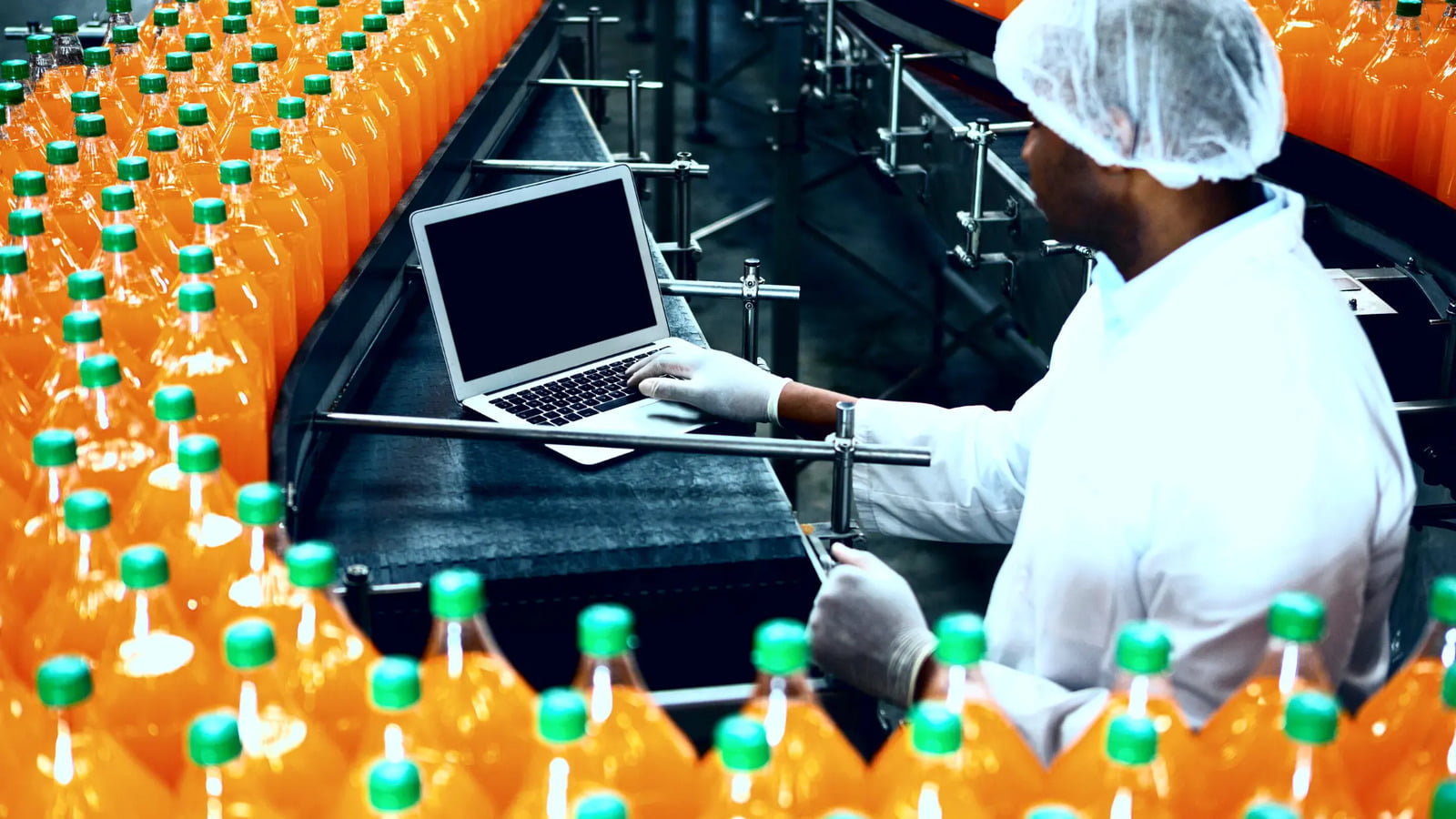
As an FMCG manufacturer, what comes to your mind when you think about a defect detection system? Are you visualizing several employees detecting defects on the production line? How reliable do you think manual inspection is? Manual inspection can be inaccurate and error-prone. Even the most experienced defect detector can miss or misidentify the accuracy of the products.
