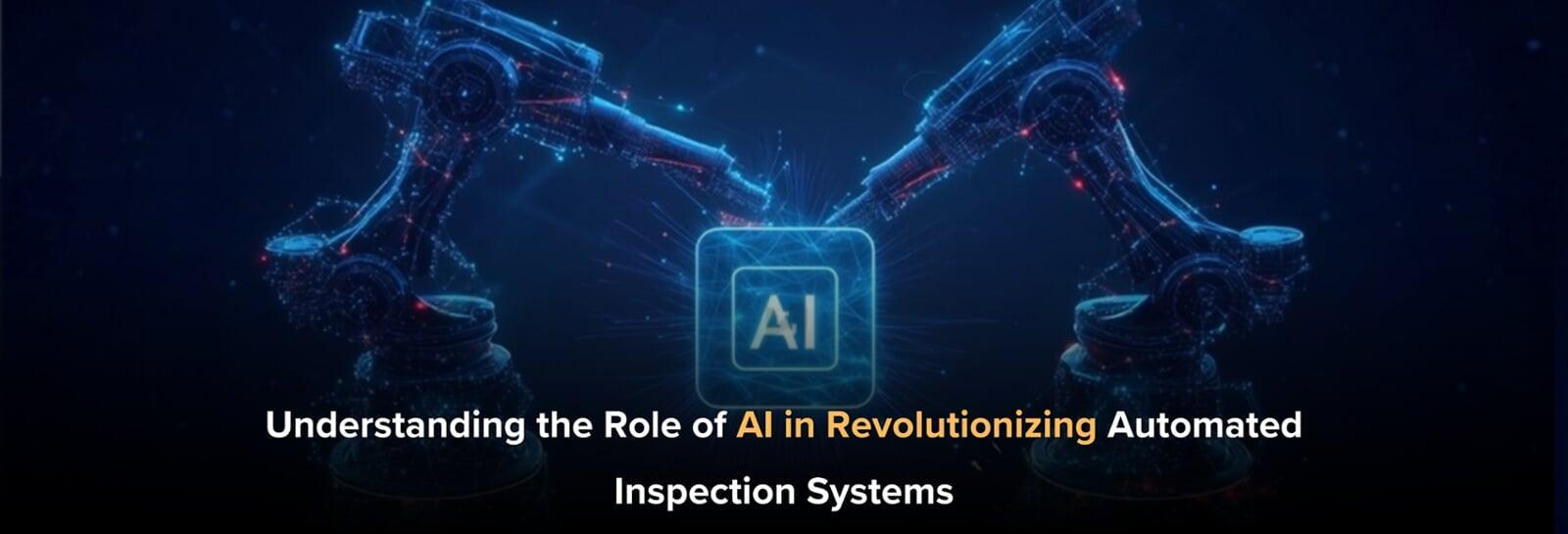
The demand for precision, speed, and reliability in industrial manufacturing is increasing, with industries such as textiles, automotive, and electronics relying on high-quality standards for optimal performance. Traditional inspection systems, while effective, are often limited by human error, speed, and the ability to detect subtle defects. With advancements in artificial intelligence (AI) and machine vision, automated inspection systems are transforming how industries manage quality control, enhance operational efficiency, and minimize waste.
In this blog, we’ll explore AI's role in revolutionizing automated inspection systems and the challenges companies face when adopting these technologies.
Key Features
AI-powered automated inspection systems enable precise and rapid defect detection, improving quality control and minimizing human error.
Real-time processing ensures immediate feedback on production lines, preventing defects from progressing through manufacturing.
AI algorithms continuously adapt and learn from new data, increasing detection accuracy.
Predictive maintenance capabilities reduce machine downtime by forecasting potential breakdowns.
Integrating AI with legacy production systems requires overcoming initial investment and system compatibility challenges.
Deep learning models, such as neural networks, enhance defect detection by recognizing complex patterns in data.
AI-powered inspection systems improve efficiency and reduce waste, delivering consistent, high-quality products.
How AI Powers Automated Inspection Systems
1) Intelligent Defect Detection- AI algorithms use machine vision and deep learning models to recognize patterns and identify product defects faster and more accurately than traditional systems. This enables systems to detect even the most minor flaws, such as thread defects, fabric texture irregularities, and material misalignments that would otherwise go unnoticed.