrics, ensuring minimal wastage.
By catching defects early, manufacturers can reduce the number of rejected products, saving materials and energy. For instance, in the production of tire cord fabrics, real-time defect detection ensures that defective sections are addressed immediately, preventing the wastage of entire rolls of fabric.
2) Energy Optimization with IoT and Smart Sensors
2) Energy Optimization with IoT and Smart Sensors
Energy consumption is a major contributor to the environmental impact of manufacturing processes. Automation 4.0 technologies like IoT-enabled energy management systems help monitor and optimize energy usage. Smart sensors embedded in machinery track energy consumption patterns and identify inefficiencies.
For example, IoT systems can adjust machine operations based on real-time data in conveyor belt fabric production, ensuring that energy is used only when necessary. This reduces energy bills and lowers greenhouse gas emissions.
3) Resource Efficiency through Data Analytics
3) Resource Efficiency through Data Analytics
Data analytics plays a crucial role in optimizing resource usage. Advanced analytics tools collect and process data from various stages of the manufacturing process to identify areas where resources can be used more efficiently.
For example, data analytics can help optimize raw materials like polypropylene and polyester in geotextile manufacturing by providing insights into material behavior during production. This ensures that resources are used effectively, reducing material wastage.
4) Predictive Maintenance for Reduced Downtime and Waste
4) Predictive Maintenance for Reduced Downtime and Waste
Unexpected equipment failures often lead to downtime, wasted materials, and increased energy consumption. Predictive maintenance, powered by AI and IoT, addresses this challenge by predicting when a machine will fail and scheduling maintenance accordingly.
In the technical textile industry, predictive maintenance ensures that machines like looms and coating units operate at peak efficiency, minimizing energy wastage and reducing the environmental impact of unplanned repairs.
5) Automation in Recycling and Reuse Processes
5) Automation in Recycling and Reuse Processes
Automation 4.0 technologies also significantly promote recycling and reuse in manufacturing. For instance, robotic systems can sort and separate recyclable materials more efficiently than manual processes. In technical textile manufacturing, automated systems can reclaim usable fibers from defective products, reducing the need for virgin raw materials.
Overcoming Challenges in Adopting Automation 4.0
Overcoming Challenges in Adopting Automation 4.0
1) High Initial Investment- Implementing Automation 4.0 technologies requires a significant upfront investment in equipment, software, and training. However, the long-term benefits, including cost savings and sustainability, outweigh these initial costs. Companies can explore government grants and subsidies to offset expenses.
2) Integration with Existing Systems- Many manufacturers face challenges in integrating new automation technologies with legacy systems. Modular solutions and scalable technologies, such as Robro Systems’ inspection systems, are designed for seamless integration, ensuring manufacturers can adopt Automation 4.0 without overhauling their entire setup.
3) Skill Gaps in the Workforce- The adoption of Automation 4.0 requires a workforce skilled in handling advanced technologies. Companies must invest in employee training and development to bridge this gap and ensure smooth implementation and operation.
4) Data Security Concerns- Data security has become a critical concern with the increasing use of IoT and cloud computing. Manufacturers must implement robust cybersecurity measures to protect sensitive information and ensure the integrity of their operations.
Benefits of Automation 4.0 in Eco-Friendly Manufacturing
Benefits of Automation 4.0 in Eco-Friendly Manufacturing
1) Enhanced Efficiency and Productivity- Automation 4.0 technologies streamline manufacturing processes, reducing production time and resource consumption. For example, automated inspection systems ensure faster defect detection, improving overall productivity.
2) Lower Carbon Footprint- By optimizing energy usage and reducing waste, Automation 4.0 significantly lowers the carbon footprint of manufacturing processes. This aligns with global efforts to combat climate change and promotes a positive brand image.
3) Improved Product Quality- Advanced inspection technologies ensure consistent product quality by detecting defects early. This reduces the number of defective products reaching the market, minimizing material waste and enhancing customer satisfaction.
4) Cost Savings- Although the initial investment in Automation 4.0 can be high, the long-term cost savings from reduced energy consumption, minimized waste, and improved efficiency make it worthwhile.
5) Regulatory Compliance- Automation 4.0 technologies help manufacturers comply with environmental regulations by promoting sustainable practices. This reduces the risk of penalties and enhances the company’s reputation as an environmentally responsible organization.
Technical Innovations Driving Eco-Friendly Manufacturing
Technical Innovations Driving Eco-Friendly Manufacturing
1) AI-Powered Defect Detection- AI-driven systems analyze visual data to detect defects with unparalleled accuracy. These systems adapt to fabric types and inspection criteria, ensuring high defect detection accuracy for technical textiles like conveyor belt fabrics and FIBCs.
2) IoT-Enabled Smart Factories- IoT devices enable real-time monitoring and control of manufacturing processes, ensuring optimal resource usage. Smart factories equipped with IoT technologies can adjust operations dynamically based on data insights, reducing energy consumption and waste.
3) Digital Twins- Digital twins create virtual replicas of physical manufacturing processes, allowing manufacturers to simulate and optimize operations before implementation. This reduces trial-and-error approaches, saving time and resources.
4) Advanced Robotics- Robotic systems automate repetitive tasks with high precision, reducing errors and material wastage. In technical textile manufacturing, robots can handle delicate fabrics without causing damage, ensuring efficient production.
5) Renewable Energy Integration- Automation 4.0 technologies facilitate the integration of renewable energy sources like solar and wind into manufacturing processes. For example, IoT systems can manage energy distribution, ensuring that renewable sources are utilized effectively.
Real-World Applications of Automation 4.0 in Technical Textiles
Real-World Applications of Automation 4.0 in Technical Textiles
1) Conveyor Belt Fabric Inspection- Automated inspection systems equipped with machine vision ensure precise defect detection in conveyor belt fabrics, reducing material wastage and enhancing durability.
2) Tire Cord Fabric Production- AI-powered systems optimize the alignment and coating of tire cord fabrics, ensuring consistent quality while minimizing resource consumption.
3) FIBC Fabric Inspection- Real-time defect detection systems for FIBC fabrics identify thread breaks and coating inconsistencies, ensuring compliance with safety standards and reducing waste.
4) Coated Geotextiles- Automation 4.0 technologies optimize coating processes for geotextiles, reducing material usage and ensuring uniformity in product quality.
5) Medical Textiles- In medical textile manufacturing, automated systems ensure precision in products like surgical gowns and masks, minimizing defects and waste.
Conclusion
Conclusion
Automation 4.0 technologies represent a transformative leap forward, particularly in driving sustainable manufacturing practices. Manufacturers can significantly reduce their carbon footprint, optimize resource utilization, and embrace circular economy principles by integrating innovative systems, real-time analytics, and advanced AI-driven tools. Industries dealing with complex fabric inspection processes, such as those for conveyor belts and tire cord fabrics, benefit enormously from automated systems that ensure precision and waste reduction. These technologies meet today's sustainability demands and position businesses for long-term success in a competitive and environmentally conscious market.
Robro Systems is at the forefront of this evolution, offering cutting-edge automation solutions like KWIS to the technical textile sector. By combining innovative vision systems with intelligent analytics, Robro Systems is helping manufacturers enhance quality control, minimize resource wastage, and align with eco-friendly goals. Visit our website or contact our team today to discover how Robro Systems can help your manufacturing process transition into a sustainable future.