Apart from the accuracy and consistency, what about safety? Do the human inspectors wear masks and gloves at all times? How do you ensure they don’t remove their safety gears while you aren’t looking? These and several other risks are prevalent if you choose manual inspection in your factory.
Automated defect detection
Manual inspection has been used for a very long period but with digital innovation, it is time to change now. A machine vision defect detection system requires low or no human intervention and provides accurate and seamless results. Such systems are driven by artificial intelligence (AI) and are capable of identifying minute details and even the smallest errors like dents, contamination, scratches, dust particles, and many more.
Manual defect detection increases the possibility of missing small errors. Additionally, it is a labour-intensive and more expensive task. Manual inspection leaves lesser free floor space for the personnel and there is a risk of people constantly bumping into one another, which can result in petty arguments.
Human inspectors may be unable to detect minor errors like slight colour variations as they are constantly looking at the same things for an extended period. People can pay attention at a particular thing for a specific period, after which they require a break for better attention. Automated inspection systems do not have these limitations, as these are digitally influenced, ensuring accurate monitoring with the least human intervention.
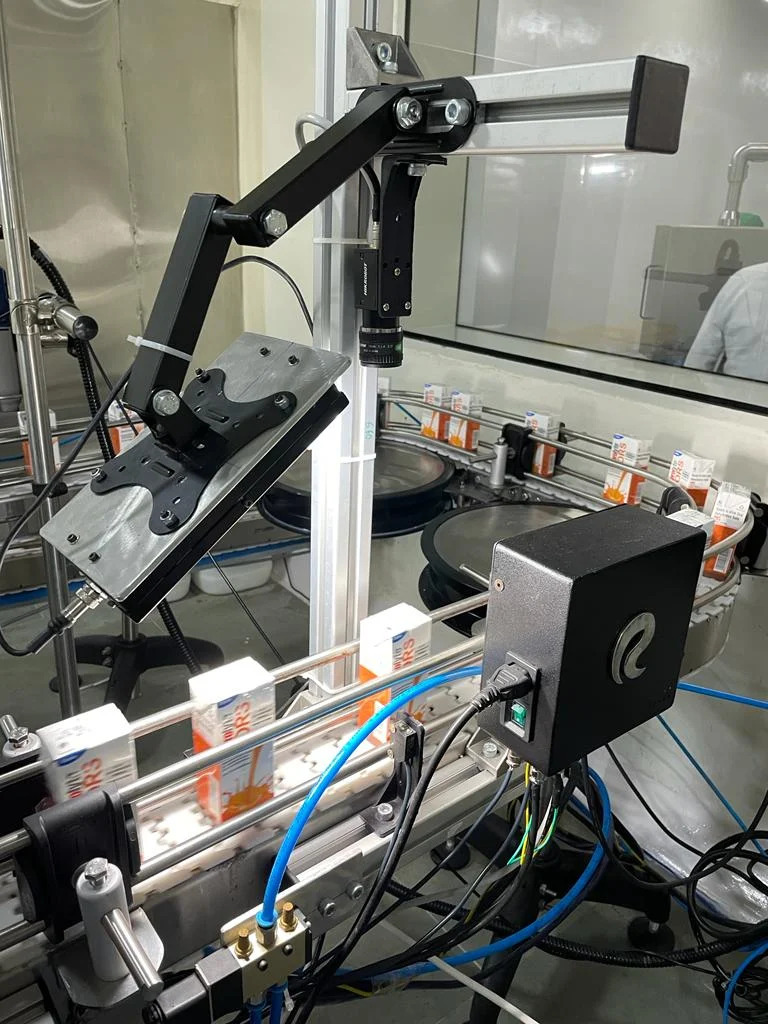
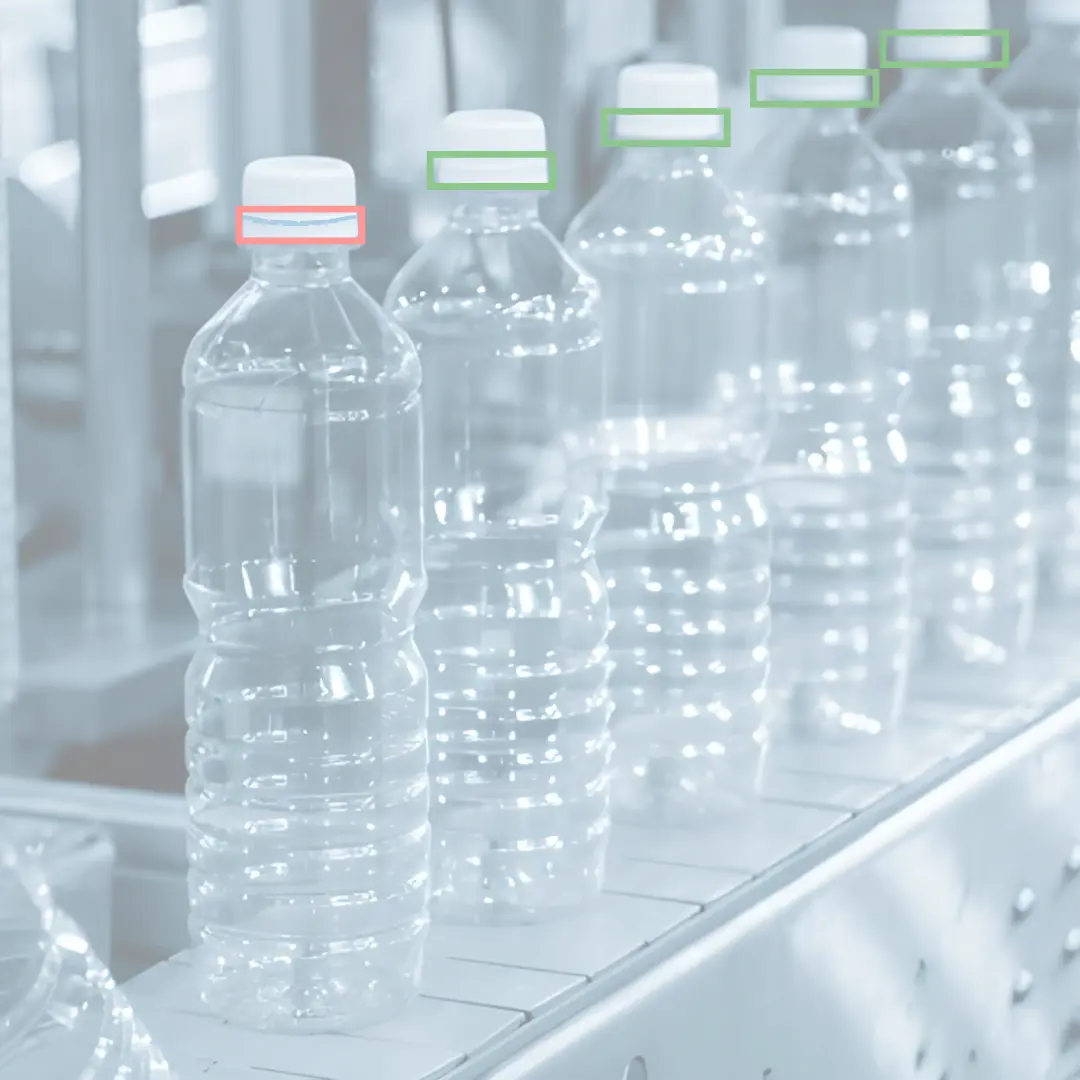
Manual inspection is neither economical nor practical. Automated vision systems offer greater accuracy, speed, and reduce wastage and costs. FMCG production is massive and human inspectors may miss minor defects. Overcoming this limitation with digital defect detection system can ensure error-free manufacturing for FMCG companies.